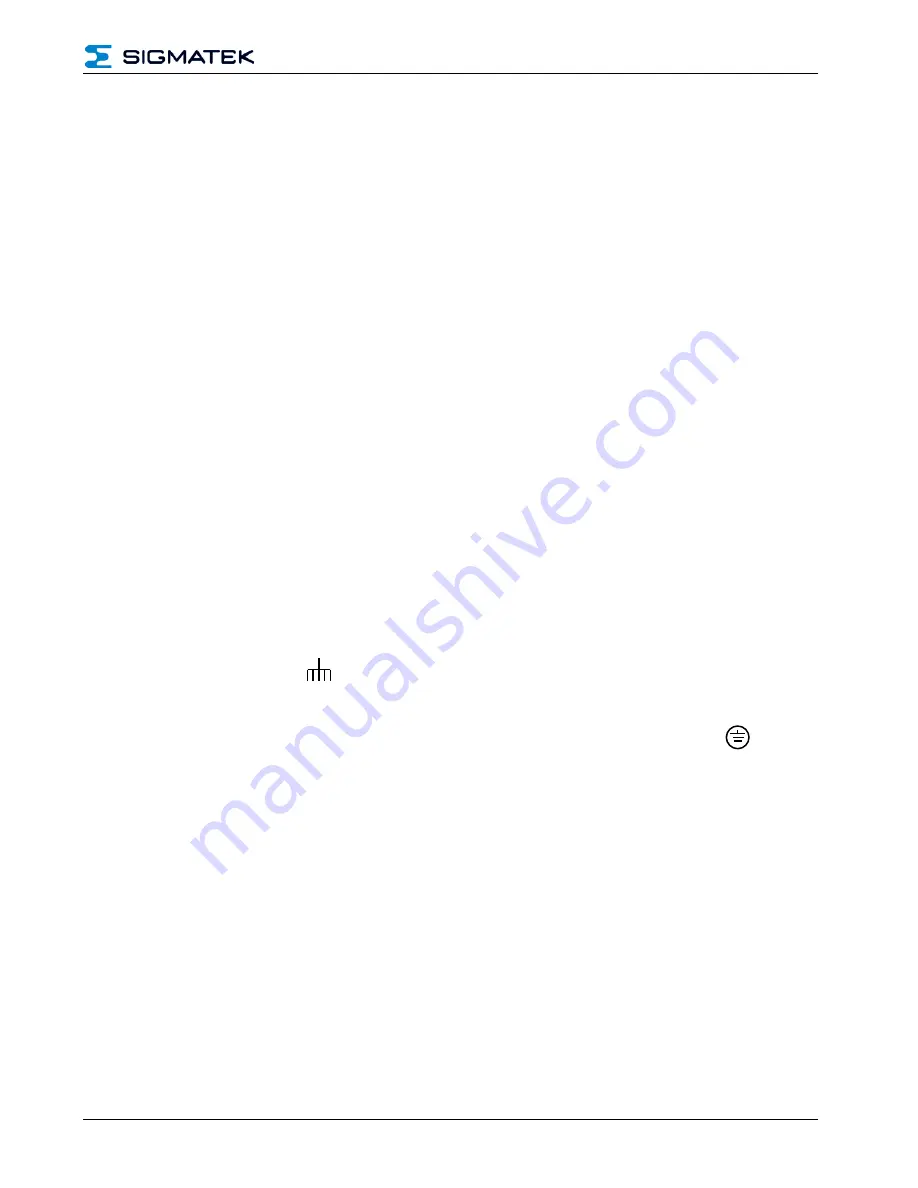
DIAS-DRIVE 335-23
27.09.2017
Page 23
•
The rated voltage and current of the servo motor and servo amplifier must match. The
electrical connection must correspond to the schematic on page 24.
•
The main supply can under no circumstances exceed the rated values for the servo
amplifier.
“Voltage Supply Options”
on page 31 should be noted.
•
The external fuse for the main supply, the +24 V auxiliary and holding brake supply
must meet the specifications for
“External fusing”
on page 30.
•
The motor and control cable should be routed with a minimum clearance of 100 mm.
This improves the effect of noise in the control cable, which is caused by the high noise
generation of the motor cable. A shielded motor and feedback cable must be used, by
which the shielding on both cable ends is applied.
•
As described on page 26, the correct mounting position is vertical.
•
The ventilation in the control cabinet must provide sufficient cool and filtered air.
Information on the
“Environmental conditions, ventilation and mounting”
can be
found on page 21.
•
Any subsequent changes to a servo amplifier will render the warranty void
, with
exception of the parameter settings.
•
During the initial start-up of the servo amplifier, the peak current must be tested. small
motors can be damaged quickly, especially if the servo amplifier settings are to high
(e.g. a 1 A motor with a 10 A amplifier without being limited to 1 A).
•
Note: The mass symbol
found in all schematic plans means that the electric
connection between the indicated device and the mounting panel in your control
cabinet must be made over the largest possible surface. This connection should enable
the dissipation of HF noise and should not be confused with the PE symbol
.
(Protective measure according to EN 60204)
•
Storage time:
< 1 year:
no limitations
≥ 1 year:
The intermediate circuit capacitors of the servo amplifier must be reformed
before the initial startup. In addition, all electrical connections must be removed and the
servo amplifier supplied with 230 V AC, single phase at terminals L1 / L2 for 30
minutes.
Содержание DIAS-Drive 335-23
Страница 1: ...DIAS Drive 335 23 Date of creation 01 10 2013 Current version 27 09 2017 Article No 10 501 351 23E...
Страница 12: ...DIAS DRIVE 335 23 Page 10 27 09 2017 1 3 Servo Amplifier Components...
Страница 17: ...DIAS DRIVE 335 23 27 09 2017 Page 15 1 8 Block Diagram...
Страница 62: ...DIAS DRIVE 335 23 Page 60 27 09 2017 6 2 2 Dimensions incl Mounting Set...
Страница 67: ...DIAS DRIVE 335 23 27 09 2017 Page 65 7 2 Mechanical Dimensions Integrated into the SDD3xx servo amplifier...
Страница 82: ...DIAS DRIVE 335 23 Page 80 27 09 2017...
Страница 94: ...DIAS DRIVE 335 23 Page 92 27 09 2017...