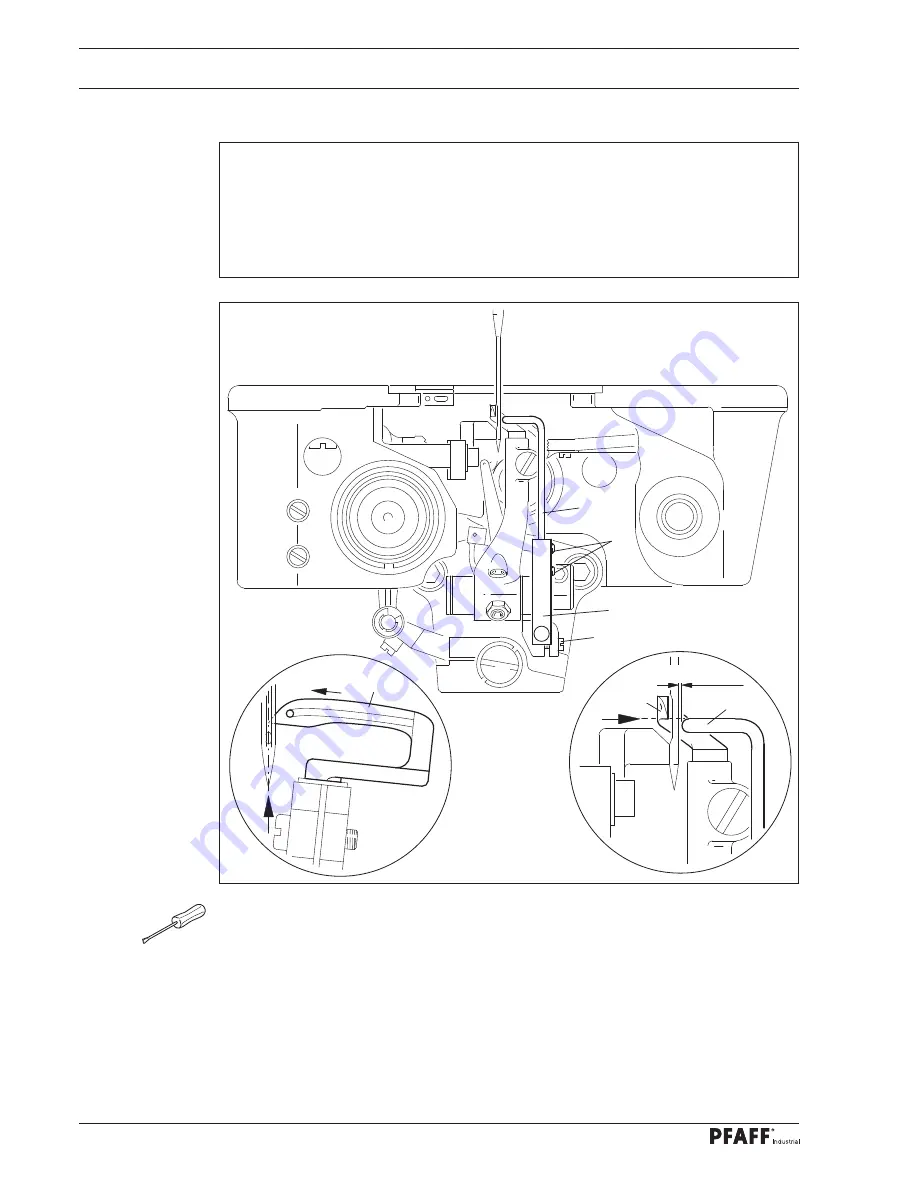
Adjustment
98
Fig. 13 - 29
4
5
3
2
13
.05.29
Position of the front needle guard
Rule
When the looper point
1
is in the centre of the needle coming from the right side, the nee-
dle guard bar should
4
1. have a lateral clearance
0.3
-
0.5 mm
to the needle,
2. stand parallel to the hook blade and
3. the top edge should stand at the same height as the point of looper
1.
Move to the hook by turning handwheel
1
to its left reversal point.
Loosen the screws
2.
Move the needle guard carrier
3
so that the needle guard bar
4
does not strike the looper
1
in this position.
Gently tighten the screws
2.
Turn the handwheel until the point of the looper
1
is in the centre of the needle coming
from the right.
Turn the needle guard carrier
3
according to rule
1
.
Adjust the needle guard bar
4
(screws
5
) according to rules
2
and
3
.
1
0.3 - 0.5 mm
4
1
Содержание 3811-15/65
Страница 6: ...Table of Contents Contents Page...
Страница 135: ...135 16 Table Top 16 01 Table top cutout Table top assembly deep...
Страница 137: ...Notes...