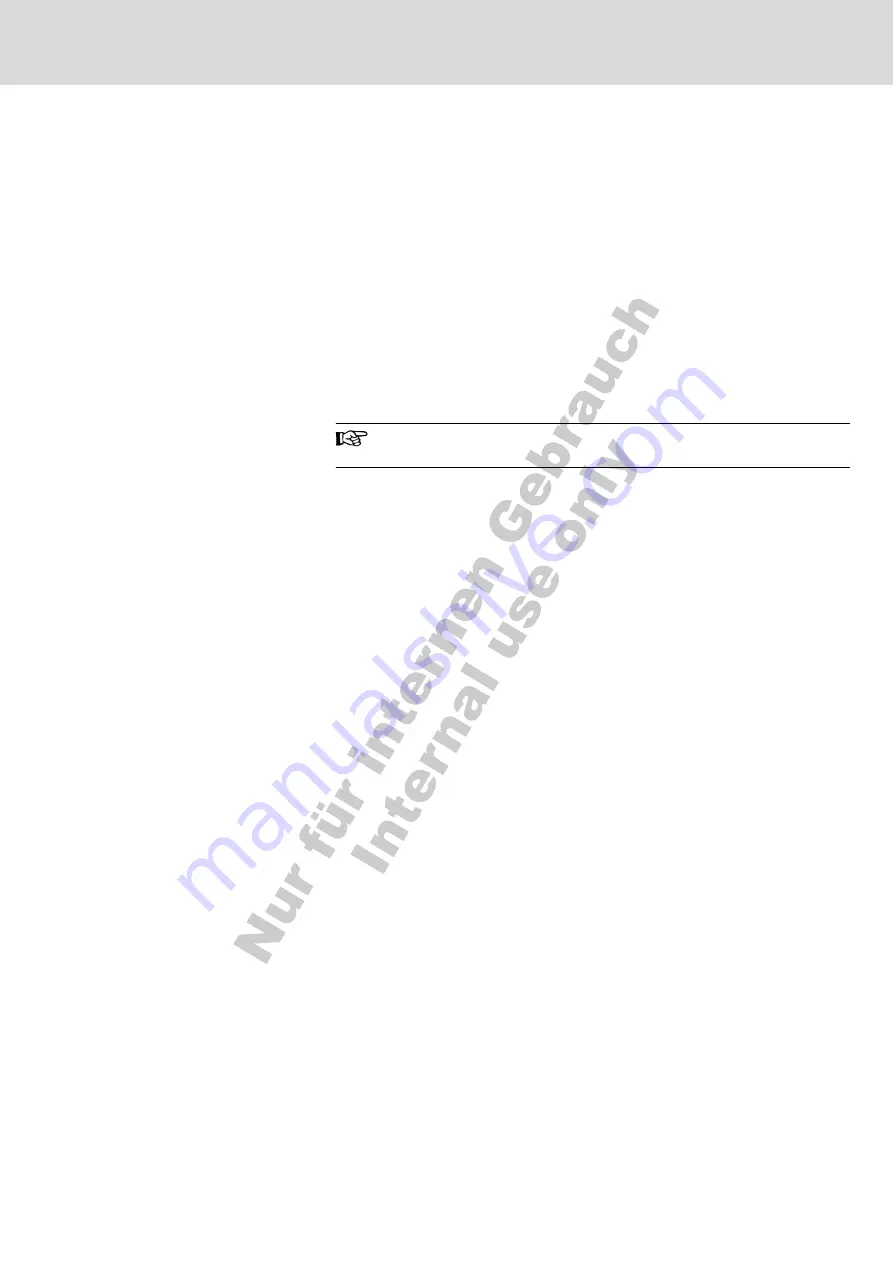
Installation of Motor Power Cable
●
Use shield motor power cable or run motor power cables in a shielded
duct;
●
Use the shortest possible motor power cable;
●
Ground shield of motor power cable at both ends over the largest possi‐
ble surface area to establish a good electrical connection;
●
Run motor lines in shielded form inside the control cabinet;
●
Do not use any steel-shielded lines;
●
The shield of the motor power cable must not be interrupted by mounted
components, such as output chokes, sine filter or motor filters.
