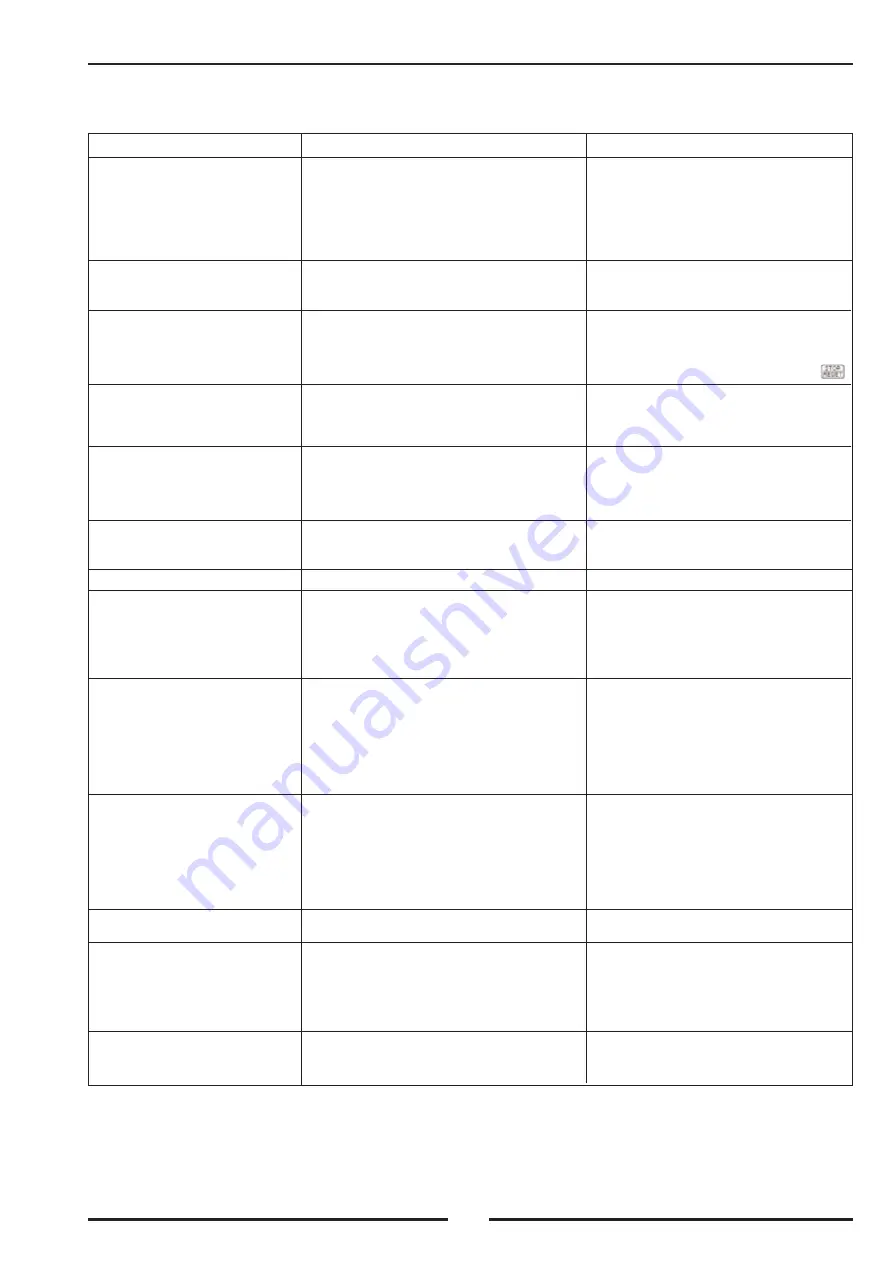
27
9. Failures - their Possible Causes and Elimination
Failure
Possible causes of failures
Failure elimination
The saw blade drive cannot be started
The motor is on, but the saw blade is not
moving
Red signal lamp in the control board
is on.
This work can be carried out only
by electrically qualified persons!
The cooling is irregular.
Vibrations during machining
Broken saw blade teeth seized in cutting
channel of the workpiece.
The cut is not rectangular
The saw blade undercuts
The saw blade breaks between the teeth
The saw blade breaks at face
Saw blade head feed into cutting
position is unstable
The saw blade head descends even
when the relief valve is shut off
The band saw head cannot be raised
• The master switch is off
• TOTAL STOP button is locked
• Protective overcurrent relay is off
• Band saw head guard limit switch not switched
• Control board fuse is blown
• Band saw head down, limit switch depressed
• The saw blade slips on driving wheel
• The saw blade is broken
• Some other gear box failure
• The saw blade guard is open.
