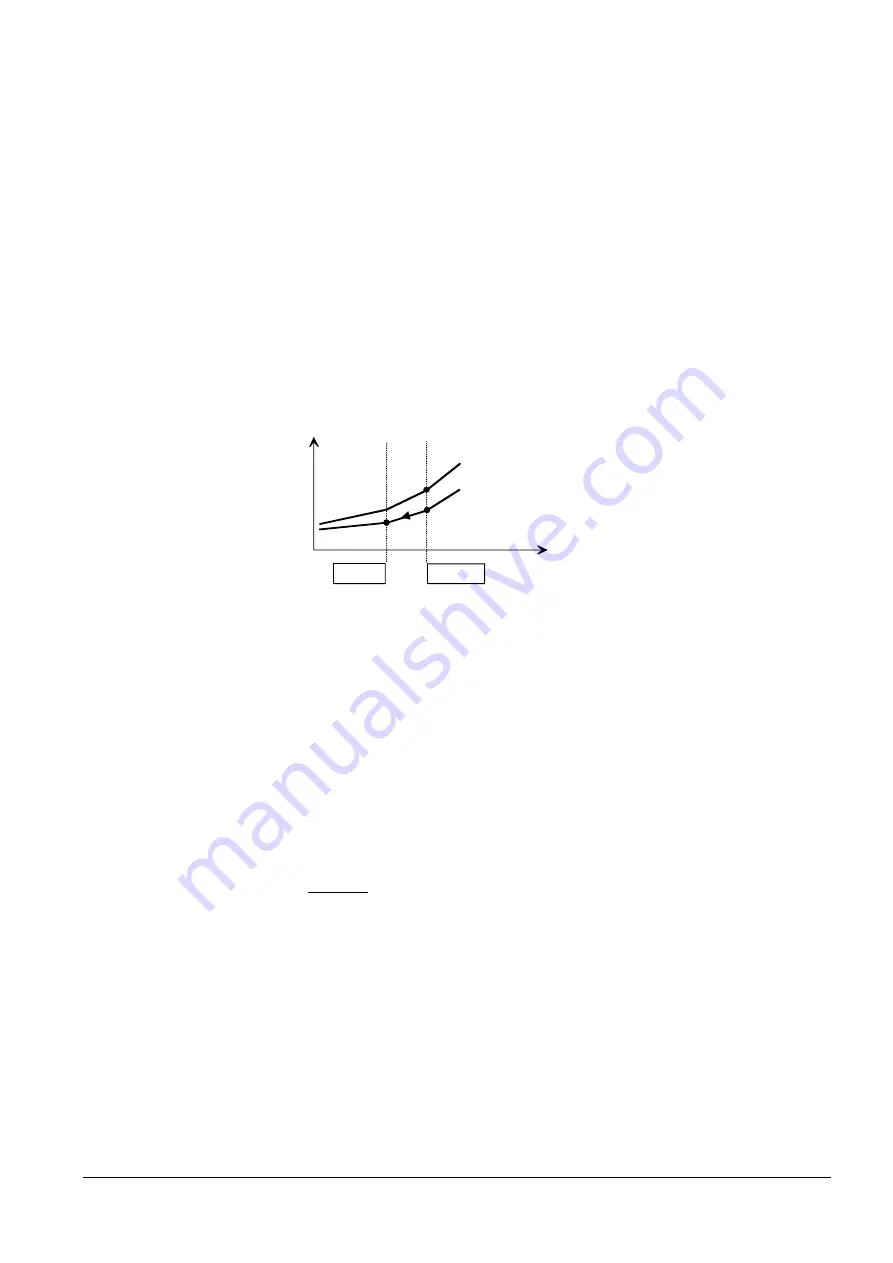
265/301
Siemens Building Technologies
Basic Documentation LMV5...
CC1P7550en
HVAC Products
19 Addendum 4: LMV52... with O2 trim control and O2 module
13.08.2004
19.2 Functioning principle of O2 trim control
The residual oxygen control system reduces the amount of combustion air depending
on the control differential (O
2
setpoint minus actual O
2
value). The amount of combus-
tion air is normally influenced by several actuators and, if used, by a VSD.
Reduction
of the amount of air is reached by reducing the «air rate» of the air-influencing
actuators.
For that purpose, the damper positions of these actuators are calculated
from some other load point on the ratio curves. Hence, due to the parameterized ratio
curves, the air-influencing actuators are in a fixed relation to one another.
O
2
trim control is supported by
precontrol,
which calculates the air rate reduction in a
way that the controller calls for the same manipulated variable as long as environ-
mental conditions do not change, irrespective of burner output. Consideration is given
to a number of measured values that are ascertained when the burner is set. This
means that the controller must only become active when environmental conditions
(temperature, pressure) change, and not when the burner load changes.
19.2.1
Air rate reduction
Positioning angle (°)
Load (%)
75
50
d
34
e/
0
903
Fuel damper
Air damper
Air rate
Fuel rate
Due to the air rate reduction, the O
2
trim controller reduces the amount of air. For that
purpose, the air-influencing actuators will travel to a smaller load (air rate) on the ratio
curve. On the ratio curve, fuel rate and air rate are the same.
Example: If the air rate is 50 % of the fuel rate, half the amount of air is delivered to the
burner (if
λ
is the same at all curvepoints) compared to the ratio curve.
19.2.2
Definition of O2 setpoint
Using the ratio curve as a basis, the O
2
setpoint is set by manually lowering the air
rate.
⇒
The system stores the O
2
ratio value, the O
2
setpoint and the relative air rate reduc-
tion (standardized value required to attain the O
2
setpoint).
Example:
With a relative air rate reduction of 10 %, the air rate must be changed by
6 percentage points from 60 % to 54 %.
By measuring both O
2
values and by having the relative air rate reduction required for
the readjustment, the system identifies the burner’s behavior. Effects such as the fan
pressure’s impact on the amount of gas are taken into consideration.