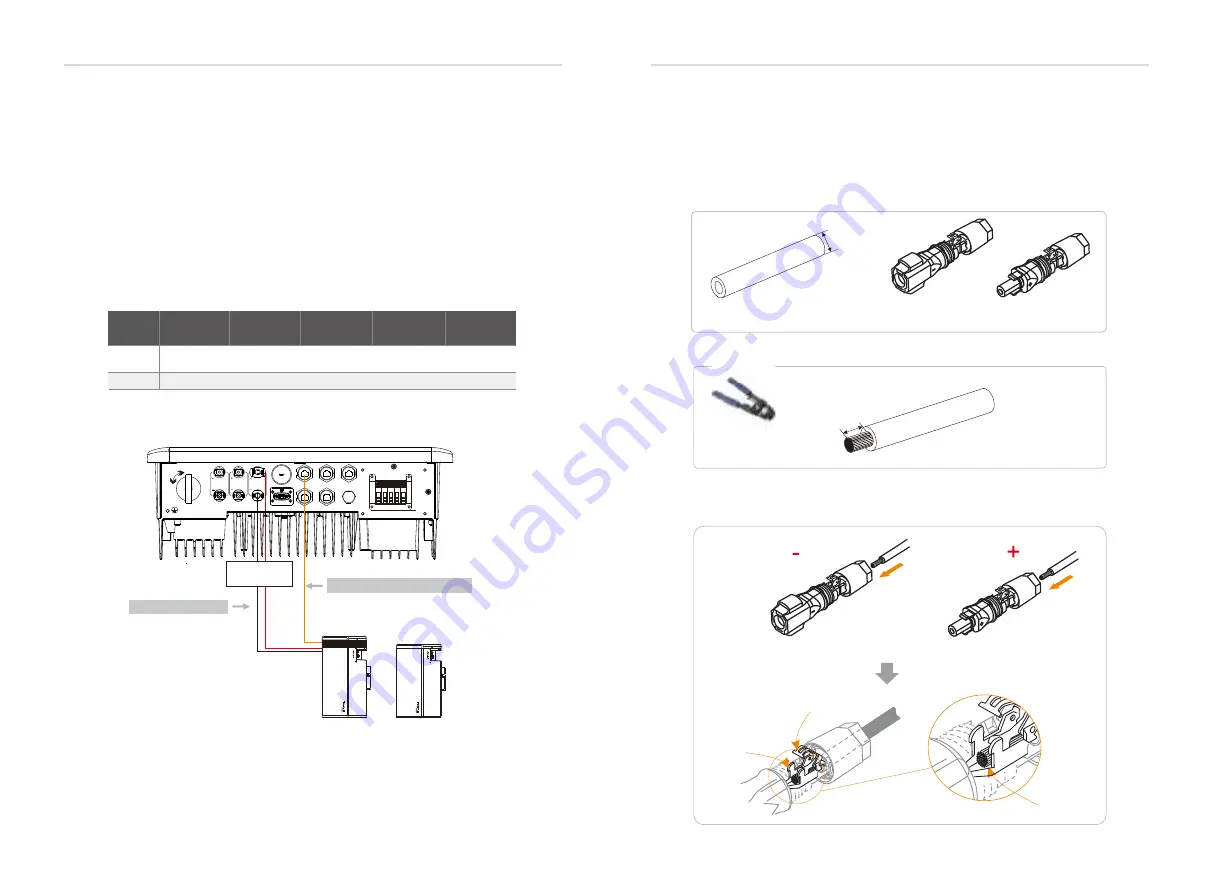
Ø
Battery Breaker
Voltage
Current[A]
32 A
Model
X1-Hybrid-3.0-D
X1-Hybrid-3.0-M
X1-Hybrid-3.7-D
X1-Hybrid-3.7-M
X1-Hybrid-5.0-D
X1-Hybrid-5.0-M
X1-Hybrid-6.0-D
X1-Hybrid-6.0-M
Ø
Battery connection diagram
High voltage lithium battery
- +
CAN/RS485
Non-polar
DC MCB
Power line connection
Communication line connection
... ...
Ø
Battery connection steps
Step 3.
Insert the stripped cables into the DC plug (-) and DC Plug (+)
respectively.
DC plug (-)
DC plug (+)
Step 2.
Strip the insulation layer (length:15 mm) at one end of the power line.
Diagonal pliers
Step 1.
Prepare 8 mm battery power line, find the DC plug (+), DC plug (-)
in the accessory bag.
BAT plug (+) BAT plug (-)
15 mm
Spring
Cavity
The cable must pass through here
8 mm
Power line
Ø
Connection requirements
X1-Hybrid-7.5-D
X1-Hybrid-7.5-M
Electrical Connection
Electrical Connection
5.4 Battery Connection
ON
OFF
PV 1
PV 2
BAT
BMS
CAN
DRM
Meter/CT
COM/LCD
B
attery port connection line of the X1-Hybrid G4 M series
inverter is on the X1-Matebox, just connect it. It is necessary to
wire the D series according to the following steps.
46
47
Upgrade
/
Dongle
X1-Hybrid G4 series inverter charge and discharge system can be
equipped with high voltage lithium battery and lead acid battery.
Please note that the maximum voltage of the battery should not
exceed 480 V, battery communication should be compatible with the
Before connecting the battery, a non-polar DC MCB must be installed to
ensure safety.
Before maintenance, the inverter need to be safely disconnected.
Notice:
When using SolaX batteries, it is recommended that the number
of battery control (T-BAT-5.8) is 1 and the number of battery
modules (HV11550) is 0-2; the number of battery control (MC0600)
is 1 and the number of battery modules (HV10230) is 1-4 pcs.
Nominal voltage of DC breaker should be larger than maximum
voltage of battery.
Содержание X1-Hybrid
Страница 59: ......