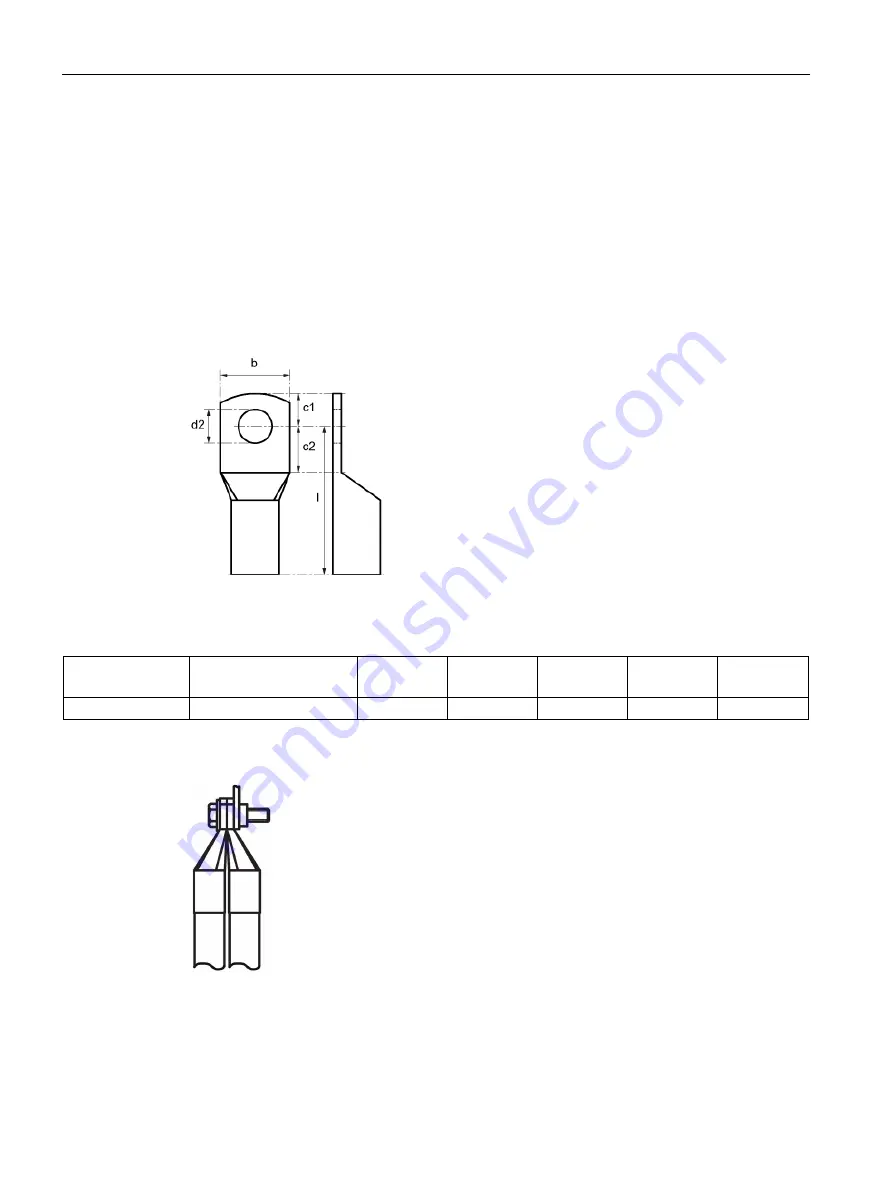
Connecting up, switching on
4.1 Cable lugs
Power Module PM330
32
Hardware Installation Manual, 12/2018, A5E32844552B AF
4.1
Cable lugs
Cable lugs
The cable connections on the devices are designed for cable lugs according to DIN 46234 or
DIN 46235.
For connection of alternative cable lugs, the maximum dimensions are listed in the table
below.
These cable lugs are not to exceed these dimensions, as mechanical fastening and
adherence to the voltage distances is not guaranteed otherwise.
Figure 4-1
Dimensions of the cable lugs
Table 4- 1
Dimensions of the cable lugs
Screw / bolts
Connection cross-section
[mm²]
d2
[mm]
b
[mm]
l
[mm]
c1
[mm]
c2
[mm]
M12
240
13
42
92
24
13
The cable lugs can be attached as shown in the following diagram if, at one connection per
phase, two cable lugs can be connected.
Figure 4-2
2 cable lugs per connection
Содержание PM330
Страница 1: ......
Страница 2: ......
Страница 8: ...Table of contents Power Module PM330 6 Hardware Installation Manual 12 2018 A5E32844552B AF ...
Страница 20: ...Introduction Power Module PM330 18 Hardware Installation Manual 12 2018 A5E32844552B AF ...
Страница 146: ...Appendix A 6 Abbreviations Power Module PM330 144 Hardware Installation Manual 12 2018 A5E32844552B AF ...
Страница 149: ......
Страница 150: ......