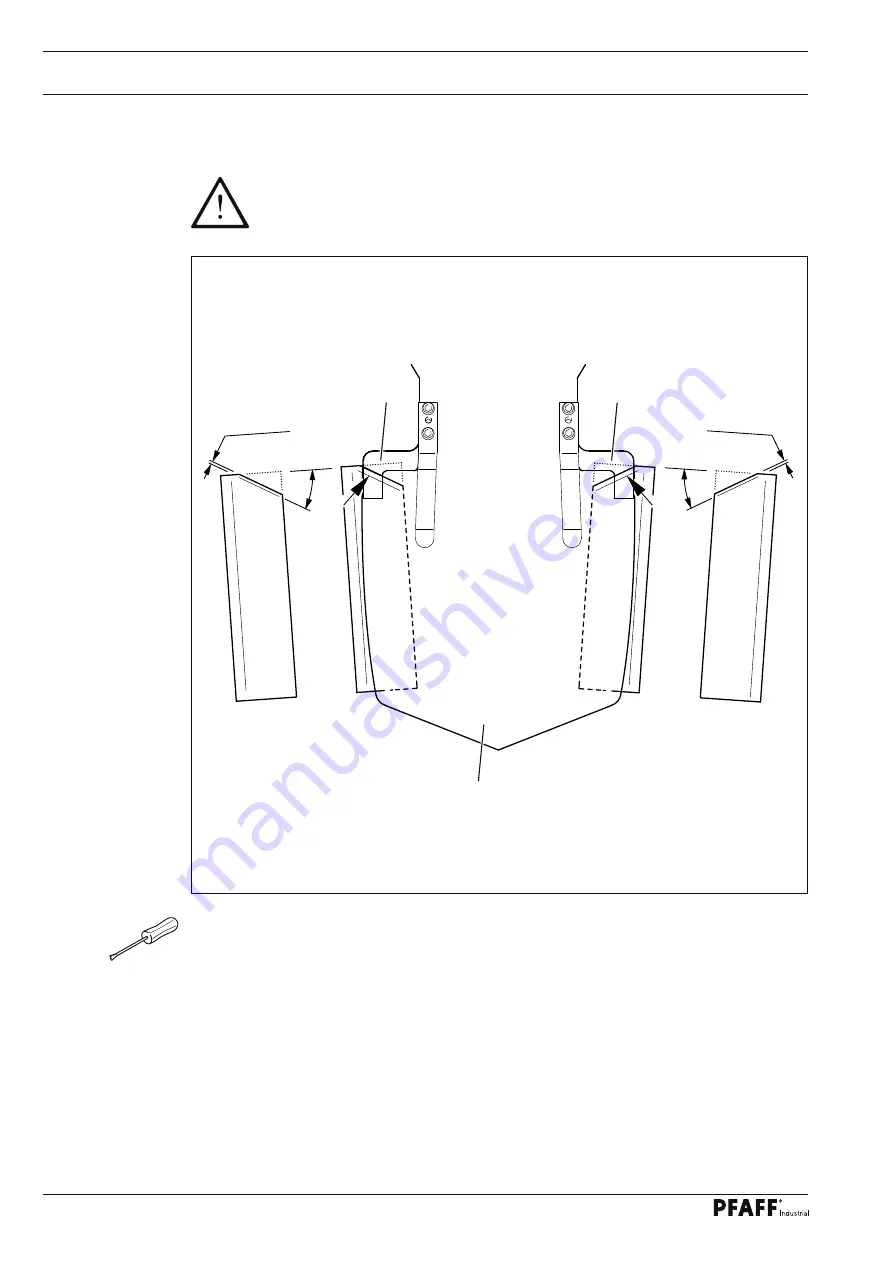
138
Adjustment
13
.07.02
Slanting the lateral folder plates
Do not begin with this work process until the adjustments in chapters
13
.
06
.12
Aligning the seam in relation to the pocket
and 13.06.13
Seam backtack dis-
tance
have been carried out!
●
With the folder plates fully extended, transfer the front edges of the stops
1
and the
outer edge of the pocket plate
2
to the lateral folder plate.
●
Trace slanted edge of
30°
.
●
Work the folder plate up to
1
-
2
mm
before the trace.
●
Round off the edges of the folder plate and polish.
2
1
1
1 - 2 mm
30°
30°
1 - 2 mm
Fig. 13 - 46
Содержание 3588-05/020
Страница 16: ......
Страница 32: ......
Страница 68: ...Input 68 Tact forwards Call up jig with obstacles with the edit function Tact forwards...
Страница 82: ......
Страница 179: ...179 91 191 367 95 Version 08 12 00 Terminals X 1...
Страница 180: ...180 Cirguit diagrams Version 02 05 12 91 191 570 95 Part 1...
Страница 181: ...181 91 191 570 95 Part 1a Version 02 05 12 Cirguit diagrams...
Страница 182: ...182 Cirguit diagrams Version 02 05 12 91 191 570 95 Part 2...
Страница 183: ...183 91 191 570 95 Part 2a Version 02 05 12 Cirguit diagrams...
Страница 184: ...184 Cirguit diagrams Version 02 05 12 91 191 570 95 Part 3...
Страница 185: ...185 91 191 570 95 Part 4 Version 02 05 12 Cirguit diagrams...
Страница 186: ...186 Cirguit diagrams Version 02 05 12 91 191 570 95 Part 5...
Страница 187: ...187 91 191 570 95 Part 6 Version 12 12 12 Cirguit diagrams...
Страница 188: ...188 Cirguit diagrams Version 02 05 12 91 191 570 95 Part 7...
Страница 189: ...189 91 191 570 95 Part 8 Version 02 05 12 Cirguit diagrams...