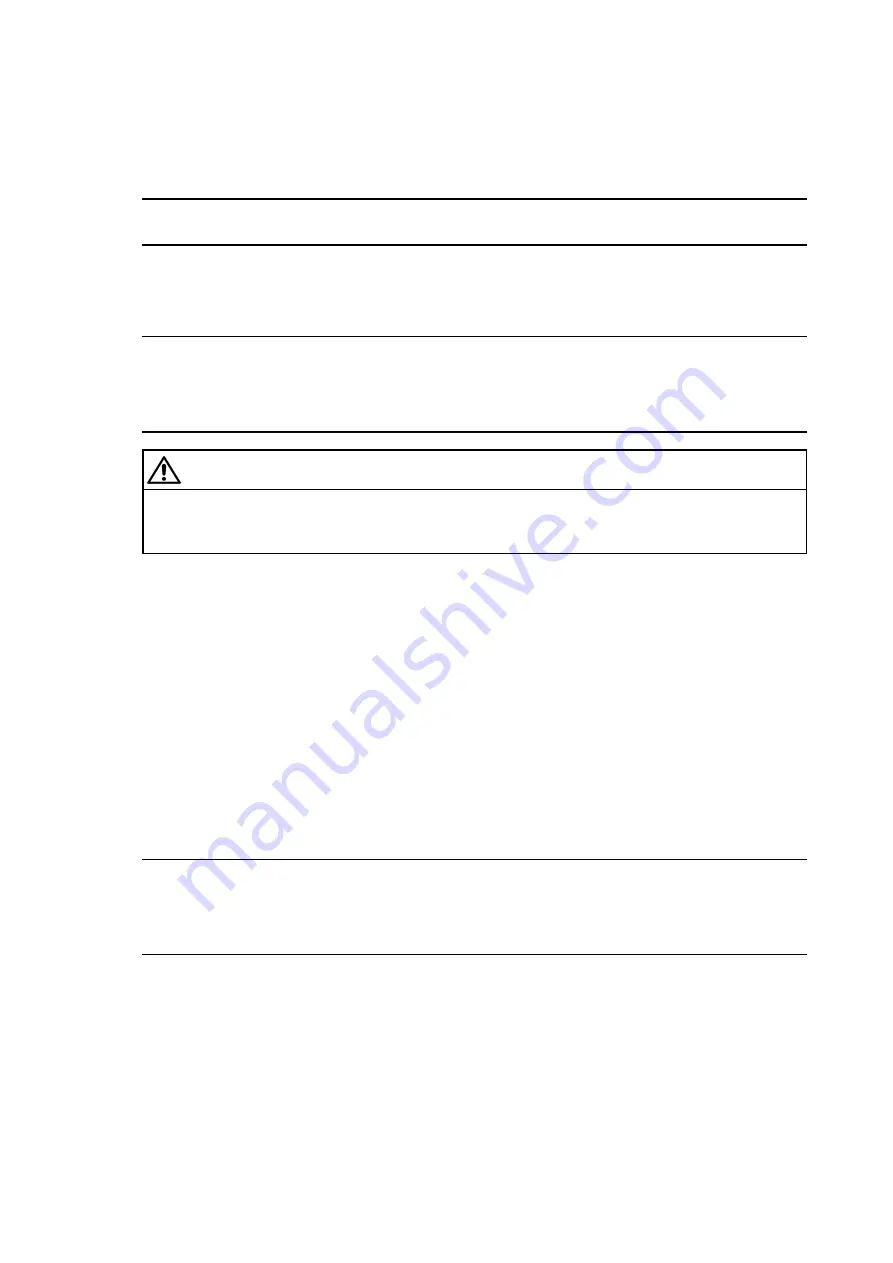
BA 5846 en 05/2015
6.11
Gear unit with separate oilsupply system
•
Remove the plugs out of the suction and delivery lines prior to connecting the system.
•
Fit the system to the gear unit or install it separately, in accordance with the drawings supplied in the
gearunit documentation.
•
The pipework must not be overstressed during the fitting procedure.
Note
Consult operating instructions for oilsupply system.
6.12
Electric connections
Wire up the monitoring devices and electrical components on the gear unit in accordance with the terminal
diagram.
Note
Electrical lines and the motors and monitoring equipment must be connected electrically in accordance
with terminal diagrams, lists of equipment and general regulations.
Electrical equipment for regulation and control must be wired in accordance with the equipment
suppliers’ instructions and Directive 94/9/EC.
WARNING
Risk of injury through electric shock
Risk of injury through electric shock when connecting up electrical components.
Before connecting up equipment, ensure that they are voltagefree.
6.13
Gear unit with heating
•
Wire the heating system electrically.
•
Wire the oillevel monitors for the heating rods (in EXversion) electrically.
6.14
Gear unit with oiltemperature monitoring system
•
Wire the temperature monitor electrically.
6.15
Oillevel monitoring system
•
Wire the oillevel limit switch electrically.
6.16
Bearingmonitoring system
•
The bearingmonitoring device must be fitted by the customer.
6.17
General notes on addon components
Note
For operating and servicing the components described in section 5, the corresponding operating
instructions and the specifications in section 6 must be observed.
For technical data and control information, refer to the data sheet and/or the orderspecific list of
equipment.