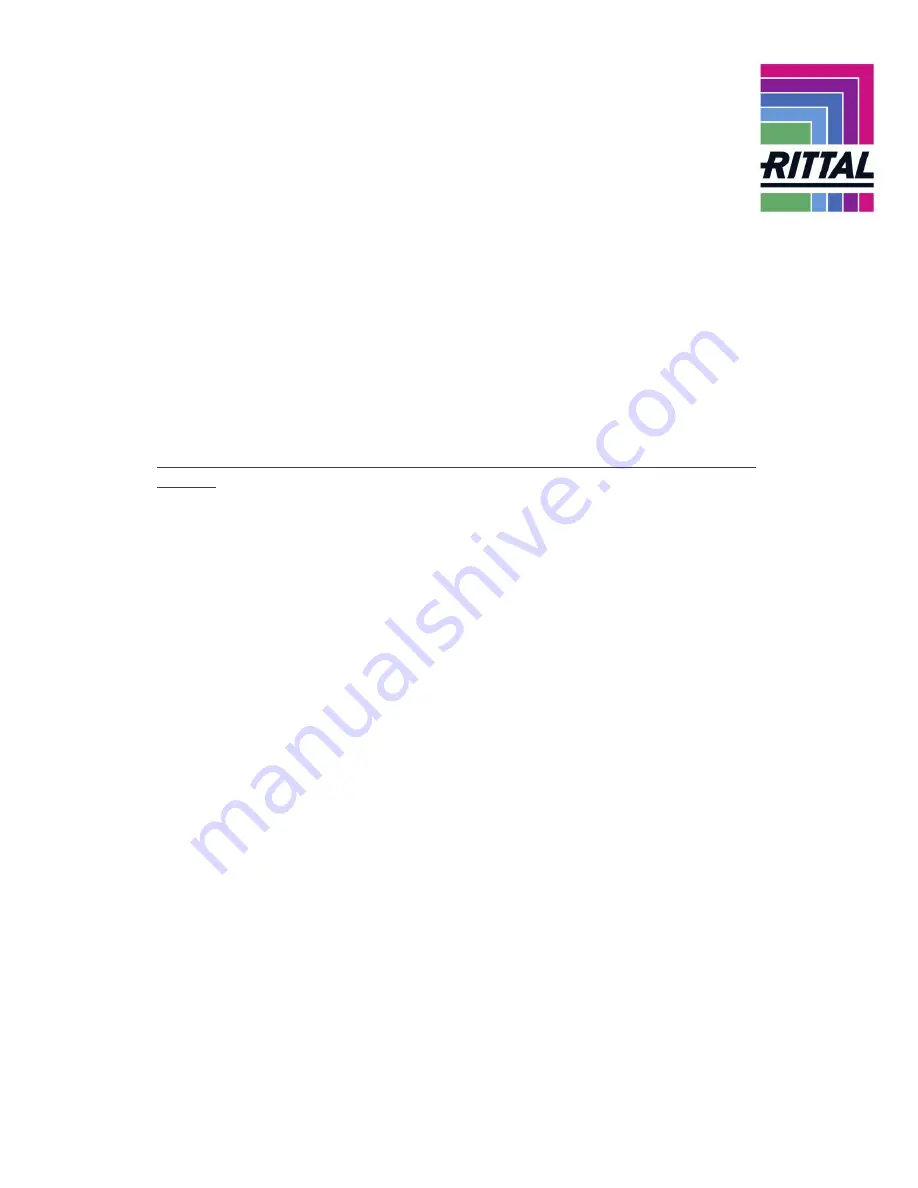
63
7.
Loosen and remove the motor power and encoder cables.
8.
Place the motor on a workbench to remove the gearbox.
9.
Use the images in Section 3.19.1 to locate and remove the gearbox coupling access
plug, motor to gearbox mount bolts and to loosen the gearbox coupling.
a.
The gearbox coupling will need to be aligned with the plug access, rotate the
pinion gear until the coupling mount bolts are visible.
b.
Loosen the gearbox coupling and separate the motor from the gearbox.
10.
Refer to Section 3.19.3 for Pinion Removal.
Note: It is advisable to replace the pinion gear (if showing wear) while the motor is out of the
machine.
3.18.2
Replacement
To install the new X-axis motor, follow the previous steps in reverse order but insure of the
following items;
Be sure that the pinion gear mount screw is tight.
Be sure that the gearbox coupling is tight.
Firmly secure the pinion to rack by using the grub screw mounts. Tighten until
snug but do not exert an excessive amount of torque on the grub screws. Tighten
locking nuts when completed.
Contact Rittal RAS Technical Support to remotely connect to the Perforex
machine using remote desktop software. Technical support will test the motor
and preform the initial Master Reference of the motor encoder, Section 3.20.
Once the Master Reference has been accomplished the axis will need to be
calibrated and the Base offset established. Do not attempt to pick up a tool until
the calibration has been performed, the spindle will collide with the tool
magazine. Refer to Section 3.21 - Calibrating the Base Offset procedure.
Содержание BC 1007 HS
Страница 54: ...54 ...
Страница 55: ...55 ...
Страница 59: ...59 Figure 2 Tool in Spindle Clamped Feedback ...
Страница 60: ...60 Figure 3 Tool in Spindle Ejected Feedback ...
Страница 78: ...78 o Select the Calculate Base Offset button in the lower portion of the popup screen ...
Страница 81: ...81 ...
Страница 87: ...87 ...
Страница 88: ...88 ...
Страница 89: ...89 ...
Страница 90: ...90 ...
Страница 91: ...91 ...
Страница 92: ...92 ...