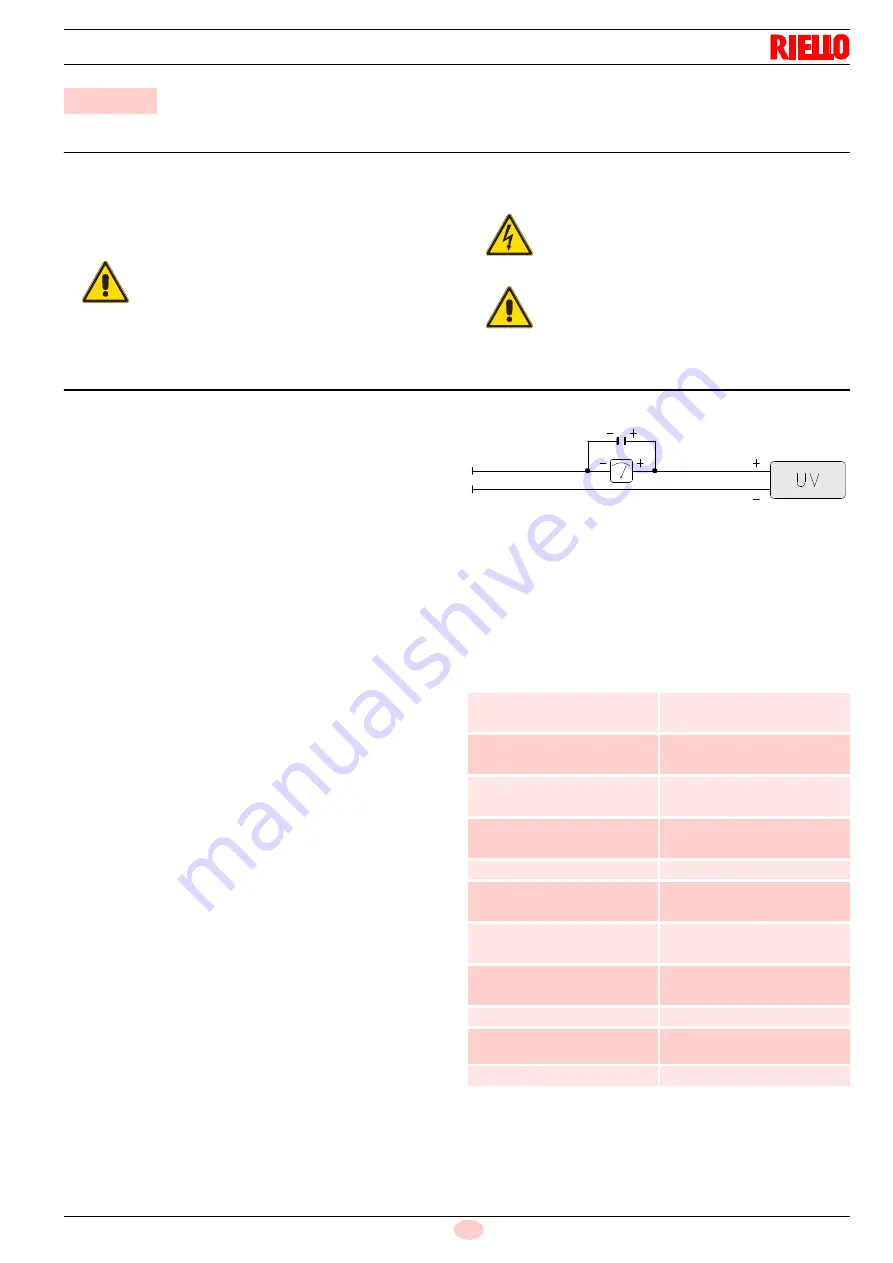
59
20081825
GB
Maintenance
7.1
Notes on safety for the maintenance
The periodic maintenance is essential for the good operation,
safety, yield and duration of the burner.
It allows you to reduce consumption and polluting emissions and
to keep the product in a reliable state over time.
Before carrying out any maintenance, cleaning or checking oper-
ations:
7.2
Maintenance programme
7.2.1
Maintenance frequency
The gas combustion system should be checked at least once a
year by a representative of the manufacturer or another
specialised technician.
7.2.2
Checking and cleaning
Combustion
The optimum calibration of the burner requires an analysis of the
flue gases.
Significant differences with respect to the previous measure-
ments indicate the points where most care should be exercised
during maintenance.
Combustion head
Open the burner and make sure that all components of the
combustion head are in good condition, not deformed by the
high temperatures, free of impurities from the surroundings
and correctly positioned.
Burner
Clean the outside of the burner.
Clean and grease the adjustable profile of the cams.
Fan
Check to make sure that no dust has accumulated inside the fan
or on its blades, as this condition will cause a reduction in the air
flow rate and provoke polluting combustion.
Boiler
Clean the boiler as indicated in its accompanying instructions in order
to maintain all the original combustion characteristics intact, especial-
ly the flue gas temperature and combustion chamber pressure.
Electrical current to UV cell
(Fig. 46 on page 59)
Clean the glass cover from any dust that may have accumulated.
To remove the photocell, pull out outwards; it is only pressed in.
Min value for a good work: 70 µA.
If the value is lower, it could be due to:
–
exhausted photocell
–
low voltage (lower than 187 V)
–
bad regulation of the burner
In order to measure the current, use a microammeter of 100 µA
d.c., connected in series to the photocell, as in the scheme, with
a capacitor of 100 µF - 1V d.c. at the same level of the instrument.
7.2.3
Safety components
The safety components should be replaced at the end of their life
cycle indicated in the following table.
The specified life cycles do not refer to the warranty terms indi-
cated in the delivery or payment conditions.
Tab. V
7
Maintenance
DANGER
The maintenance interventions and the calibration
of the burner must only be carried out by qualified,
authorised personnel, in accordance with the con-
tents of this manual and in compliance with the
standards and regulations of current laws.
DANGER
Turn off the burner's power supply using the main
system switch.
DANGER
Turn off the fuel interception tap.
Safety
component
Life cycle
Flame control
10 years or 250,000
operation cycles
Flame sensor
10 years or 250,000
operation cycles
Gas valves (solenoid)
10 years or 250,000
operation cycles
Pressure switches
10 years or 250,000
operation cycles
Pressure adjuster
15 years
Servomotor (electronic cam)
10 years or 250,000
operation cycles
Oil valve (solenoid)
10 years or 250,000
operation cycles
Oil regulator
10 years or 250,000
operation cycles
Pipes/ oil fittings (metallic)
10 years
Flexible hoses (if present)
5 years or 30,000
pressurised cycles
Fan impeller
10 years or 500,000 start-ups
Fig. 46
D1143
Содержание RLS 310/E MX
Страница 2: ...Original instructions ...
Страница 81: ...79 20081825 GB Appendix Electrical panel layout RLS 310 410 E MX 230 400V Direct Start Up ...
Страница 82: ...20081825 80 GB Appendix Electrical panel layout RLS 310 410 510 610 E MX 400V Star Triangle Start Up ...
Страница 84: ...20081825 82 GB Appendix Electrical panel layout ALL MODELS ...
Страница 85: ...83 20081825 GB Appendix Electrical panel layout 0 ALL MODELS ...
Страница 87: ...85 20081825 GB Appendix Electrical panel layout ALL MODELS ...
Страница 94: ......
Страница 95: ......