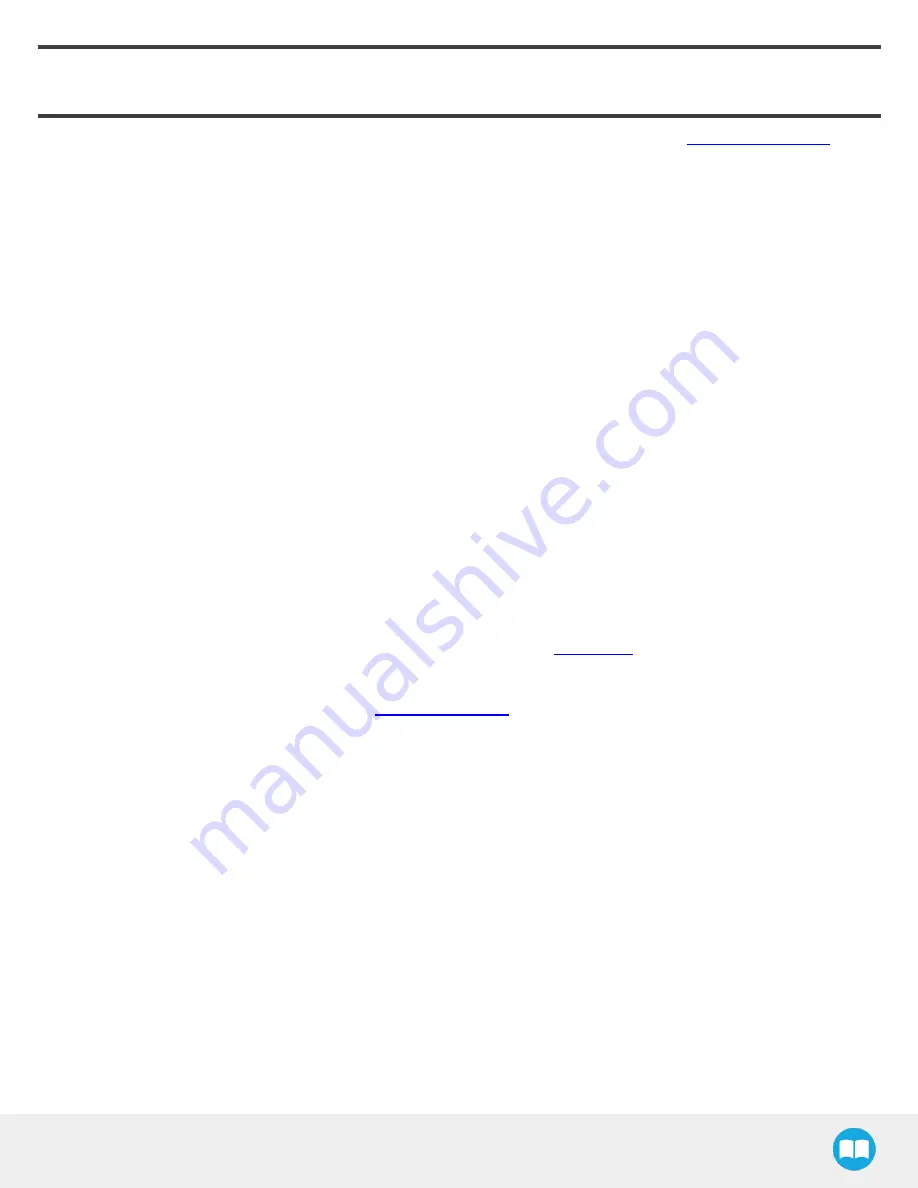
8. Troubleshooting
The following are some common troubleshooting hints, if you need further assistance please contact
.
8.1. General troubleshooting
8.1.1. An offset has appeared in the Sensor data
l
Changes in ambient conditions can cause an offset in the sensor signals.
l
An offset can also be caused if the sealing o-rings are displaced during an overload.
l
These offsets do not account for a de-calibration of the Sensor as they are in fact recognized as effort applied to the Sensor. Any
additional force applied on the tool side of the Sensor will be read normally.
l
In all cases, it is recommended to have a software offset which compensates for these variations in addition to the effort caused
by the tool weight for a given orientation. It is preferable to set the software offset before starting to use the sensor data such
that the robot software uses a proper and consistent reference.
8.1.2. Procedure to determine if the Sensor is functional
l
Verify that the Sensor is connected according to the Installation section of this manual.
l
When powered, verify that the LED on the Sensor is blue (not red/blue).FT 300 LED is red if powered without communication,
blue if powered with communication. For detailed information on the LED status, refer to the Status LED section.
l
Power-off the Sensor and then connect the provided USB/RS485 converter to a USB port of a Windows PC.
l
In the Windows PC, open the Device Manager.
l
You should see a USB Serial Port device in the Ports (COM & LPT) category. If not, it is possible that the converter drivers
have not installed automatically. You can download the drivers from the
ftdichip.com
website.
l
Power the Sensor with the recommended voltage.
l
Download the simple data logger application at
support.robotiq.com
l
Run the data logger application. Enter 100 for the number of data per 10 seconds and any file name (for example "test.csv").
l
Verify that the sensor data is displayed in the Windows console application.
FT 300 Force Torque Sensor - Instruction Manual
80