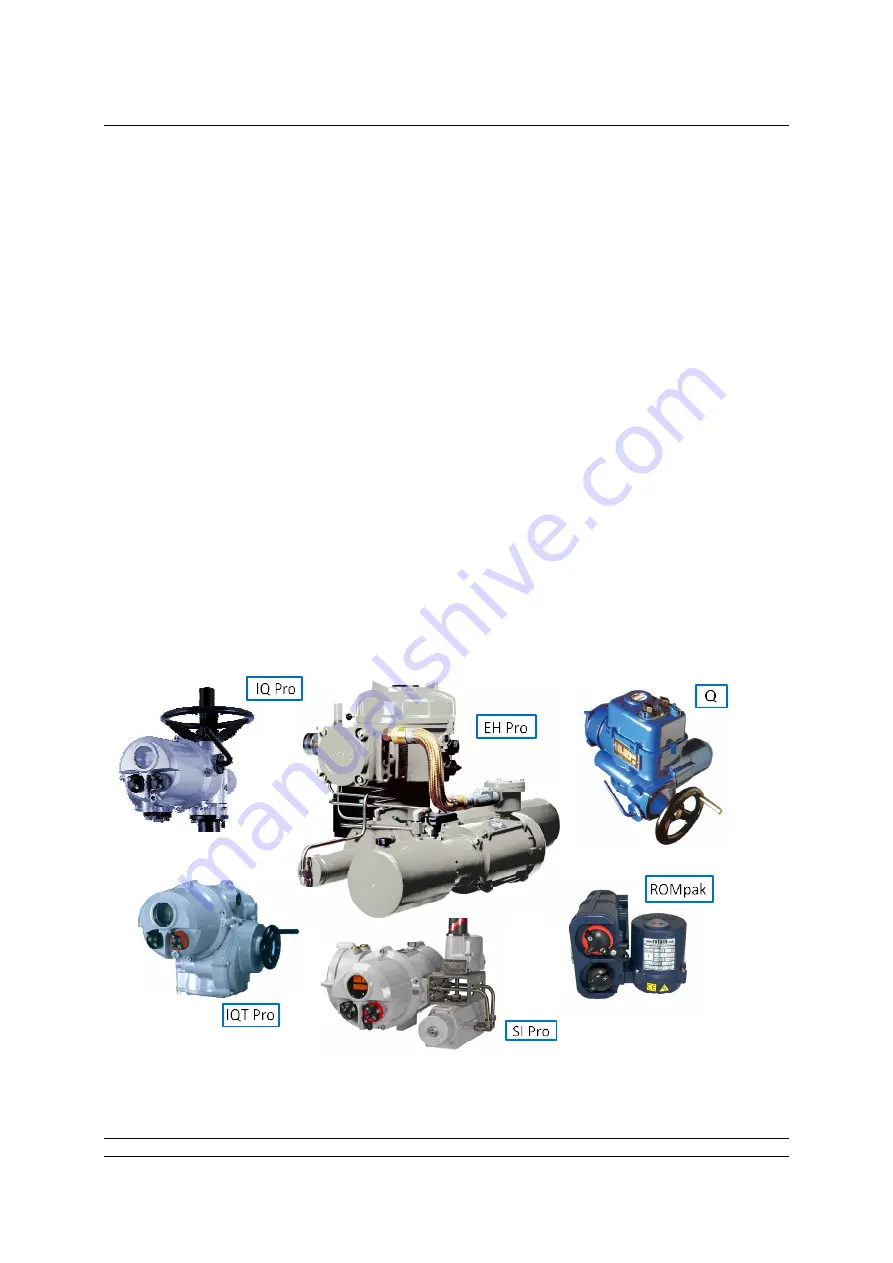
Introduction
Publication PUB091-003-00_0119
7 of 76
1 INTRODUCTION
The Rotork Modbus Module Actuator Control option card (MFU) uses 2-wire (half-duplex) RS-485 and
the Modbus RTU protocol to allow for information exchange and control over the data highway
between the actuator and a suitable host system with a Modbus capability.
The module is an integral part of the actuator in which it is housed and is fitted within the main
electrical housing. For the IQ
Pro
, IQT
Pro
, SI Pro, EH Pro and Q products this electrical housing is
double sealed and need never be opened once the actuator leaves the assembly plant. The ROMpak
actuators do not have double sealing and the electrical cover is required to be entered for connecting
to the Field connections.
All adjustments to the settings for the module may be made via the Modbus data highway using a
Modbus master tool or via the Infra-red setting tools for the IQ
Pro
, IQT
Pro
, SI Pro and EH Pro
products. (If the data highway speed was not specified at time of order, or it is changed, it may be
necessary to change the links on a Single Highway plus Repeater option, see Section 4.5.3.)
The Modbus Module circuits do not impinge on the actuator control electronics; the actuator itself
remains fully self-protecting. The module performs the tasks of network interface, actuator data
collection and the issuing of actuator commands.
The Modbus Module may command the actuator into which it is fitted to open, stop, close, perform an
ESD operation or move to a set position. Commands to the module come from the network and will
have been generated in a master controller. The module operates in Master/Slave communication
mode only using Modbus RTU protocol. For SI and EH actuators, where a SIL approved safety
function is required, the hard wired ESD control should be used and not the Modbus ESD function.
Fig 1: The Modbus Module Option Card Actuator Compatibility