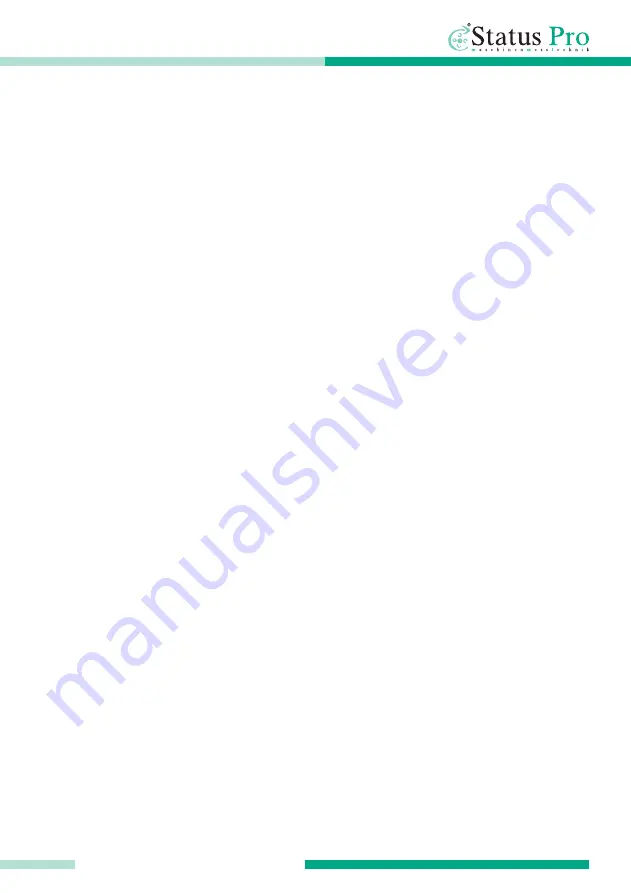
Status
Pro
–
µLine F1 User Manual
61
ADDITIONAL SOFTWARE OPTIONS
between steps will be and therefore the measurement in inclination overall will be. The
disadvantage, however, is more interaction is required to move the reflector accurately for
each step.
In the configuration menu (see fig. 64, 9.2.3) select the type of measurement method you
want (such as 'end point fit method' described earlier). The actual measurement in
straightness is then shown as a curve by the software (no measurement is perfectly
straight unless meticulously aligned beforehand).
If you have chosen more than one cycle in series, the program will then superimpose the
cycles and create a curve with mean values for all the same points in position. In certain
cases, it is also helpful to set how long each point is measured for a more automated pro-
cedure.
9.3.8 Precautions concerning Measurement with Angular
Detecting Optics
Tilt detection varies with each passage of movement. For instance, as seen with a linear
guide, the angles of each point measured on it will shift incrementally. If no displacement
occurs, i.e. no movement along the axis is performed, the system will re-create a parable
for that point instead of a curve (the increment becomes exponential as it still measures a
shift in angle). Therefore, it is vital to get the same distance (or velocity) for each point on
the guideway, bearing way or rail as the case may be.
Theoretically, this type of measurement is particularly accurate but also potentially hard to
control. For precise measurement make sure the optics are perfectly perpendicular to the
laser as possible and distances (integrals between points) are measured with utmost
accuracy. In this way, measurement can theoretically be reproduced within a tolerance of
< 0.5 µm/m.