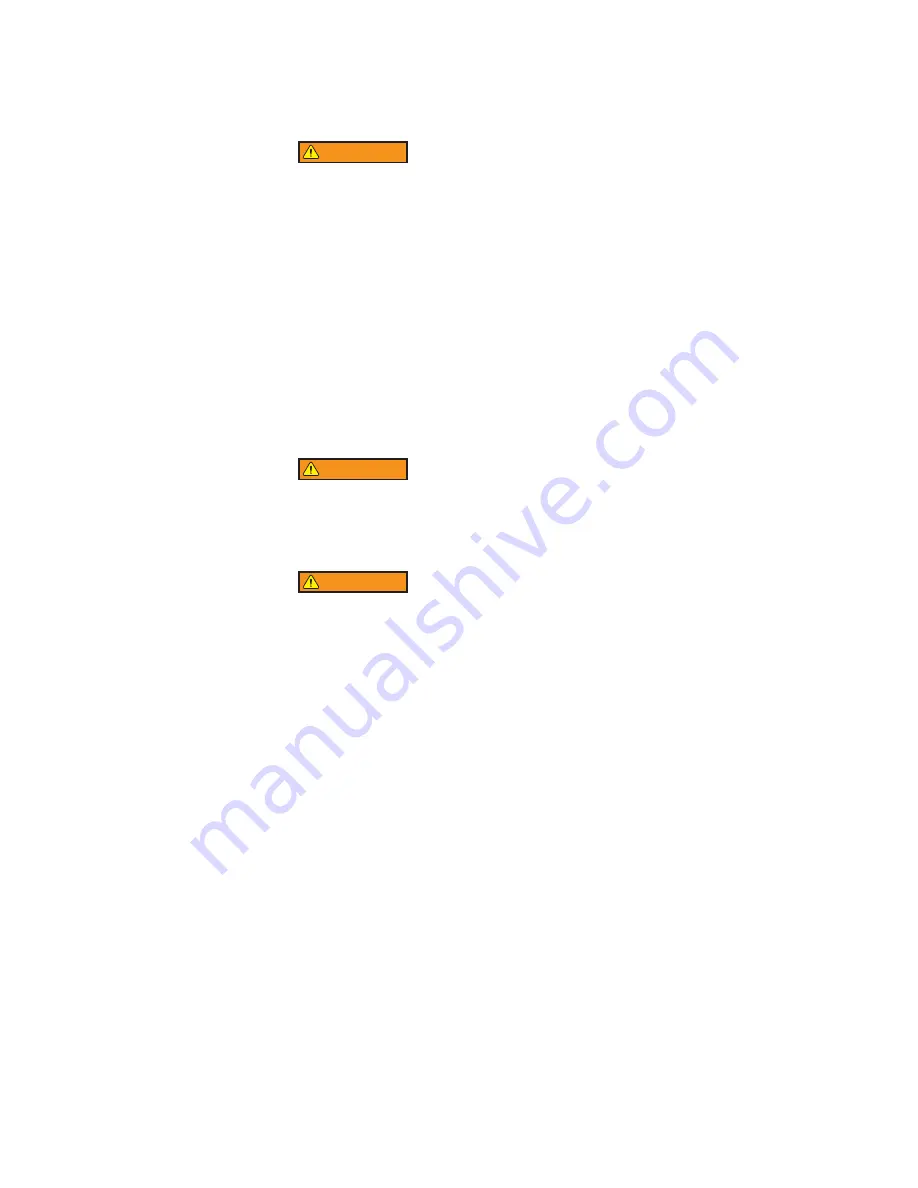
GENERAL RULE
S
700+smgr.fm
PAGE 39
S
AF
ETY M
AN
U
AL
8.19
Air can be introduced into the delivery system in several ways
besides being sucked in through the hopper:
• when initially priming the delivery system;
• when restarting after moving;
• when restarting after adding or removing delivery system;
• when attempting to remove a blockage by “rocking” the concrete;
• When opening the system to remove blockages;
• when pumping is stopped and the boom is at a downward angle.
Whenever air has been introduced into the line for any reason, warn everyone to
stay away from the discharge until material runs steadily. Personnel should move a
prudent and reasonable distance beyond the end-hose movement area or the point of
discharge, and personal protective equipment (PPE) should be worn (Figure 51).
8.20
A bulk density of approximately 150 pounds per cubic foot is
assumed for the material to be pumped with a placing boom (normal concrete). If
you intend to pump material with a higher bulk density, you must contact the
manufacturer for advice. Failure to do so may result in damage to the boom and/or
instability in certain operating positions.
8.21
Blockages in the pump or delivery pipeline can create an
unsafe condition.
Blockages are caused by many different factors, as outlined
below.
CAUSES OF
BLOCKAGES
•
Faulty concrete mix design.
The concrete being supplied may not be a pump-
able mix; for example there may be too much sand or too little cement. There
may be bleeding or segregation. Some admixtures adversely affect pumpability
(e.g., too much air entrainment). If the mix is not pumpable, no amount of oper-
ator expertise will make it so.
•
The line size may be inadequate.
The line size should always be at least 3
times larger than the largest aggregate being pumped, or blockages could occur.
•
Worn concrete valve parts.
Worn parts allow the finest material and water to
escape back into the hopper when pressure is applied.
•
Pipeline and joint deficiencies.
This would include: dirty pipes (pipes that have
not been cleaned properly); worn and leaking pipe joints that allow loss of con-
crete fines and water; pipes that haven’t been properly primed before starting;
and too many sections of rubber hose, which increases friction. These are all
causes of blockages that can be controlled by the operator.
•
Pump inadequate for the application.
The pump selected for the job may not
have enough pressure or horsepower available for the required duty.
•
Concrete setting up in the pipeline.
This may be caused by delays on site (e.g.,
repairing a broken form), or by attempting to pump “old” concrete (concrete that
was batched hours before pumping and is being kept alive only by adding water
and constant agitation). Weather conditions can also affect how quickly the con-
crete becomes hard. Companies should establish procedures for these situations.
A good rule of thumb is:
If in doubt...wash out.
WARNING
WARNING
WARNING
Содержание SPB 28
Страница 2: ......
Страница 4: ......
Страница 8: ...8 Table of Contents SPB Operation Manual...
Страница 10: ......
Страница 16: ...16 Introduction SPB Operation Manual...
Страница 18: ......
Страница 22: ...22 Specifications SPB Operation Manual SPB 35 Working Range Diagram SPB 35 235...
Страница 24: ...24 Specifications SPB Operation Manual Working Range Diagram SPB 37 SPB 37 235...
Страница 26: ......
Страница 28: ...28 Safety S 39 41 SX Operation Manual...
Страница 113: ...402indexcov eps ALPHABETICAL INDEX 700indxcov fm PAGE 83 SAFETY MANUAL Alphabetical Index...
Страница 122: ...30 Overview S 39 41 SX Operation Manual...
Страница 154: ...62 Operation SPB Operation Manual Lifting Instructions 1 of 3...
Страница 155: ...63 Operation SPB Operation Manual Lifting Instructions 2 of 3...
Страница 156: ...64 Operation SPB Operation Manual Lifting Instructions 3 of 3...
Страница 200: ......
Страница 216: ...124 Appendix SPB Operation Manual...