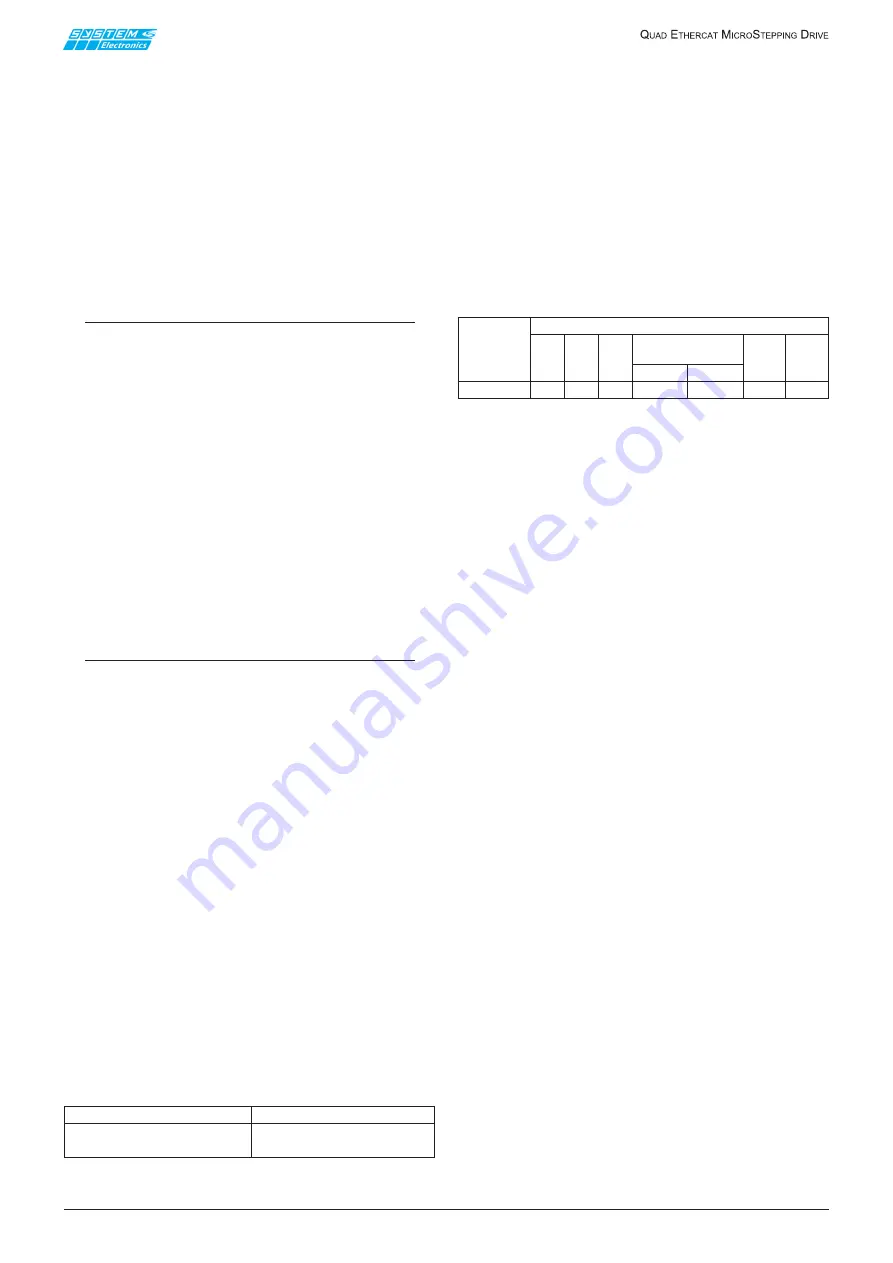
page
4
January 2020 - Rev. 1.2
Order Cod. 1902503003
•
Operating current for each motor max 10A
continuous (max 13A boost)
•
Programmable setting of the overvoltage and
undervoltage threshold to generate a fault
•
Cooling fan operated automatically by the drive
•
Management and reset of faults due to:
• Overcurrent between phases of the same motor
• Overcurrent between phases of different motors
• Short-circuit between phase and power supply
• Short-circuit between phase and GND
• Overtemperature
• Undervoltage / overvoltage.
NOTE:
Maximum surrounding air temperature 40°C.
Suitable for use on a circuit capable of delivering
not more than 5000A RMS symmetrical amperes,
176V max
Motors with rating for high voltage must be use
in coupling with this drive.
