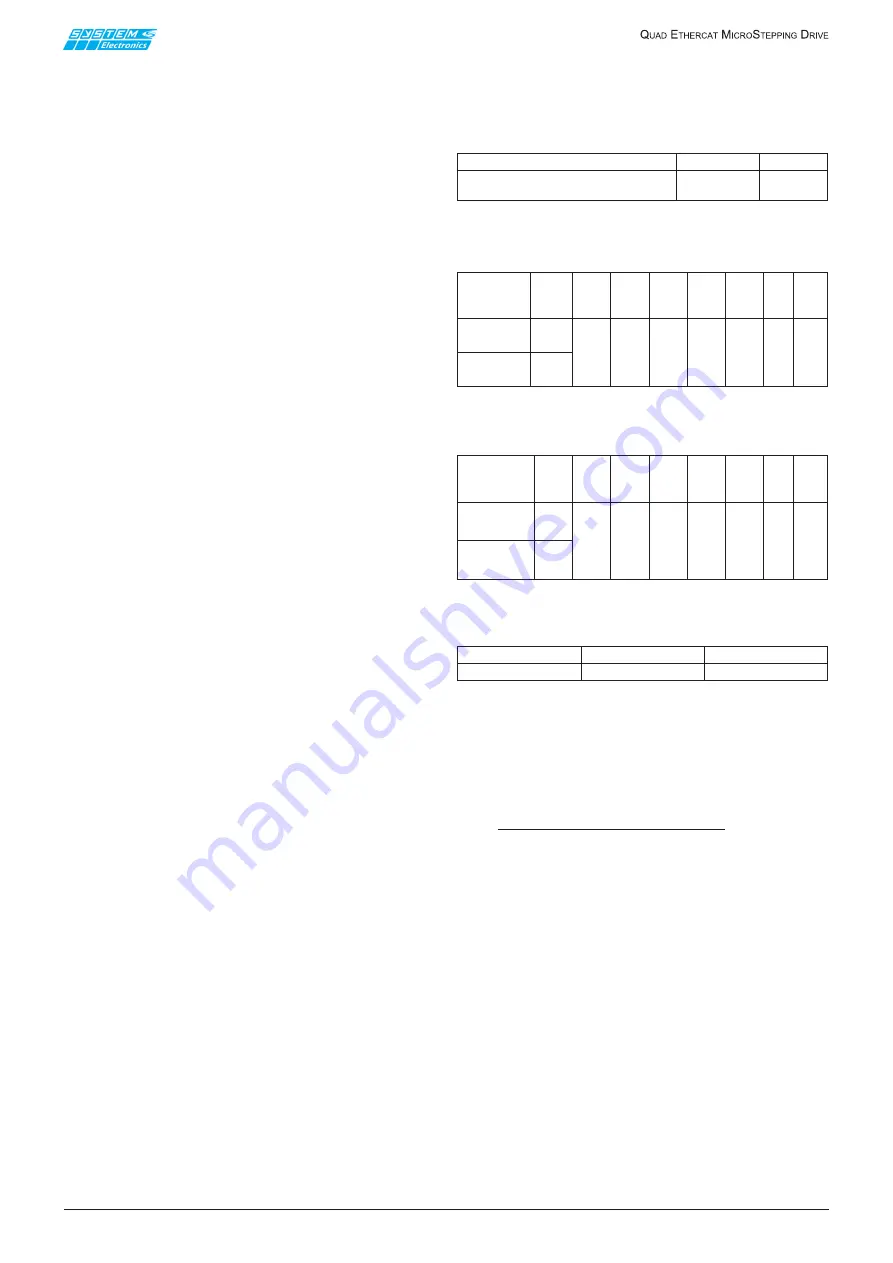
page
3
January 2020 - Rev. 1.2
Order Cod. 1902503003
1. General characteristics
The
Quad Microstep drive
unit is designed to control
and monitor up to four two-phase stepper motors,
operating in bipolar chopper mode.
The drive is equipped with a high performance trajectory
generator and with a digital control system of the
current supplied to ensure smooth and silent motor
movement.
Microstepping generation is achieved digitally and
is configurable remotely, as well as all the operating
parameters that can be varied via the field bus in use
(the use of configuration jumpers or the like is not
required).
