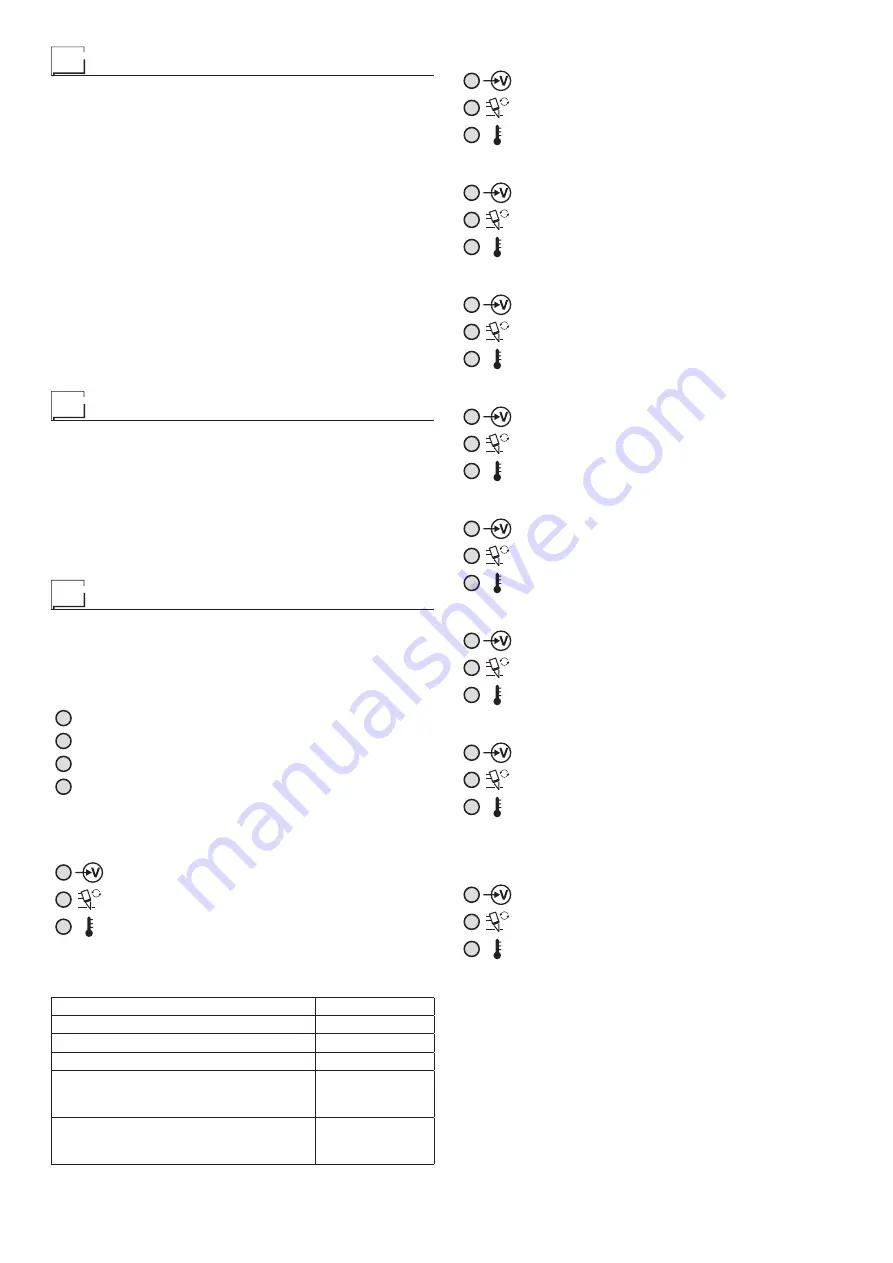
10
Connection to the mains supply
Before connecting the plasma cutting plant to the power
supply, check that the data on the plaque corresponds to
the power supply voltage and frequency and that the plant
line switch is in the “O” position.
This plant is designed for a nominal power supply of 230V
50/60 Hz.
Connection to the power supply must be effected using the plug
provided with the plasma cutting plant.
