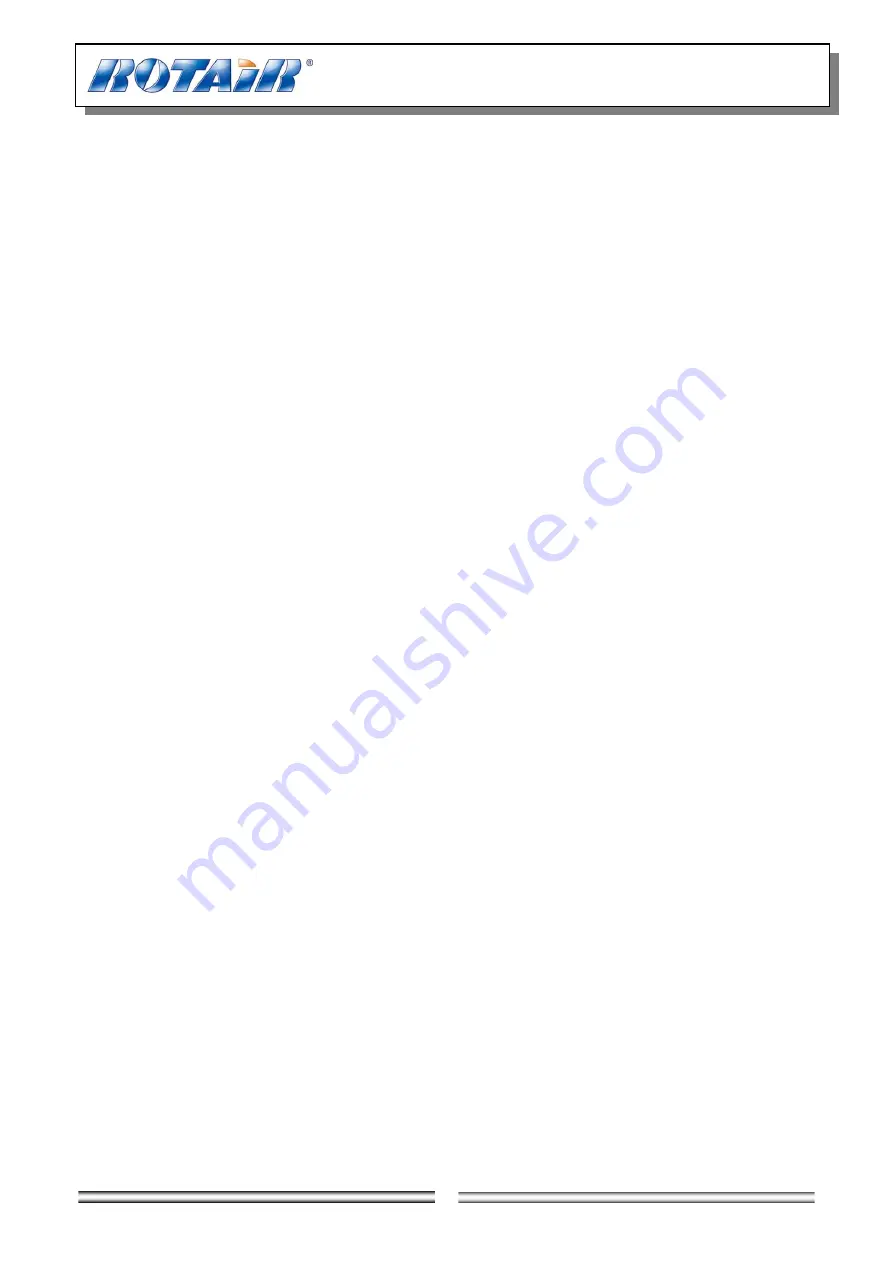
11
6.2 Machine State Diagram
Controller operational logic is shown in the machine state diagram as state blocks with an associating status
block number. The state block determines the functionality of the controller at any given time. The controller
can only be in one state at any given time. The controller will move from state to state in accordance with the
defined exit and entry conditions of each state block and the defined connections between state blocks.
Definitions:
Fault:
A detected abnormal condition that must be indicated to operator personnel and that may require controller
automated safety action, dependant on fault type and definition.
Start Inhibit Fault (S):
A start inhibit fault is a condition that may present a danger or cause damage to the compressor if started
whilst the condition is present. Start inhibit faults are only triggered if a compressor start from the ready to
start condition is attempted. Start inhibit faults are not triggered during an automated motor start sequence
from the standby condition. Start inhibit faults are self-resetting. A start inhibit fault code is displayed when
triggered but is not recorded in the fault log.
Run Inhibit Fault (R):
A run inhibit fault is a condition that may present a danger or cause damage to the compressor if the main
motor is started whilst the condition is present. Run inhibit faults are only triggered if a motor start sequence
is initiated. Run inhibit faults are self-resetting and do not prevent the compressor from entering a started
condition. A Run inhibit will hold the compressor in a standby state and will allow a motor start sequence
when the condition is no longer present. A Run inhibit fault code is displayed when triggered but is not
recorded in the fault log.
Alarm Fault (A):
An alarm fault is a warning condition that does not present an immediate danger or potential damage to the
compressor. An alarm state will not shutdown the compressor or affect normal operation. An alarm fault code
is displayed that must be manually reset to clear once the condition has been resolved or no longer exists.
Shutdown Fault (E):
A shutdown fault is a condition that may present danger or potential damage to the compressor if the
condition persists. A shutdown fault will cause the controller to stop the compressor. A shutdown fault code
is displayed that must be manually reset to clear once the condition has been resolved or no longer exists.
Two types of shutdown fault are definable a) non-emergency shutdown, an immediate controlled stop is
executed, b) emergency shutdown, an instantaneous stop is executed.
Unload Pressure:
The unload pressure is the delivery pressure level (adjustable) at which the controller will de-energise the
load solenoid output and the compressor will offload.
Load Pressure
:
The load pressure is the delivery pressure level (adjustable) at which the compressor will energise the load
solenoid output and the compressor will load. If in the standby state, an automated main motor start
sequence is triggered prior to load.
Main Motor Start Sequence:
The controller will energise the Star contactor output followed by the Main contactor output 200ms later. After
the Star/Delta timer (adjustable) expires the controller will execute an automated Star to Delta contactor
output changeover with a 50ms star to delta transition time. If a Stop command is received during the start
sequence the controller will continue to execute the start sequence before stopping. This action is intended
to limit the break current of motor starter contactors.