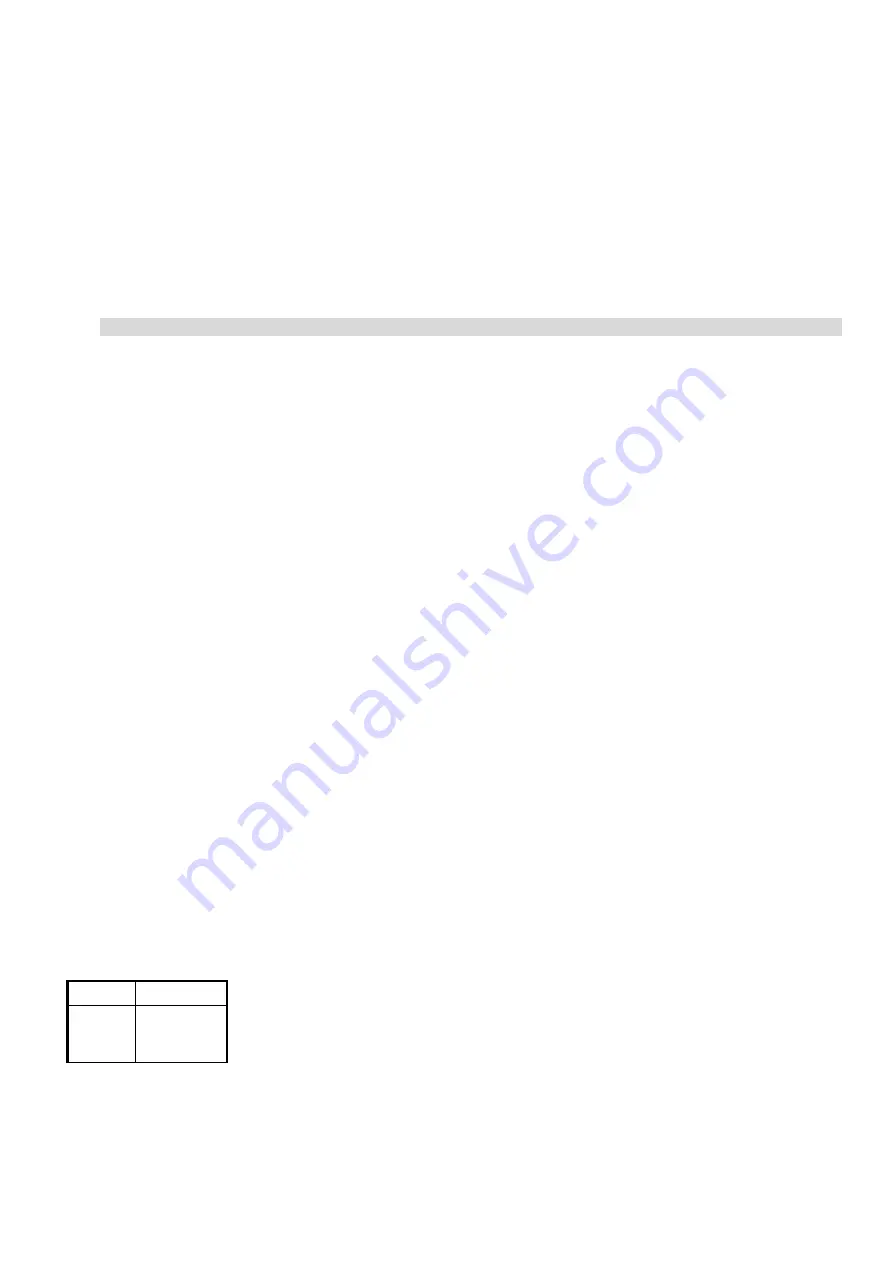
17/21
AUTOMATIC MECHANICAL DEVICES
As standard the unit is controlled by pressure switches:
1 LP pressure switch (automatic reset) for each compressor
1 HP pressure switch (automatic reset) for each condenser fan.
As option electronic controlled could by installed (refer to instruction manual joined to electrical diagram)
START-UP OPERATIONS
PRELIMINARY CHECKS AND OPERATIONS
General information
Ensure that all the threads are fully tightened on connection flanges, flexible connections and cables as jolting during transport
could cause screws and bolts to loosen.
Check also, for same reasons, if there are any breaks in the piping.
Ensure that the flexible connections are not in contact with metal parts. Vibrations from the compressor can cause wear in these
until they rupture at the point of friction.
Switch on crankcase heaters 24 hours before start-up.
Before starting up a machine with pressurised tanks, all service valves must first be opened upstream and downstream and all
external valves closed.
Leaks testing
Pressurise the whole system, including the compressors, using a neutral gas (Nitrogen) with a tracer at a minimum pressure of 10
bars and at a maximum
pressure below 17 bars, isolating the LP (low pressure) switches.
Important
: If the LP (low pressure) circuit is fitted with a safety valve (e.g.: on the suction accumulator) the test pressure on that
part of the circuit should be approx. 20% below the operating pressure of this valve.
Thorough leakage detection using haloid lamp or electronic detector should be carried out on the power pack.
After these tests, the gas must be removed. Fit the drier cartridges in their casing.
Dehydrationofcircuits
This operation must be carried out with all valves open (including solenoid valves) with connection to a vacuum pump:
of the low pressure side and of the high pressure side.
The quality of drying should not be judged by the speed at which the level of vacuum is reached but on the effective time it
is held (24 hours at 0.7 mbar is a good standard).
The total increase in pressure during that period should not be more than 2.6 mbar. The residual moisture in the system should be
less than 20ppm.
When the installation is under vacuum, an insulation check of the motor should not be carried out nor should the compressors be
started before at least 1 bar of fluid pressure is reintroduced.
This is to prevent motor windings damage.
Oil Level Check
Oil levels should never exceed the Bitzer recommendations
☯
half way up the sight glass when running
Oils
The compressor manufacturer recommendations should be followed.
The use of colorants or UV tracers as leak detectors in the oil, is not allowed.
Fluide
BITZER
R404A
BSE 32
OR
Artic EAL 32
This table is not exhaustive, but summarises the principal oils used. If any other oil is to be used, we would advise contacting
PROFROID or the compressor manufacturers.
RefrigerantFluidCharge
It is possible to charge in liquid phase when the installation is under vacuum through the charging valve provided on the liquid
receiver (depending on models).