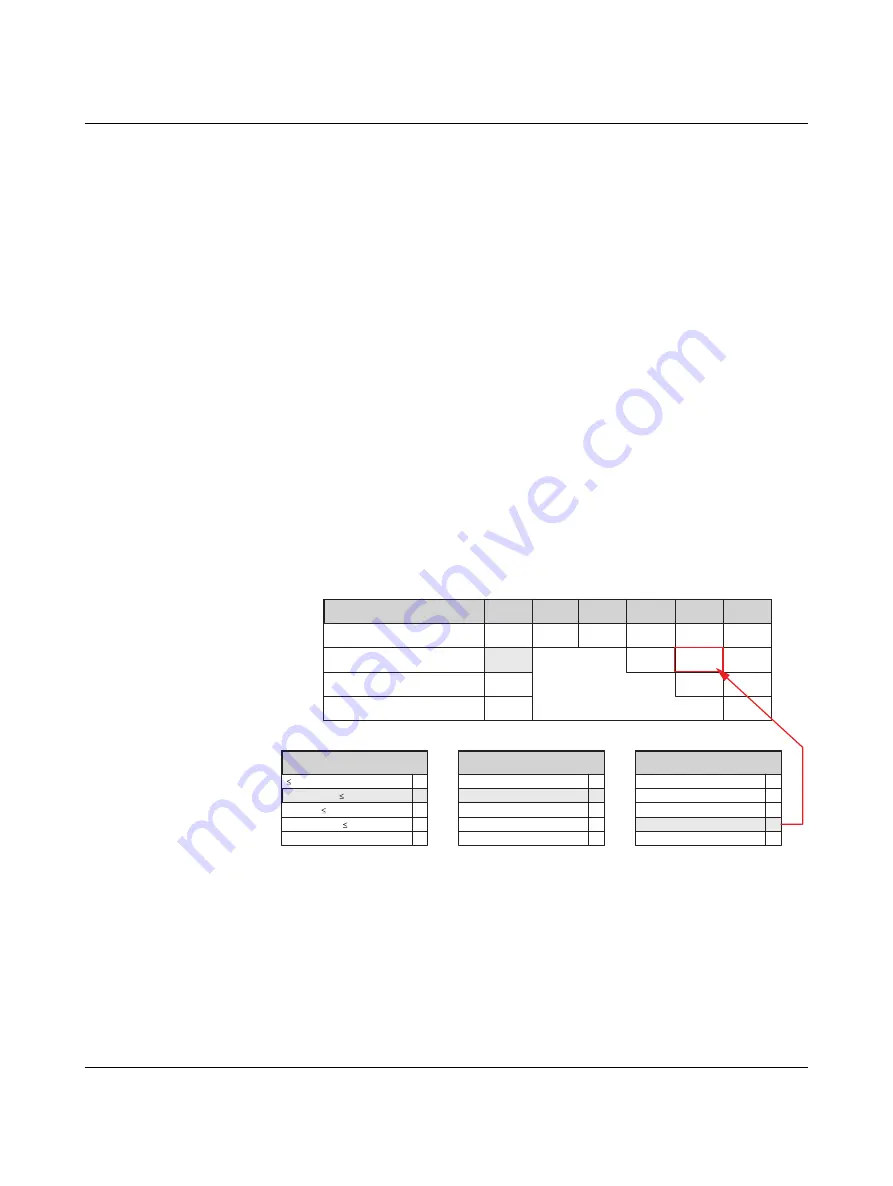
Safety of machines and systems
102597_en_03
PHOENIX CONTACT
2.3
Practical procedure in accordance with
EN ISO 62061
In practice, the following steps have proven effective when designing safe control systems
according to EN 62061.
2.3.1
Specification of requirements for the safety-related control
function (SRCF)
The safety function must be defined first. This information is derived from the risk assess-
ment.
Example:
2.3.2
Determination of the required safety integrity level (SIL)
The required SIL is determined in combination with the safety function within the framework
of the higher-level risk assessment.
Figure 2-5
Example of specifying the SIL (in accordance with EN 62061)
2.3.3
Drafting the safety-related electrical control system
(SRECS)
This step involves the technical pre-planning of the safety function, taking possible technol-
ogies and components into account. The safety-related components and parts must then
be identified for later verification.
Trigger event:
Opening the safety door.
Response:
The robot drive is set to a safe stop state. The power semicon-
ductor pulses are disabled.
Safe state:
Power circuit has no power.
>
>
>
>
5
5
5
4
4
4
4
3
3
3
2
2
2
+
+
3
4
2
1
SIL 2
SIL 2
SIL 2
SIL 3
SIL 3
SIL 1
SIL 2
SIL 3
SIL 1
SIL 3
SIL 1
S
3 - 4
5 - 7
8 - 10
11 - 13
14 - 15
Death, loss of an eye
or arm
Permanent, loss of a
finger
Reversible, medical
treatment
Reversible, first aid
Effect
Severe
Class
Class
Class
Class
Class
Other measures
F Frequency and duration
F Probability of a
dangerous event
P Avoidance
Impossible
Possible
Probability
Frequent
Probable
Possible
Rare
Negligible
1 hour
1 hour to
Day to
2 weeks to
1 year
1 day
2 weeks
1 year
Содержание 2702924
Страница 137: ......