The drive is always equipped with a
master
board
containing the global control electronics and the power
section for two motors; an
expansion
board is connected
to the master board and allows to control two additional
motors. The expansion board also provides 16 digital
24V isolated outputs and 16 digital inputs.
A front display and keyboard allow to rapidly view
the main configuration parameters and status of the
drive.
The general characteristics of the system are:
•
Open type
•
Limited dimensions: 375×190×80
•
High performance thanks to the use of Mosfet in
the power stage
•
Silent due to an operating frequency equal to
25KHz
•
Complete work parameter setting from remote
•
Front display and keyboard to verify some
operating parameters
•
Management of step fractionation up to 1/256
steps per step (for example, with motors operating
at 200 steps/revolution one can achieve positioning
resolutions up to 51200 microsteps/revolution).
The use of microstepping also allows to obtain less
motor heating and increased silentness in rotation.
The maximum generated frequency is in any case
equal to 622500 microstep/s
•
Optimal integration between the control stage,
power stage and inputs-outputs: in fact the
Microstep unit features a PMD indexer integrated
on-board, capable of handling 4 independent axes
with trapezoidal, velocity and S-curve profiles
•
16 digital 24V isolated inputs and 16 outputs
•
Control of stepper motors at 25V - 160V
max
and 1A
- 13A
•
Guards:
• Protection against short-circuit between the motor
phases
• Protection against incorrect wiring (phases not
connected)
• Protection against overtemperature
• Protection against short-circuit between a phase
and the drive power supply
•
Fault management and report
•
Remote reading of the power stage temperature
•
Remote reading of the motor supply voltage
•
Report of failure to reach the current set-point
while in motion.
•
UL certified
2. Technical specifications
2.1 Electrical ratings
1. Power Input
Terminal
Voltage
Current
+V34-GND (XT2, pin B1,B2,B3,B4)
+V12-GND (XT1, pin B10,B11,B12,B13)
160Vdc
7A
Table 2.1.1
2. Power Output
Table 2.1.2
3. OPTIONAL Power Output
Table 2.1.3
4. Control Supply 24V Input
Table 2.1.4
Power supply separated and isolated from the control
power supply and I/O
•
Motor power supply min 25V max 180V. Separate
motor power supply for pairs of motors 1-2 and 3-
4:
while maintaining the same mass
, it is possible
to power motors with different voltages or partly
disable them
•
The power supply of the pair of motors 1-2 shares
the same GND of the pair of motors 3-4. The GND
can be connected to the PE depending on the
application
•
Power section operating temperature max 90°C
•
Minimum operating temperature 0°C
•
Reading via field bus of the power stage dissipators
temperature of each pair of motors
Temperature readings “1” and “2” refer to the pair
of motors 1 - 2; temperature readings “3” and “4”
to the pair of motors 3 - 4 (motors 1 and 2 share
the same dissipator, just as motors 3 and 4)
•
Programmable setting of the dissipator
overtemperature threshold (<90°C)
•
Remote reading of the motor supply voltage
•
Protection of every single motor with fuse on the
removable front terminal board. Fuse installed:
10A F 250V
(See par. 2.6 for details)
Terminal
Output
Voltage
Current
(Arms)
per
terminal
Max
two
phases
output
current
Peak
Current
Freq.
Power
Duty
Cycle
AN1-A1-BN1-B1
XT1, pin B6,B7,
B8,B9
AN2-A2-BN2-B2
XT1, pin B2,B3,
B4,B5
Motor 1
Motor 2
Max
160Vac
7A
Max
13A
Max
155KHz
2.7hp
10A
RMS
0-100%
Terminal
Output
Voltage Current
Max
two
phases
output
current
Peak
Current
Freq.
Power
Duty
Cycle
AN3-A3-BN3-B3
(XT2, pin B9,
B10,B11,B12)
AN4-A4-BN4-B4
(XT2, pin B5,
B6,B7,B8)
Motor 3
Motor 4
Max
160Vac
7A
Max
13A
Max
155KHz
2.7hp
10A
RMS
0-100%
Terminal
XP10
Voltage
24 Vdc
Current
0.5A