• The saw blade is not tensioned.
• FQ3 motor starter for cooling dropped out.
• Protective function for frequency converter overload
has responded.
• The coolant is used up.
• The coolant tank and/or supply piping or ball valves
are fouled.
• The pump does not work.
• The saw blade feed is in unfavourable range.
• Incorrect saw blade tooth size has been selected
• Wrong setting of guide heads, carbides or bearings
• Wrong clamping of workpiece
• Incorrect setting of cutting angle
• The saw blade is blunt
• Incorrect saw blade tooth size
• Cutting feed too fast
• The saw blade slipped under guide bearings
• Clearance between carbides
• The workpiece is not fitted parallel to vice bed
• Incorrect saw blade tooth size
• Cutting feed too fast
• Guide head carbides incorrectly adjusted or damaged
(carbides, bearings)
• Distance between moving guide head and workpiece
is too big
• Insufficient cooling
• Wrong workpiece clamping for bundle cutting
• Saw blade incorrectly fitted on the moving wheels
(running on the shoulder)
• Incorrect saw blade tooth size
• Cutting feed too fast
• Guide head carbides incorrectly adjusted or damaged
(carbides, bearings)
• Distance between moving guide head and workpiece
too big
• Insufficient oil in hydraulic system
• M4 lock screw of control valve wheel is loose - it
turns through.
• Valve seat is worn out.
• Cylinder sealing is worn out.
• Valve failure (impurities).
• Band saw head ascending switch is set to 0.
• The master switch is off.
• The TOTAL STOP button is locked.
• Switch on the master switch
• Unlock TOTAL STOP button
• Check motor protective switch
• Check band saw head guard
• Replace the fuse
• The band saw head must be raised when the saw
blade is started
• Tension saw blade correctly, see chapter 5.6.
• Replace saw blade, see chapter 5.6.
• Contact service centre
• Close the guard, restart hydraulic unit.
• Tension saw blade, see chapter 5.6., restart hyd.
unit.
• Turn FQ3 switch to position I.
• Press STOP/RESET on frequency converter.
• Check coolant quality.
• Clean coolant tank and supply pipes.
• Replace the pump.
• Set saw blade feed into the cutting position by
approx. 5% lower/higher
• Check tooth size
• For adjustment see chapter 5.7.
• Check workpiece clamping
• Do not use a new saw blade for cutting in old
cutting channel! It could cause damage of the
the new saw blade in the first cut.
• See chapter 5.1.
• Replace the saw blade
• Check tooth size, see chapter 6.2.
• Adjust the feed
• Fit the saw blade correctly, see chapter 5.6.
• Adjust the carbides, see chapter 5.7.
• Align roller conveyor, check workpiece clamping
• Check tooth size, see chapter 6.2.
• Adjust the feed
• Adjust them, see chapter 5.7., and/or replace them
• Reduce distance, see chapter 5.5.
• Supply more coolant
• Clamp workpiece thoroughly.
• Check the saw blade, see chapter 5.6.
• Check tooth size, see chapter 6.2.
• Adjust the feed.
• Adjust them, see chapter 5.7., and/or replace them
• Reduce distance, see chapter 5.5.
• Contact the service centre.
• Tighten M4 lock screw
• Loosen M4 screw, turn control wheel through
approx. 10° to the left and tighten it.
• Contact the service centre.
• Contact the service centre.
• Switch over to 1.
• Switch on the master switch.
• Unlock the TOTAL STOP button by pulling up.
Содержание 20875-0204
Страница 5: ...4 ARG 380 Plus S A F ARG 500 Plus S A F...
Страница 35: ...34 ARG 380 Plus S A F ARG 500 Plus S A F...
Страница 65: ...64 ARG 380 Plus S A F ARG 500 Plus S A F...
Страница 92: ...91...
Страница 93: ...92...
Страница 94: ...93...
Страница 95: ...94...
Страница 96: ...95...
Страница 97: ...96...
Страница 98: ...97...
Страница 99: ...98...
Страница 100: ...99...
Страница 101: ...100...
Страница 102: ...101...
Страница 103: ...102...
Страница 104: ...103...
Страница 105: ...104...
Страница 106: ...105...
Страница 107: ...106...
Страница 108: ...107...
Страница 109: ...108...
Страница 110: ......