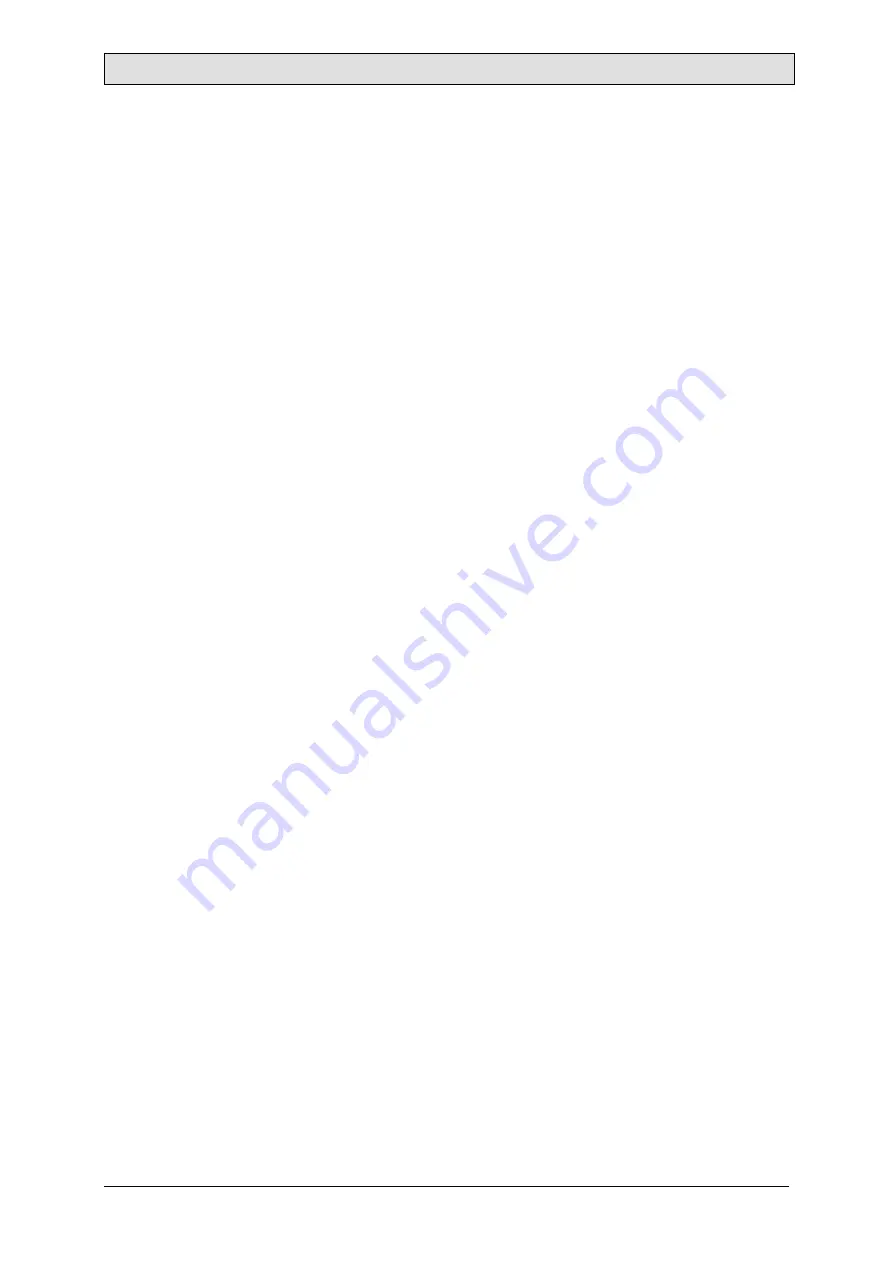
Safety instructions
©
by Antriebs- & Regeltechnik Schimpf GmbH
8
•
After completing the adjustments, check whether the electrical signals
of the actuating drives (especially the position feedback) correspond to
the mechanical position of the drive! This applies in particular to the
end positions!
•
After completing the installation or configuration work, check that the
actuating drive is functioning correctly. Check compliance with the end
positions if necessary! Also check that any optional components are
functioning properly!
•
Finally, check that any safety devices are functioning properly to
ensure that they are free of errors!
Содержание 00-10/30 STEP
Страница 28: ...Connections by Antriebs Regeltechnik Schimpf GmbH 28 Figure 10 CPU board 00 15 Figure 11 Add on board 00 15 ...
Страница 69: ...Declaration of Conformity by Antriebs Regeltechnik Schimpf GmbH 69 Declaration of Conformity ...
Страница 71: ...Dimensional drawing by Antriebs Regeltechnik Schimpf GmbH 71 Figure 15 Dimensions of drive type 00 15 ...
Страница 72: ...Dimensional drawing by Antriebs Regeltechnik Schimpf GmbH 72 Figure 16 Dimensions of drive type 01 15 ...