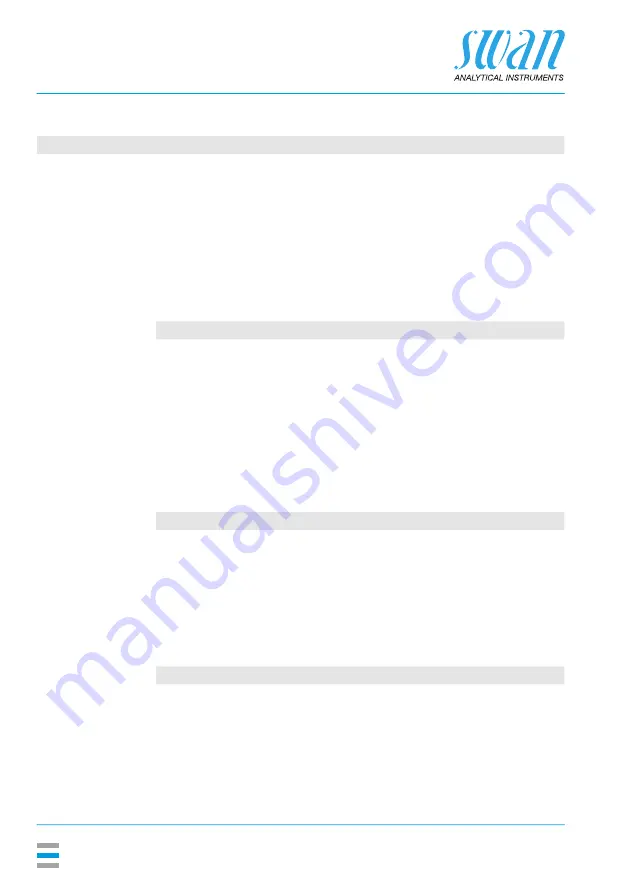
A-96.250.231 / 130421
AMI Turbitrack
Program List and Explanations
62
The relays may be used to drive control units such as solenoid
valves, membrane dosing pumps or motor valves. When driving a
motor valve both relays are needed, relay 1 to open and relay 2 to
close the valve.
5.3.2.22
Parameter
: select a process value (Meas. value, flow)
5.3.2.32
Settings:
Choose the respective actuator:
Time proportional
Frequency
Motor valve
Examples of metering devices that are driven time proportional are
solenoid valves, peristaltic pumps.
Dosing is controlled by the operating time.
5.3.2.32.20
Cycle time:
duration of one control cycle (on/off change).
Range: 0–600 sec.
5.3.2.32.30
Response time:
Minimal time the metering device needs to react.
Range: 0–240 sec.
5.3.2.32.4
Control Parameters:
Range for each Parameter same as
Examples of metering devices that are pulse frequency driven are
the classic membrane pumps with a potential free triggering input.
Dosing is controlled by the repetition speed of dosing shots.
5.3.2.32.21
Pulse frequency:
Max. pulses per minute the device is able to re
-
spond to. Range: 20–300/min.
5.3.2.32.31
Control Parameters:
Range for each Parameter same as
Dosing is controlled by the position of a motor driven mixing valve.
5.3.2.32.22
Run time:
Time needed to open a completely closed valve
Range: 5–300 Sec.
5.3.2.32.32
Neutral zone:
Minimal response time in % of the runtime. If the re
-
quested dosing output is smaller than the response time, no change
will take place.
Range: 1–20%
5.3.2.1
Function = Control upwards/downwards::
Actuator = Time proportional
Actuator = Frequency
Actuator = Motor valve