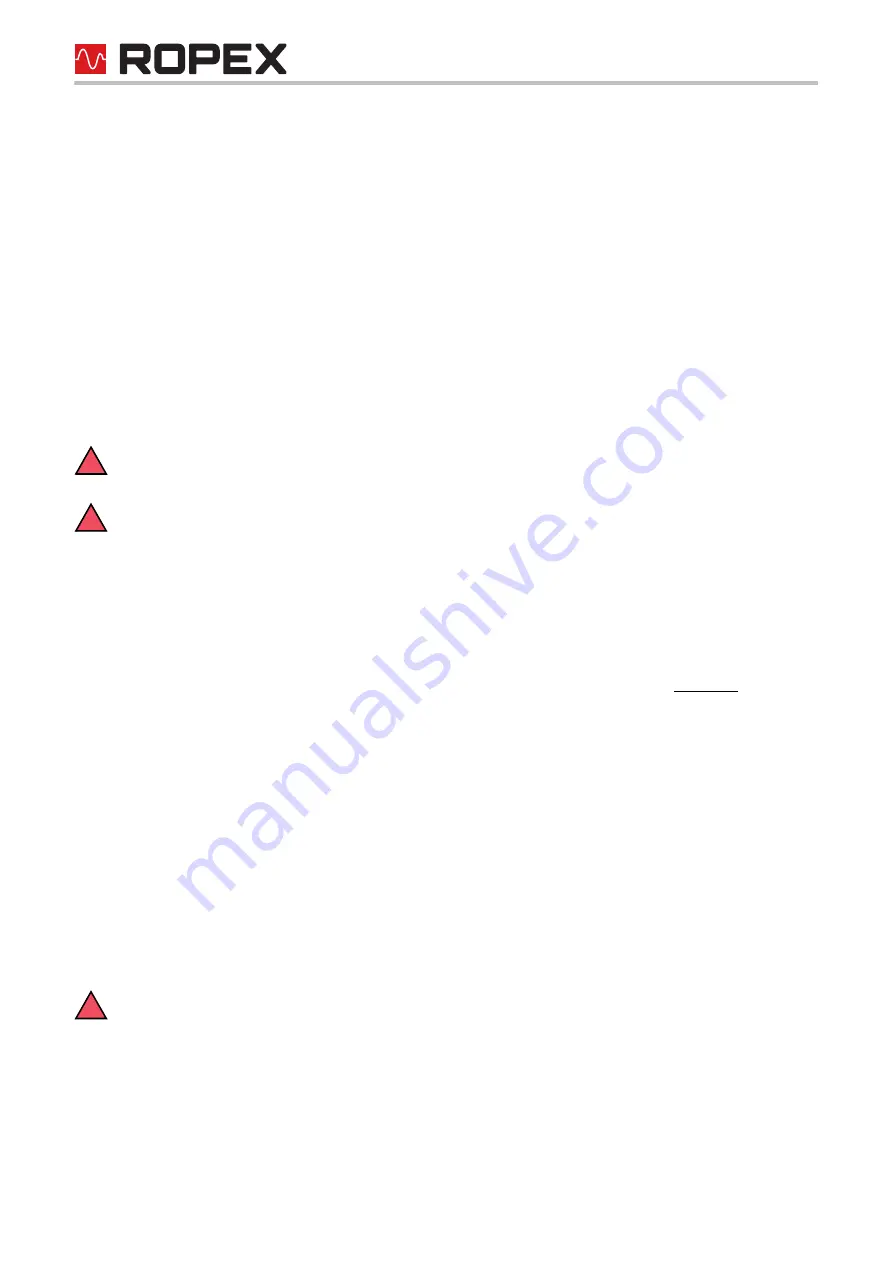
Controller functions
Page 52
RES-409
Version 1
If an error occurs, the fault bit is set in the controller status (bit 4) (
section 10.4.1 "Controller status" on page 39)
and in the acknowledgment message (bit 14) (
section 10.4.2 "Acknowledgment message" on page 40). The
error message appears at bit positions 8…11 in the controller status.
D.)
Error code output by means of the 0 to 10V actual value output (terminals 17+18):
Since the temperature no longer needs to be indicated if the controller is faulty, the actual value output is used to
display error codes in the event of a fault.
13 voltage levels (up to January 2007: 12 voltage levels) are provided for this purpose in the 0…10VDC range,
each of which is assigned an error code (
section 10.16 "Error messages" on page 52).
If a state that requires "AUTOCAL" occurs – or if the controller configuration is incorrect – (error codes 8…12; as
of February 2007 also: 104…106, 111…114, 211, 302, 303), the actual value output jumps back and forth at 1Hz
between the voltage value corresponding to this error and the end of the scale (10VDC, i.e. 300°C or 500°C). If
a "START" command is sent in one of these states (or a "START" signal is activated), the voltage value no longer
changes.
An error message can only be reset by sending a "RESET" command or by switching the controller
off and then on again.
Invalid error messages may appear when the controller is switched off owing to the undefined
operating state. This must be taken into account when they are evaluated by the higher-level
controller (e.g. a PLC) in order to avoid false alarms.
10.16 Error messages
A detailed fault diagnosis can be carried out using the CAN protocol. A two-digit error code (4-bit) can be queried
for this purpose via CAN message address 4, value 4 (
section 10.4.1 "Controller status" on page 39). All
controllers manufactured as of February 2007 support three-digit error codes (10-bit) as an additional option. This
can be queried with CAN message address 4, value 13 (ƒ section 10.4.3 "Fault / AUTOCAL status (as of February
2007)" on page 41).
The error codes provide information about the exact cause of the fault. A voltage corresponding to the error code
is additionally generated at the actual value output.
The table below shows how the analog voltage values at the actual value output are assigned to the faults that
have occurred. It also describes each fault and the required corrective action.
The error messages are listed in two separate tables for controllers "up to January 2007" and "as of February
2007". The block diagram in section 10.17 "Fault areas and causes" on page 57 permits each fault to be cleared
quickly and efficiently.
13 voltage levels for fault diagnostics appear at the actual value output of all controllers manufactured as of
February 2007. The error messages are differentiated even more finely internally. The error codes described
below can also be displayed via the CAN interface (CAN message address 4, value 13) or in the ROPEX
visualization software (
section 10.12 "Diagnostic interface / visualization software (as of February 2007)" on
page 50 to facilitate troubleshooting).
If the actual value output is evaluated in order to identify an error message – in the higher-level
controller, for instance – the tolerance window must be adjusted to prevent it from being incorrectly
interpreted. Please note the tolerances of the actual value output (
page 11).
!
!
!