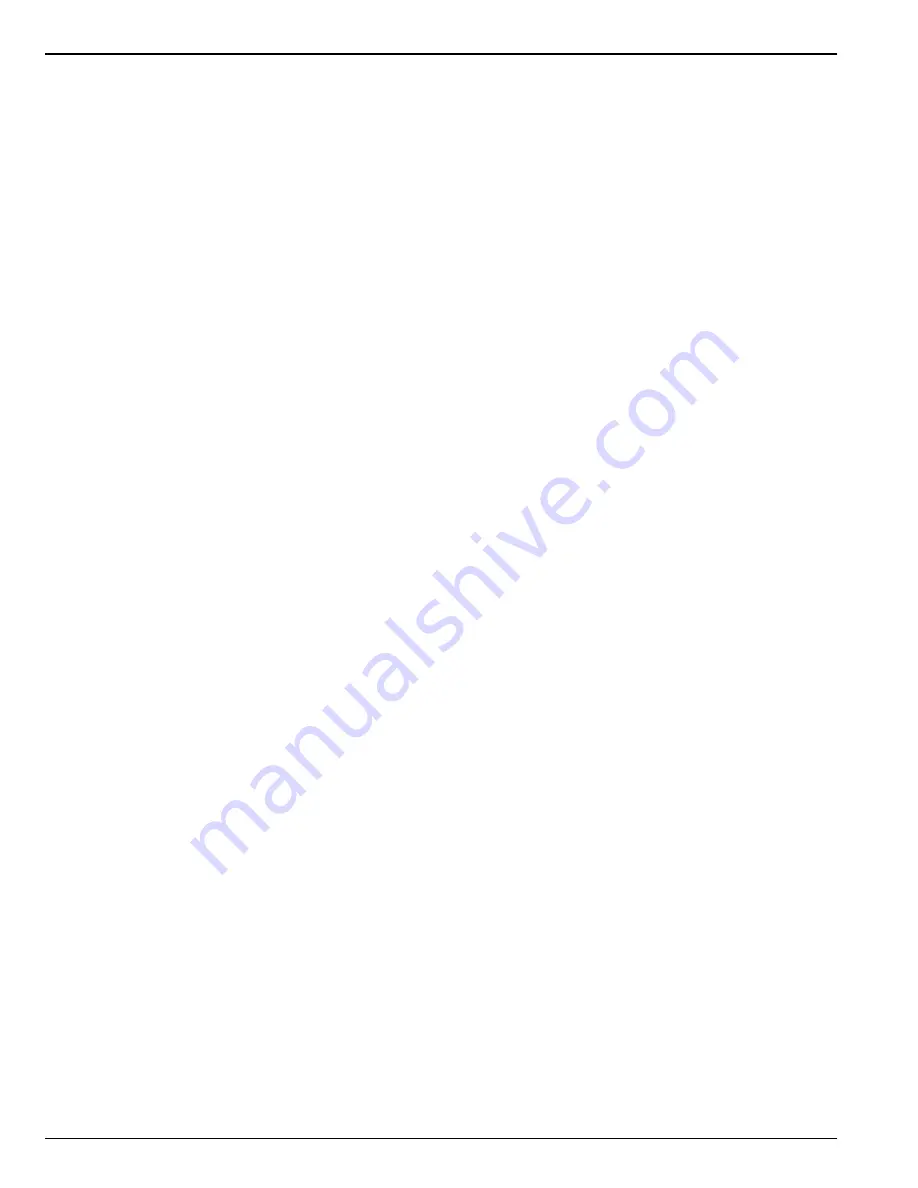
4-2
General Description
µ
P-D Controller
CSR-20 & CSR-40, September 1999
3.
Status indicator LEDs (see “Status Indicator LEDs and
Alarm Codes” in this chapter).
4.
Power Module: Low voltage control power and ground
are supplied to the
µ
P-D controller and Output Module.
The Power Module also includes:
• Modulation valve power output terminals.
