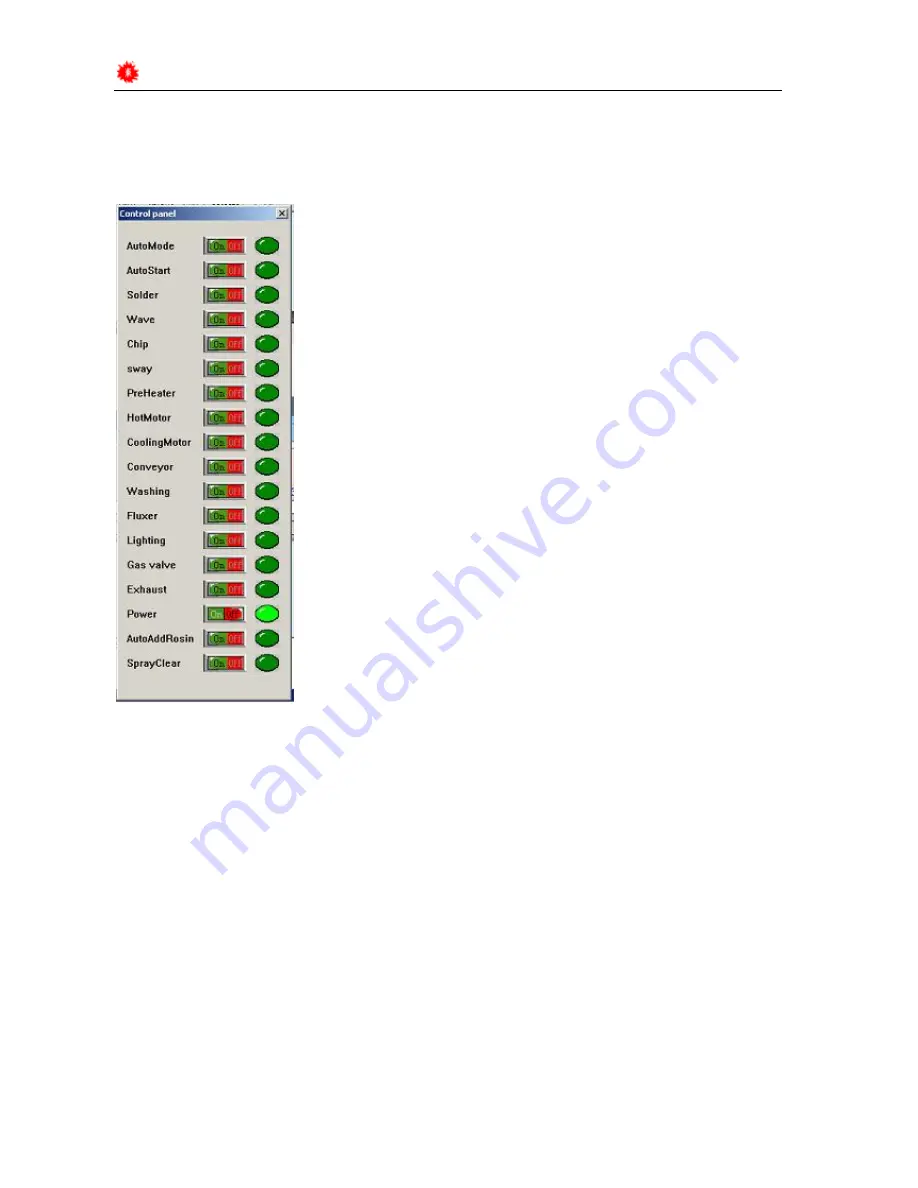
SUN EAST PEAK-350
电脑波峰焊用户手册
48 -74
operating the relevant parts.
Control Panel
The above menu will come out if you press
“
Control Panel
”
button. Below is the specific
introduction on the functional buttons.
The indicator light shows ON/OFF status of parts.
AutoMode: This switch is for automatic melting the solder.
AutoStart: This switch indicates that the soldering system will run under the automatic mode or
manual mode. Turn off the AutoStart, the other switches can be turn on or off separately. Turn
on the AutoStart, the other switches are under the control of automatic mode but you can turn
on or off the Wave and Spray motor.
Solder Pot: Temperature control of solder pot
Pre-heat: Temperature control of pre-heat zone. The hot air should work while preheating.
Wave: The existing status of the second wave
Sprayer: The existing status of the first wave.
Cooler: The cooler with cool wind cycling in the cooling zone.
Conveyor: The chain conveyor system.
Содержание PEAK-350
Страница 24: ...SUN EAST PEAK 350 23 74...
Страница 25: ...SUN EAST PEAK 350 24 74 2 Parameter Setup of Machine...