EMC-optimal installation in facility and control cabinet
General information
For EMC-optimal installation, a special separation of the interference-free
area (mains connection) and the interference-susceptible area (drive compo‐
nents) is recommended, as shown in the figures below.
For EMC-optimal installation in the control cabinet, use a sepa‐
rate control cabinet panel for the drive components.
Division into areas (zones)
Exemplary arrangements in the control cabinet: See section Control Cabinet
Mounting According to Interference Areas – Exemplary Arrangements
We distinguish three areas:
1.
Interference-free area of control cabinet (area A):
This includes:
●
Supply feeder, input terminals, fuse, main switch, mains side of
mains filter for drives and corresponding connecting lines;
●
Control voltage or auxiliary voltage connection with power supply
unit, fuse and other parts unless connection is run via the mains fil‐
ter of the AC drives;
●
All components that are not electrically connected with the drive
system.
2.
Interference-susceptible area (area B):
●
Mains connections between drive system and mains filter for
drives, mains contactor;
●
Interface lines of drive controller
3.
Strongly interference-susceptible area (area C):
●
Motor power cables including single cores
Never run lines of one of these areas in parallel with lines of another area so
that there is not any unwanted interference injection from one area to the oth‐
er and that the filter is jumped with regard to high frequency. Use the shortest
possible connecting lines.
Recommendation for complex systems: Install drive components in one cabi‐
net and the control units in a second, separate cabinet.
Badly grounded control cabinet doors act as antennas. Therefore, connect
the control cabinet doors to the cabinet on top, in the middle and on the bot‐
tom via short equipment grounding conductors with a cross section of at least
6 mm
2
or, even better, via grounding straps with the same cross section.
Make sure connection points have good contract.
DOK-RCON02-FV*********IB01-EN-P
Rexroth Frequency Converter Fv
Bosch Rexroth AG
155/219
Technical Data
Содержание Fv Series
Страница 20: ...Bosch Rexroth AG DOK RCON02 FV IB01 EN P Rexroth Frequency Converter Fv 18 219...
Страница 30: ...Bosch Rexroth AG DOK RCON02 FV IB01 EN P Rexroth Frequency Converter Fv 28 219...
Страница 34: ...Bosch Rexroth AG DOK RCON02 FV IB01 EN P Rexroth Frequency Converter Fv 32 219...
Страница 52: ...Bosch Rexroth AG DOK RCON02 FV IB01 EN P Rexroth Frequency Converter Fv 50 219...
Страница 58: ...Bosch Rexroth AG DOK RCON02 FV IB01 EN P Rexroth Frequency Converter Fv 56 219...
Страница 144: ...Bosch Rexroth AG DOK RCON02 FV IB01 EN P Rexroth Frequency Converter Fv 142 219...
Страница 164: ...Bosch Rexroth AG DOK RCON02 FV IB01 EN P Rexroth Frequency Converter Fv 162 219...
Страница 180: ...Bosch Rexroth AG DOK RCON02 FV IB01 EN P Rexroth Frequency Converter Fv 178 219...
Страница 214: ...Bosch Rexroth AG DOK RCON02 FV IB01 EN P Rexroth Frequency Converter Fv 212 219...
Страница 216: ...Bosch Rexroth AG DOK RCON02 FV IB01 EN P Rexroth Frequency Converter Fv 214 219...
Страница 220: ...Bosch Rexroth AG DOK RCON02 FV IB01 EN P Rexroth Frequency Converter Fv 218 219...
Страница 221: ...Notes DOK RCON02 FV IB01 EN P Rexroth Frequency Converter Fv Bosch Rexroth AG 219 219...