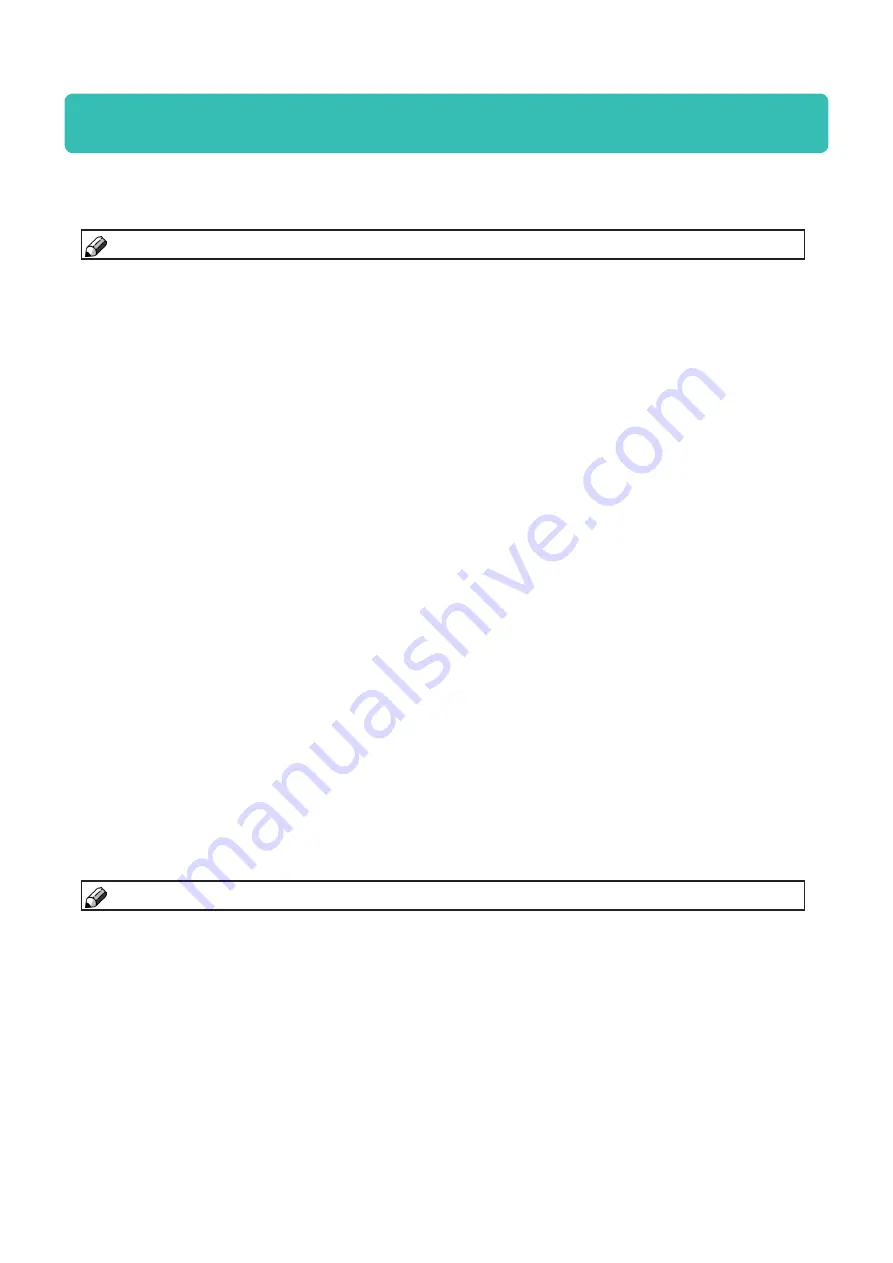
CIP Training
Plockmatic LCT3500 Large Capacity Tray
Troubleshooting - Fault codes
Fault Codes
LCT-564 Paper flow error Q325
Paper flow error Q325 is a paper flow error detection. Paper flow error checks sensor sta-
tus during running, both previous and following sensors in transport direction are checked
when paper leading/trailing edge is detected by a paper path sensor. Sensor Q201/Q202 and
Q326 are checked when paper leading edge comes to Q325. Q201/Q202 should be covered
and Q326 should be uncovered. Sensor Q201/Q202 and Q326 are also checked when paper
trailing edge comes to Q325. Q201/Q122 should be uncovered and Q326 should be covered.
A jam condition is generated if the described status is not detected.
Actions:
•
Ensure that DSD sensors Q501/502 are clean and calibrated properly (see sensor cali-
bration procedure in this section of the manual)
•
Ensure that sensor Q325/326 are clean (these sensors are located in the LCT, on the jam
clearance baffle on the lower part of the machine)
•
Check that there are no obstructions in the paper path
LCT-565 Paper flow error Q326
Paper flow error Q326 is a paper flow error detection. Paper flow error checks sensor sta-tus
during running, both previous and following sensors in transport direction are checked
when paper leading/trailing edge is detected by a paper path sensor. Sensor Q325 and Q327
are checked when paper leading edge comes to Q326. Q325 should be covered and Q327
should be uncovered. Sensor Q325 and Q327 are also checked when paper trailing edge
comes to Q326. Q325 should be uncovered and Q327 should be covered. A jam condition is
generated if the described status is not detected.
Actions:
•
Ensure that sensor Q325/326/327 are clean (Q325 and Q326 are located in the LCT, on the
jam clearance baffle on the lower part of the machine. Q327 is mounted on the clearance
baffle located on the exit side of the LCT, the closest one to the downstream device)
•
Check that there are no obstructions in the paper path
Jam recovery manual setting
In the following pages is the procedure for jam recovery using manual settings. Before
starting the adjustments, make sure that all the parameters are set to “auto” mode. Refer
to “setting sub-menus” in section 2 for how to adjust FAN power, Process Position and
Pickup Time.
Refer to “testing the changes” in section 2 to check if the sheets are floating correctly.
Refer to “Job Preparation” in section 1 for how to measure paper curl.
NOTE:
For components locations, refer to the
Guide to Components
section.
NOTE:
For components locations, refer to the
Guide to Components
section.