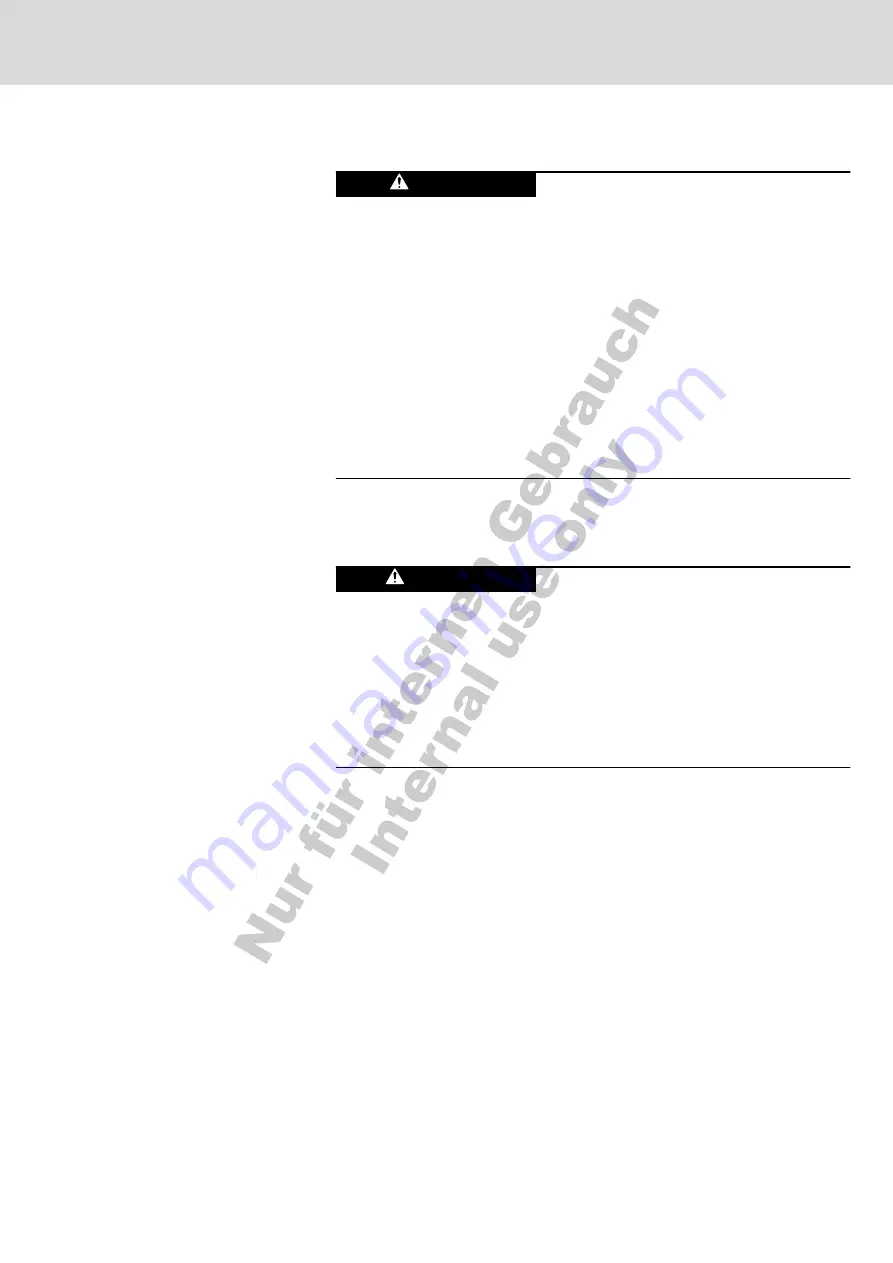
With electrical drive and filter components, observe the following:
High housing voltage and large leakage cur‐
rent!
Risk of death or bodily injury by electric
shock!