Table 2 lists the rating values for delayed line fuses chosen
on the basis of the nominal maximum power delivered by the
plasma cutting plant and the nominal power supply voltage.
Proceed as follows if you have to replace the plug:
• 2 conducting wires are needed for connecting the machine
to the supply
• The third, which is YELLOW GREEN in colour is used for
making the “EARTH” connection.
NOTE: If extensions of the power supply cable are used, they
must be of adequate cross section and never inferior to that of
the cable supplied.
Instructions for use
COMMAND AND CONTROL UNITS (Fig. A)
Pos. 1
Potentiometer for regulation of cutting current.
Pos. 2
White LED - power supply on. When on the system
is powered and ready for use.
Pos. 3
Red LED - plasma cutting cycle control.
Pos. 4
Yellow LED: signals intervention of overheat cutoff
Pos. 5
Earth wiring.
Pos. 6
Plasma torch.
Pos. 7
Main switch.
LED Sequences
The following are the principal combinations or sequences
which the LEDs on the
SHARK 25
rack panel may assume.
Important! Read this paragraph to fully understand correct plant
operation.
LED symbols legend
ON
LED on
OFF
LED off
LOW INT
LED flashing slowly
FAST INT
LED flashing rapidly
POWER ON
This sequence lasts a few seconds only from the moment in
which the operator actions the plant power switch.
ON
The plant has just been switched on
and the microprocessor is verifying the
correct function of each component.
FAST INT
FAST INT
PAUSE
ON
The plant is functional but no cutting
operations are being executed at this
time.
OFF
OFF
EFFECTIVE WORKING
ON
The plant is functional and the operator is
cutting at this time.
ON
OFF
“TIME OUT” PILOT NOT TRANSFERRED
ON
Alarm! The pilot arc has not transferred
to the item to be cut. The LED flashes for
some 15 seconds.
FAST INT
OFF
THERMOSTAT CUT OUT
ON
Alarm! Protective thermostat triggered.
Wait for the yellow LED to go off, several
minutes, the recommence cutting.
OFF
ON
UNDER-VOLTAGE OR OVER-VOLTAGE
ON
Alarm! Incorrect power supply voltage.
Power off the plant and verify that line
power corresponds to the data on the
plaque.
LOW INT
OFF
AIR PRESSURE
ON
Alarm! Air pressure insufficient (<2.5 bar).
Power off the plant and verify that the air
compressor is functioning correctly.
LOW INT
OFF
“SAFETY” TORCH ACTIVE
ON
Alarm! External torch nozzle mounted
incorrectly. Power off the plant and verify
- remount the plasma torch correctly.
LOW INT
OFF
POWERING OFF
This sequence lasts a few seconds from the moment in which
the operator actions the machine power supply switch.
ON
The plant has just been powered off
and the microprocessor is verifying the
correct function of each component.
FAST INT
OFF
Table 2
Model
SHARK 25
Power input @ I
2
Max
kVA
5
Delayed fuse
A
16
Duty cycle @ 35% (40°C)
A
25
Mains supply connection cable
Length
Section
m
mm
2
2,3
3×1,5
Earth cable
Length
Section
m
mm
2
3,5
4
Содержание SHARK 25
Страница 72: ...72 D A 95 B C E A B 6 25 7 7 A LED 2 A LED 3 A LED SHARK 25 SHARK 25 F 3 LED rack SHARK 25 LED LED E F D...
Страница 73: ...73 7 A LED 2 A inverter LED 4 A inverter inverter LED LED 3 A 2 5bar inverter Undervoltage overvoltage...
Страница 77: ...77 B SHARK 25 3 1 1 7 A 2 3 2 A 3 1 A 4 A C B C 5 2 A 3 A 1 2 3 4 5 6 7 A B C A...
Страница 78: ...78 D A 95 B C E A B 6 25 7 7 A 2 A 3 A SHARK 25 SHARK 25 F 3 SHARK 25 E F D...
Страница 79: ...79 7 A 2 A 4 A 3 A 2 5...