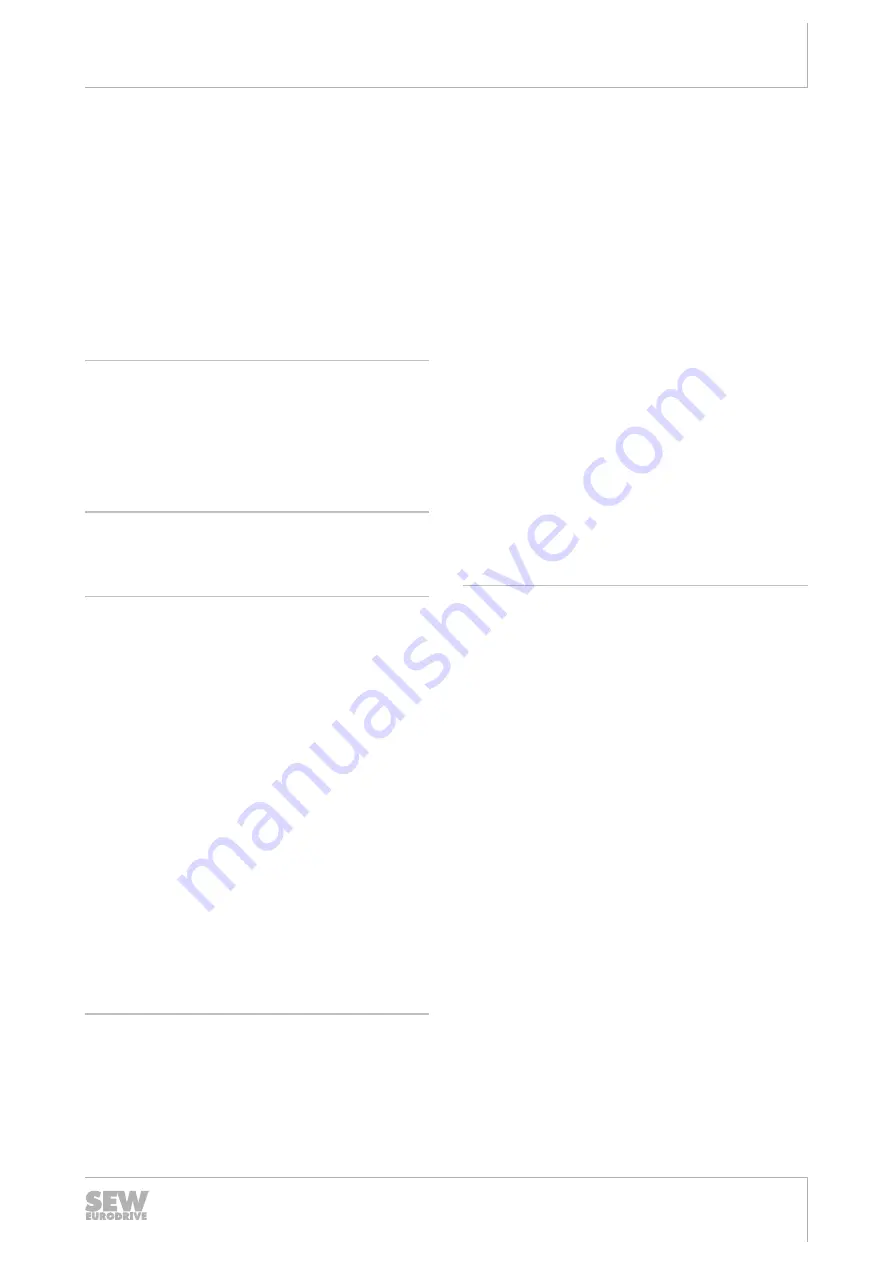
Index
Ethernet 1 ............................................................ 36
Ethernet 1 system bus......................................... 36
Ethernet 2 ............................................................ 37
Ethernet communication...................................... 52
Ethernet switch, integrated .................................. 54
Auto-crossing ................................................. 55
Auto-negotiation ............................................. 55
Multicast handling........................................... 55
Exclusion of liability ............................................... 8
F
Freely programmable controller
Performance class "advanced" ...................... 12
Performance class "standard" ........................ 12
Functional safety technology
Safety note ..................................................... 10
H
Hazard symbols
Meaning............................................................ 6
I
Information
Designation in the documentation .................... 6
Installation
In MOVITRAC
®
B ........................................... 24
In the MOVIAXIS
®
master module.................. 23
Introduction
Additional documentation ............................... 11
Content of this manual ................................... 11
IP address ........................................................... 55
IP address parameters EtherNet/IP / Modbus/TCP .
Deactivating/activating DHCP ........................ 59
Initial startup ................................................... 59
Resetting IP address parameters................... 60
IP address parameters via DCP .......................... 58
Initial startup ................................................... 58
Resetting IP address parameters................... 58
L
L15 LED (PIO) ..................................................... 67
LED H1/H2 .......................................................... 63
LED L1 (CAN 1 status) ........................................ 63
LED L10 (24 V / I/O OK)...................................... 65
LED L13 (BUS FAULT) - DeviceNet ................... 68
LED L13 (BUS FAULT) - PROFINET .................. 69
LED L13 (NETWORK STATUS) - EtherNet/IP.... 71
LED L14 (BIO) - DeviceNet ................................. 68
LED L14 (MODULE STATUS) - EtherNet/IP....... 71
LED L14 (RUN) - PROFINET .............................. 70
LED L16 (MOD/NET)........................................... 67
LED L17 (PROFIBUS fault) ................................. 66
LED L18 (RUN PROFIBUS) ................................ 66
LED L2 (CAN 2 status) ........................................ 64
LED L3 (IEC program status) .............................. 64
LED L4 (controller status).................................... 64
LED L5 (user) ...................................................... 64
LED L6 – L9 (DIO n/m)........................................ 65
LEDs
DH.21B/41B ................................................... 63
DHF21B/41B .................................................. 65
DHR21B/41B.................................................. 69
Lifting applications ............................................... 10
Link/activity LED - EtherNet/IP ............................ 72
Link/activity LED - PROFINET............................. 71
M
MAC address....................................................... 55
Mechanical installation
In MOVIDRIVE
®
MDX61B .............................. 17
In the MOVIAXIS
®
MXM master module ........ 19
In the stand-alone housing ............................. 17
MOVIAXIS
®
master module
Connecting a voltage supply .......................... 23
Connecting the system bus ............................ 23
Installing DH.21B/41B .................................... 23
MOVIDRIVE
®
MDX61B
Connecting the system bus ............................ 22
Installing and removing DH.21/41B................ 18
Installing DH.21B/41B .................................... 17
MOVITOOLS
®
MotionStudio
Communication channels ............................... 44
Communication ports ..................................... 54
Configure unit ................................................. 48
Creating a project ........................................... 45
Designated use .............................................. 44
Establishing communication........................... 45
Functions........................................................ 44
Reading/changing device parameters............ 60
Setting the connection mode.......................... 46
Starting up unit ............................................... 61
Tasks.............................................................. 44
22900055/EN – 08/16
Manual – DHE/DHF/DHR21B (standard) and DHE/DHF/DHR41B (advanced)
85
Содержание DH 21B Series
Страница 2: ...SEW EURODRIVE Driving the world ...
Страница 88: ......
Страница 89: ......
Страница 90: ......
Страница 91: ......