DANGER
●
Before switching on, the housings of all electrical equipment and motors
must be connected or grounded with the equipment grounding conduc‐
tor to the grounding points. This is also applicable before short tests.
●
The equipment grounding conductor of the electrical equipment and the
units must be non-detachably and permanently connected to the power
supply unit at all times. The leakage current is greater than 3.5 mA.
●
Over the total length, use copper wire of a cross section of a minimum
of 10 mm
2
for this equipment grounding connection!
●
Before start-up, also in trial runs, always attach the equipment ground‐
ing conductor or connect with the ground wire. Otherwise, high voltages
may occur at the housing causing electric shock.
2.4
Protection Against Electric Shock by Protective Low Voltage
(PELV)
High electric voltage by incorrect connection!
Risk of death or bodily injury by electric
shock!
WARNING
●
To all connections and terminals with voltages between 0 and 50 Volt,
only devices, electrical components, and conductors may be connected
which are equipped with a PELV (Protective Extra-Low Voltage) system.
●
Connect only voltages and circuits which are safely isolated from dan‐
gerous voltages. Safe isolation is achieved for example by isolating
transformers, safe optocouplers or battery operation without mains con‐
nection.
2.5
Protection Against Dangerous Movements
Dangerous movements can be caused by faulty control of connected motors.
Some common examples are:
●
Improper or wrong wiring of cable connections;
●
Incorrect operation of the equipment components;
●
Wrong input of parameters before operation;
●
Malfunction of sensors, encoders and monitoring devices;
●
Defective components;
●
Software or firmware errors.
Dangerous movements can occur immediately after equipment is switched
on or even after an unspecified time of trouble-free operation.
The monitoring in the drive components will normally be sufficient to avoid
faulty operation in the connected drives. Regarding personal safety, especial‐
ly the danger of bodily harm and material damage, this alone cannot be relied
upon to ensure complete safety. Until the integrated monitoring functions be‐
come effective, it must be assumed in any case that faulty drive movements
DOK-RCON02-FV*********IB01-EN-P
Rexroth Frequency Converter Fv
Bosch Rexroth AG
23/219
Safety Instructions for Electric Drives and Controls
Содержание Fv Series
Страница 20: ...Bosch Rexroth AG DOK RCON02 FV IB01 EN P Rexroth Frequency Converter Fv 18 219...
Страница 30: ...Bosch Rexroth AG DOK RCON02 FV IB01 EN P Rexroth Frequency Converter Fv 28 219...
Страница 34: ...Bosch Rexroth AG DOK RCON02 FV IB01 EN P Rexroth Frequency Converter Fv 32 219...
Страница 52: ...Bosch Rexroth AG DOK RCON02 FV IB01 EN P Rexroth Frequency Converter Fv 50 219...
Страница 58: ...Bosch Rexroth AG DOK RCON02 FV IB01 EN P Rexroth Frequency Converter Fv 56 219...
Страница 144: ...Bosch Rexroth AG DOK RCON02 FV IB01 EN P Rexroth Frequency Converter Fv 142 219...
Страница 164: ...Bosch Rexroth AG DOK RCON02 FV IB01 EN P Rexroth Frequency Converter Fv 162 219...
Страница 180: ...Bosch Rexroth AG DOK RCON02 FV IB01 EN P Rexroth Frequency Converter Fv 178 219...
Страница 214: ...Bosch Rexroth AG DOK RCON02 FV IB01 EN P Rexroth Frequency Converter Fv 212 219...
Страница 216: ...Bosch Rexroth AG DOK RCON02 FV IB01 EN P Rexroth Frequency Converter Fv 214 219...
Страница 220: ...Bosch Rexroth AG DOK RCON02 FV IB01 EN P Rexroth Frequency Converter Fv 218 219...
Страница 221: ...Notes DOK RCON02 FV IB01 EN P Rexroth Frequency Converter Fv Bosch Rexroth AG 219 219...