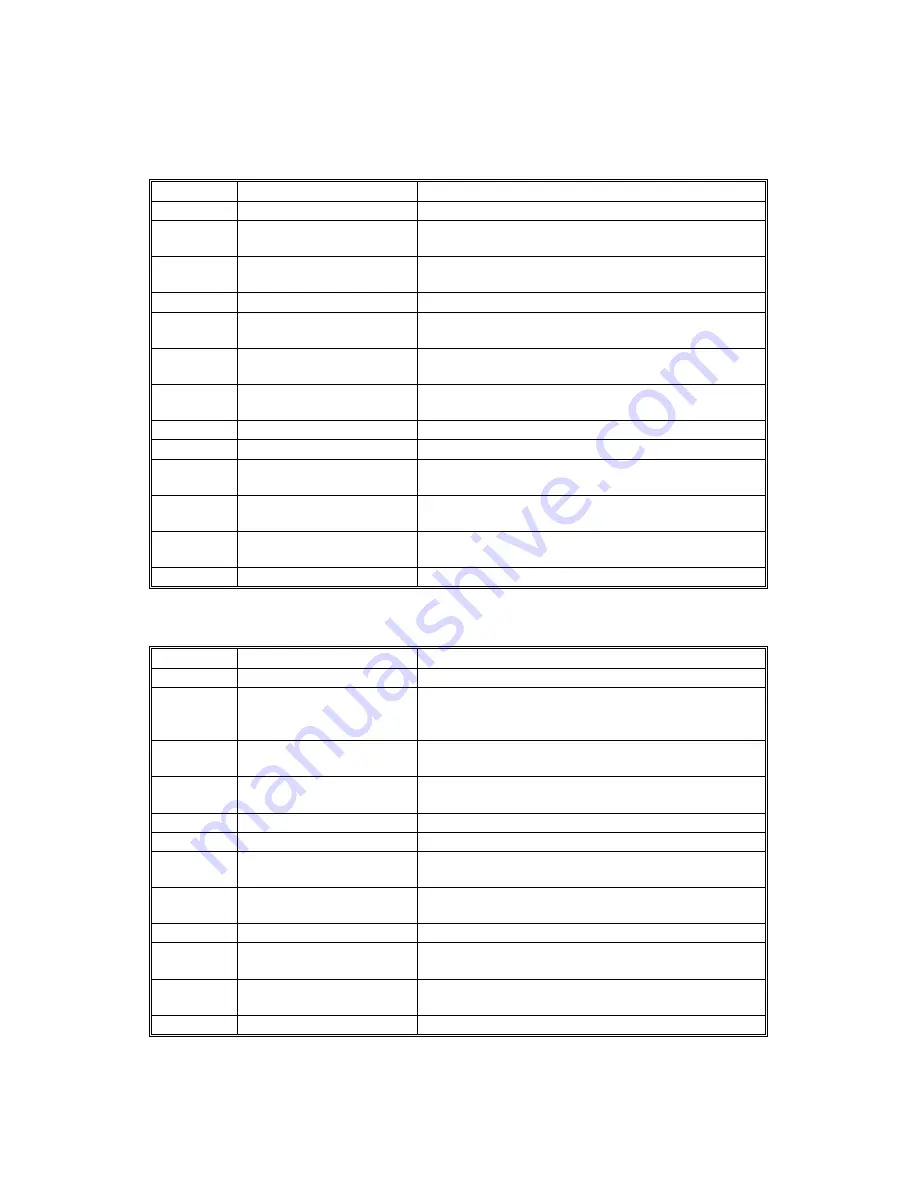
MECHANISM OVERVIEW
C262/C265 6-6
SM
6.1.3 TABLE OF ELECTRICAL COMPONENTS
Boards
Index No.
Name
Function
1
Operation Panel Board
Controls the operation panel.
2
Main Motor Control
Board
Controls the main motor speed.
3
Power Supply Unit
(PSU)
Provides DC power to the machine.
4
I/O Board
Controls the mechanical components.
5
Double Feed Detection
Board
Detects double feeds
6
Application Control Unit
(ACU)
This is the main control board for the machine.
7
Engine Control Unit
(ECU)
Controls the engine functions, both directly and
through other boards.
12
Lamp Stabilizer
This supplies power to the exposure lamp.
14
CCD and SBU
Makes a video signal from the scanned original.
20
Feed Pressure Detection
Board
Sends data about the paper feed pressure to the
CPU.
31
Paper Width Detection
Board
Sends data about the paper width on the paper
table to the CPU.
34
Separation Pressure
Detection Board
Sends data about the paper separation pressure to
the CPU.
59
Ink Detection Board
Checks if there is ink in the drum.
Motors
Index No.
Name
Function
15
Scanner Drive Motor
Drives the scanner.
17
Registration Pressure
Motor
Releases the pressure between the registration
rollers, to allow jammed paper to be removed
easily.
21
Feed Pressure Motor
Drives the paper feed pressure adjustment
mechanism.
24 Registration
Motor
Feeds the paper to align it with the image on the
master on the drum.
26
Paper Feed Motor
Feeds the paper from the paper table.
30 Paper
Table
Motor Raises
and lowers the paper table.
35
Separation Pressure
Motor
Drives the paper separation pressure adjustment
mechanism.
39
Friction Pad Shift Motor
Switches between the normal pad and custom pad
(these pads are used for paper separation).
48
Ink Pump Motor
Drives the ink pump to supply ink.
50
Idling Roller Motor
Presses or releases the idling roller against the
drum metal screen.
52
Drum Shift Motor
Slides the drum metal screen position to the front
or rear for the side-to-side image shifting mode.
60
Master Eject Motor
Sends used masters into the master eject box.
Содержание LDD250
Страница 1: ...LDD280 C262 LDD250 C265 SERVICE MANUAL 002648MIU rev 05 31 06...
Страница 2: ......
Страница 3: ...C262 C265 SERVICE MANUAL...
Страница 4: ......
Страница 5: ...C262 C265 SERVICE MANUAL 002648MIU...
Страница 6: ......
Страница 8: ......
Страница 10: ......
Страница 12: ......
Страница 24: ......
Страница 28: ...SPECIFICATIONS...
Страница 29: ......
Страница 34: ...INSTALLATION...
Страница 35: ......
Страница 43: ...INSTALLATION PROCEDURE C262 C265 1 8 SM C262I044 WMFF C262I046 WMFF...
Страница 70: ...PREVENTIVE MAINTENANCE...
Страница 71: ......
Страница 74: ...REPLACEMENT AND ADJUSTMENT...
Страница 75: ......
Страница 84: ...SCANNER UNIT SM 3 9 C262 C265 Replacement Adjustment C Scanner drive motor x 1 x 2 1 spring C262R008 WMF C...
Страница 154: ...PAPER FEED SECTION SM 3 79 C262 C265 Replacement Adjustment E Paper feed assembly x 4 x 3 C262R087 WMF E...
Страница 233: ...TROUBLESHOOTING...
Страница 234: ......
Страница 259: ...SERVICE TABLES...
Страница 260: ......
Страница 321: ...DETAILED SECTION DESCRIPTIONS...
Страница 322: ......
Страница 394: ...DRUM C262 C265 6 72 SM 6 7 5 DRUM DRIVE MECHANISM C262D063 WMF C262D065 WMF C262D066 WMF A B C D E...