2.2 Environmental Ratings
The Quad Microstep drive unit is intended for use in
end-use application within final enclosure to maintain a
pollution degree 2 or equivalent environment.
2.3 Overvoltage Protection
These devices are intended use connected to a “Circuit
Overvoltage Category III”.
NOTE
Transient Surge Suppression Overvoltage Protec-
tion shall be externally provided in the end use
application on the Line side of the equipment by
any suitable R/C Surge-protective Devices – Com-
ponent (VZCA2/VZCA8) or a suitable “Power
Supply/System” of “Overvoltage Category II”,
rated minimum Nominal Voltage 160 V, maximum
Voltage Protection Rating VPR=2500 Vpk and
minimum Nominal Discharge Current In=5kA.
RECOMMENDED Suppressive Device model
BSPM1A150D200LV, rated 200Vdc, manufactured
by COOPER BUSSMANN (E340782).
2.4 Short Circuit Ratings and
Protection
The Short Circuit Current is referred to the maximum
Drive Power. The Stepper Motor DC Driver series Quad
Remote Microstep Driver is rated for Standard Fault
Current values in accordance with UL508C, Table 45.1,
and based on an Internal Solid State Short Circuit pro-
tection whose operation complies with Section 45.1.3
and whose manufacturing process complies with Section
64.1, 64.2 and 64.3.
Table 2.4.1
Short Circuit Protection is performed both by Internal
Solid State Short Circuit Protection and by External
Recognized Special-purpose Fuses (recommended) Pro-
tection. The fuse has been evaluated during the Short
Circuit Test also for Branch Circuit Protection.
INTERNAL SOLID STATE SHORT CIRCUIT PROTECTION
- The Drive is equipped with Solid State Short Circuit
Protection.
EXTERNAL (RECOMMENDED) PROTECTION FUSES – R/C
Special-purpose Fuses (JFHR2/JFHR8), manufactured
by COOPER BUSSMANN LLC (E91958), model
FWP-
40B
, series FWP, Fuses for protection of semiconductor
devices.
Table 2.4.2
Alternative - Any Listed Cartridge Fuses, Nonrenewable
(JDDZ/JDDZ7) or R/C Special-purpose Fuses (JFHR2/
JFHR8) with the same ratings of the above fuse, in par-
ticular with I2t and Ipeak equal or lower.
Integral solid state short circuit protection does
not provide branch circuit protection.
R/C (JHFR2/JHFR8)
Branch circuit protection fuses as indicated in
this description shall be present in the end-use
application.
2.5 Overload Protection
The equipment incorporates internal Solid State Motor
Overload protection for the motor load and speed sensi-
tive overload protection with thermal memory retention
(in comply with par. 43.1, 43.3, 43.4 and 43.5, UL508C),
therefore does not require to be used with external or
remote overload protection.
OVERLOAD IMPLEMENTATION: BY THE USER
The drive implements an algorithm for protection
against motor current overload; the user is responsi-
ble for setting the proper value of Motor rated current
parameter.
Set the variable Motor rated current for each axis
with the rated current of the motor you have. (Nominal
Current of the motor from its datasheet)
The motor can run continuously for current values below
the "rated current” set by the user.
For current ranges from 100% to 200% of the rarted
current there will be an overload if the motor will work
for 8 minutes without stopping. The motor has to run at
lower currents at least for the same time in order to cool
down properly before moving again at currents higher
than the rated one.
For current values greater than 200% the overload error
occurs within 20seconds. For current values greater than
600% the overload error occurs immediately.
Follow the installation instruction in Table 5.1.2 and
Table 5.2.1.
Model Number
Model Number
Stepper Motor DC Driver series
Quad Remote Microstep Driver
Stepper Motor DC Driver series
Quad Remote Microstep Driver
Short Circuit Current, Amp
Short Circuit Current, Amp
5,000
5,000
External (Recommended) Cartridge Fuses - Rating
External (Recommended) Cartridge Fuses - Rating
Fuse Model
No.
Fuse Model
No.
FWP-40B
FWP-40B
Vac
Vac
Vdc
Vdc Arms
Arms
500
500
500
500
40
40
Maximum Breaking
Capacity
Maximum Breaking
Capacity
ac
ac
dc
dc
50 kA
50 kA
200 kA
200 kA
I2t,
kA2sec
I2t,
kA2sec
Ip
(A)
Ip
(A)
900
900
96
96