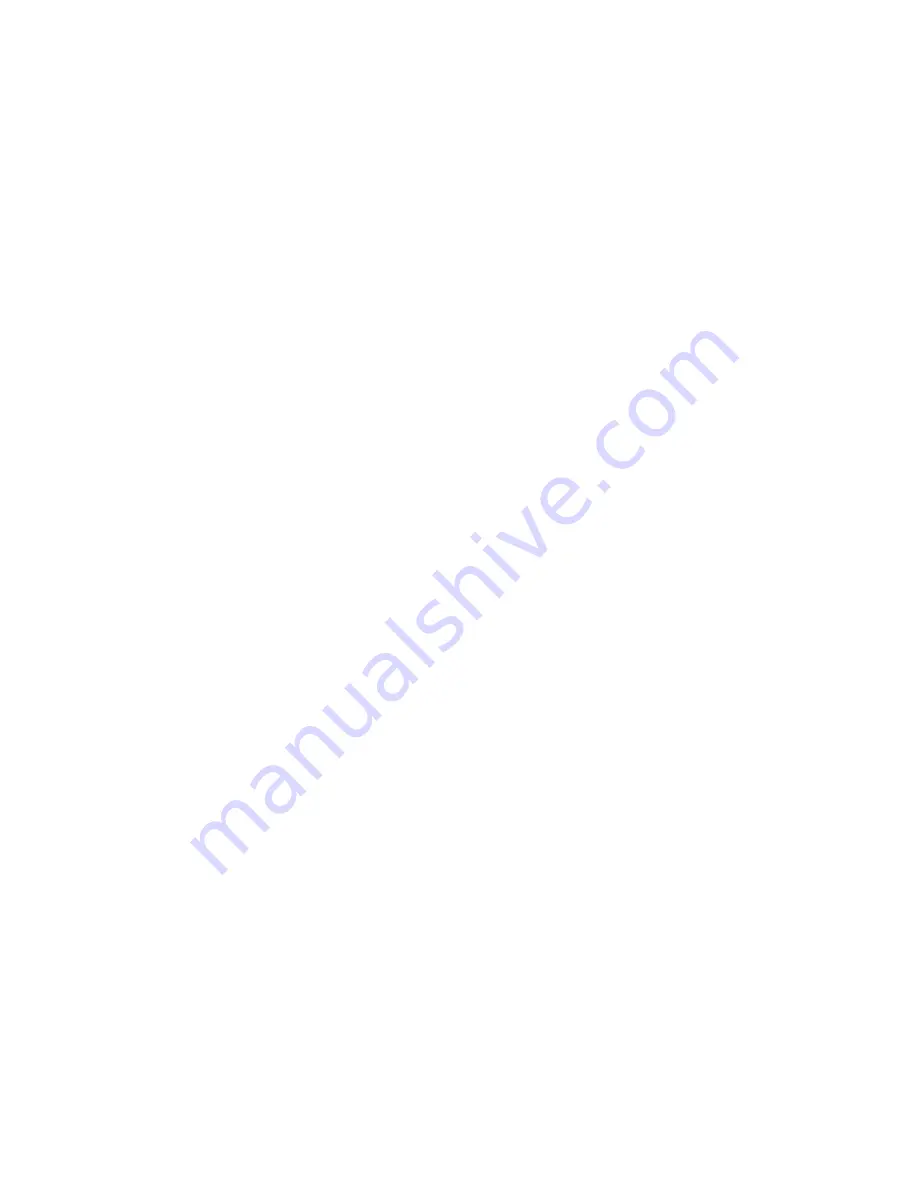
TB9100 Installation and Operation Manual
Technical Description
119
© Tait Electronics Limited May 2006
8.6
System Control Bus
The system control bus provides the following physical paths:
■
I
2
C communications between modules
■
RS-232 communications between the reciter and Calibration Software
■
fan power from the PA and PMU
■
speaker and microphone signals to and from the control panel
■
power connections for the control panel.
The system control bus has been designed so that, if a major fault occurs on
the bus, the basic operation of the base station is unaffected, but some
features will not operate correctly. For example, if the PA is disconnected
from the bus:
■
the ‘PA not detected’ alarm is generated in the reciter; however,
transmission still takes place because the transmit RF and key signals are
transmitted from the reciter to the PA via the interconnecting coaxial
cable
■
the PA is unable to turn on its fan. Depending on the ambient
temperature at the site and the transmit duty cycle, this could allow the
PA to heat up to the point where it reaches the upper temperature
threshold. At this point it will begin power foldback, protecting the
equipment from damage.
The PMU behaves in a similar way to the PA.
The system control bus has been designed to operate only within the
TB9100 subrack. It has not been designed for use outside the subrack or to
interconnect two subracks.
I
2
C Signals
The TB9100 base station uses the I
2
C bus and a proprietary software
protocol to provide communications between any modules connected to the
bus. Typically this involves the reciter assuming ‘server’ status, and PA and
PMU ‘client’ status. The reciter co-ordinates the entire subrack operation,
reading from and writing to all modules, including the control panel. The
I
2
C bus allows the reciter to perform the following functions:
■
monitoring (e.g. operating status, module details, operating temperatures
etc.)
■
diagnostics (execution of tests to confirm correct operation)
■
firmware upgrades
■
configuration (of operational parameters).
The I
2
C current source is located in the PMU so that the TB9100 base
station can operate with the control panel removed. However, the PMU
must be powered up to enable the I
2
C communications to operate. Base
stations which use the 12 V PA do not require a PMU, and in this case the
I
2
C current source is located on the base station subrack interconnect board.
Содержание TB9100
Страница 1: ...MBA 00002 05 Issue 5 May 2006 TB9100 base station Installation and Operation Manual...
Страница 6: ...6 TB9100 Installation and Operation Manual Tait Electronics Limited May 2006 Glossary 131...
Страница 26: ...26 Description TB9100 Installation and Operation Manual Tait Electronics Limited May 2006...
Страница 34: ...34 Maintenance TB9100 Installation and Operation Manual Tait Electronics Limited May 2006...
Страница 60: ...60 Installation TB9100 Installation and Operation Manual Tait Electronics Limited May 2006...
Страница 70: ...70 Base Station Operation TB9100 Installation and Operation Manual Tait Electronics Limited May 2006...
Страница 74: ...74 TB9100 Installation and Operation Manual Tait Electronics Limited May 2006...
Страница 122: ...122 Technical Description TB9100 Installation and Operation Manual Tait Electronics Limited May 2006...
Страница 126: ...126 Appendix A Interface Pin Assignments TB9100 Installation and Operation Manual Tait Electronics Limited May 2006...
Страница 130: ...130 Appendix B Inter Module Connections TB9100 Installation and Operation Manual Tait Electronics Limited May 2006...