• Remote monitoring connection is provided by a serial
communications port located on the side of the control
box.
• Control circuit fuse protection:
- 2 amp fuse (F1) protects the circuit to the modulation
valve.
- 1 amp fuse (F2) protects the bridge light relay (option)
circuit.
- 1 amp fuse (F3) is unused.
- 5 amp fuse (F4) protects the circuit that supplies power
to Power Module Board.
- 1 amp fuse (F5) protects the bridge light (option) circuit.
- 5 amp fuse (F6) protects the IRMU (option) circuit.
- 3 amp fuse (F7) protects the TRANSFRESH (option)
circuit.
- 2 amp fuse (F8) protects the RMM/IRMU (option) cir-
cuit.
- 3 amp fuse (F9) protects the chart recorder (option) cir-
cuit.
- 3 amp fuse (F10) protects the battery charger (option)
power input circuit.
- 7.5 amp fuse (F11) protects the Output Module circuit.
- 3 amp fuse (F12) protects the remote battery connector
circuit.
- 3 amp fuse (F13) protects the battery charger (option)
output circuit.
- 3 amp fuse (F14) protects the battery (option) circuit.
5.
Output Module: Output terminals are used to energize
and de-energize unit contactors and solenoids (see
“Output Module” in this chapter).
6.
Thermo Bus Tap circuit board: Serial communication
commands are transmitted between the controller and the
Output Module through the Thermo Bus circuit board (see
“Thermo Bus Tap” in this chapter).
7.
Replaceable sensors: Return air, supply air, evaporator
coil, condenser coil, ambient air and compressor discharge
gas temperature sensors are field replaceable (see
“Temperature Sensors” in this chapter). Four spare sensor
receptacles are also provided for USDA and PULP tem-
perature recording (optional).
8.
Defrost cycle control (see “Defrost” under Sequence of
Operation in this chapter).
9.
Internal self-checking/diagnostic capability.
10. Pretrip test capability (see “Full Pretrip Test” under Menu
Test in this chapter).
11. Sensor Check test capability (see “Sensor Check” under
General Theory of Operation in this chapter).
12. Data recording capability (see “Data Recording and
Downloading Data” in this chapter).
13. Electronic phase selection (see “Automatic Phase
Selection” under General Theory of Operation in this
chapter).
14. Power limit control (see “Power Limit” under General
Theory of Operation in this chapter).
15. Sequential component start-up control: A sequence start
of the required loads occurs during initial start-up of the
controller and when a control mode shift requires the
compressor to start (see “Sequence of Operation” in this
chapter).
16. Evaporator fan speed and condenser fan operation control
(see “Evaporator Fan Control” and “Condenser Fan
Control” under General Theory of Operation in this chap-
ter).
17. Hourmeters: The
µ
P-D controller has multiple built-in
hourmeters that can be accessed through the Display
Menu.
18. Wake-up (setpoint enable) capability: Pressing the
SELECT key (or connecting a communications cable to the
Data Port on the bottom of the control box) when 12 Vdc
battery power option is present awakens the controller.
This capability provides auxiliary power for setpoint adjust-
ment or downloading of controller data recording memory
when a three phase power source is not available. Battery
power keeps the controller energized for 1 minute unless a
key is pressed on the controller keypad.
NOTE: The battery pack connection is located on
the Power Module Board inside the control box.
19. Compressor refrigerant gas injection cycle control (see
“Compressor Liquid Injection” under General Theory of
Operation in this chapter).
20. Flash memory: Flash program memory allows the appli-
cation software to be updated without replacing a EPROM
chip on the controller. Application software can be updat-
ed in the field using a portable computer and Thermo
King flash loading program. Consequently, the field
installed application software version may have a different
revision number and may include control features not
included in the original factory installed software. If the
operation of your unit differs from the Sequence of
Operation described for your unit (both unit and customer
configuration block numbers) in this manual, check the
unit configuration number and customer configuration
number to be sure the controller is set to the proper unit
and customer configuration (see “Reviewing Application
Software Version” in this chapter).