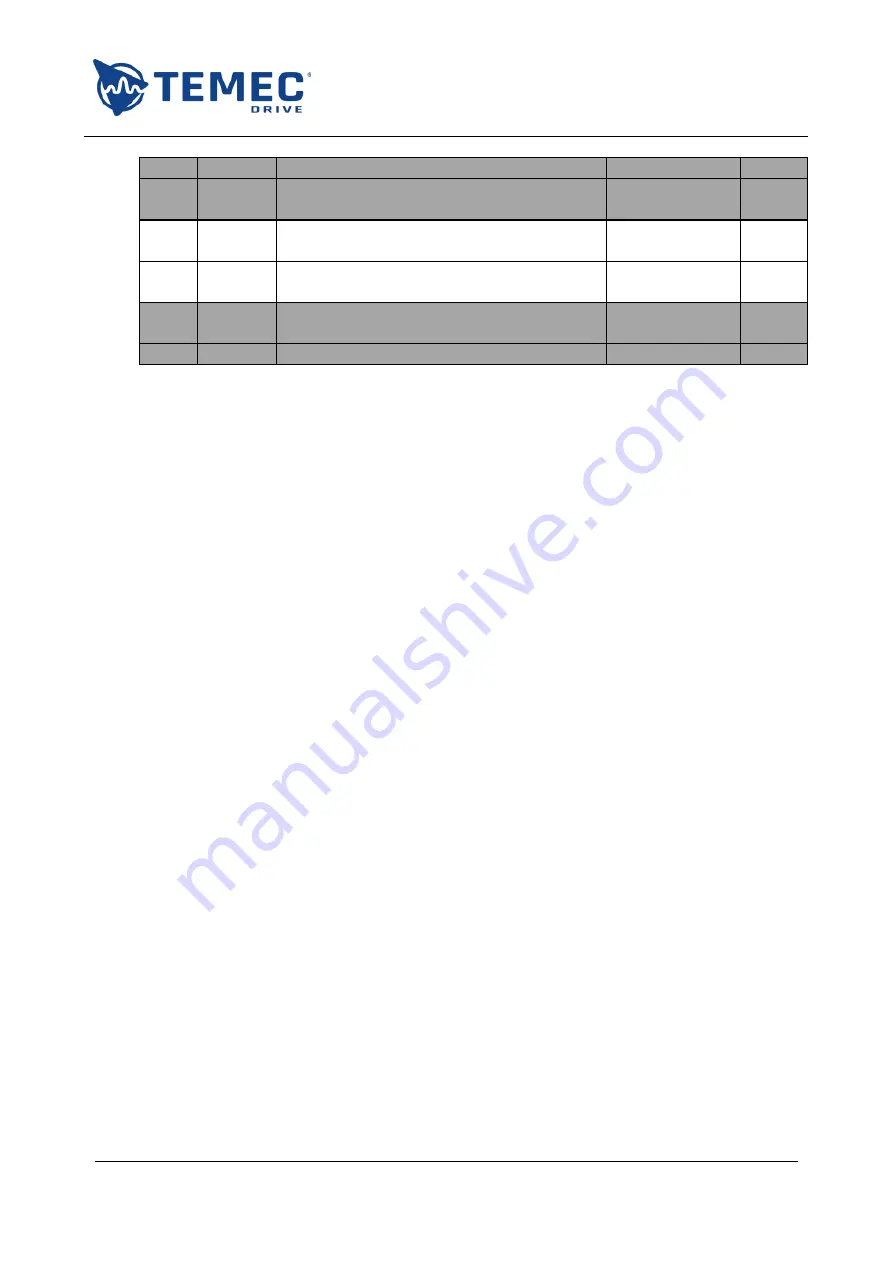
AZ
2
USER MANUAL
ST.TEC.003.EN Rev. 2.1
42 / 52
C216
Motor 2
Delay of inrush current control during closing
1 – 500 [ms]
20
C218
Motor 2
Delay added to close acceleration time before
the normal threshold is applied
100 – 1500 [ms]
1000
C219
Motor 2
Enables the block in case of overcurrent during
closing
ON / OFF
ON
C220
Motor 2
High threshold of nominal current control
during closing
1 – 11 [A]
10
C221
Motor 2
Low threshold of nominal current control
during closing
1 – 10 [A]
9
C222
Motor 2
Delay of nominal current control during closing 1 – 500 [ms]
20
Table 37: current limits parameters
Содержание AZ2
Страница 1: ...AZ2 DC MOTOR DRIVE USER MANUAL ...