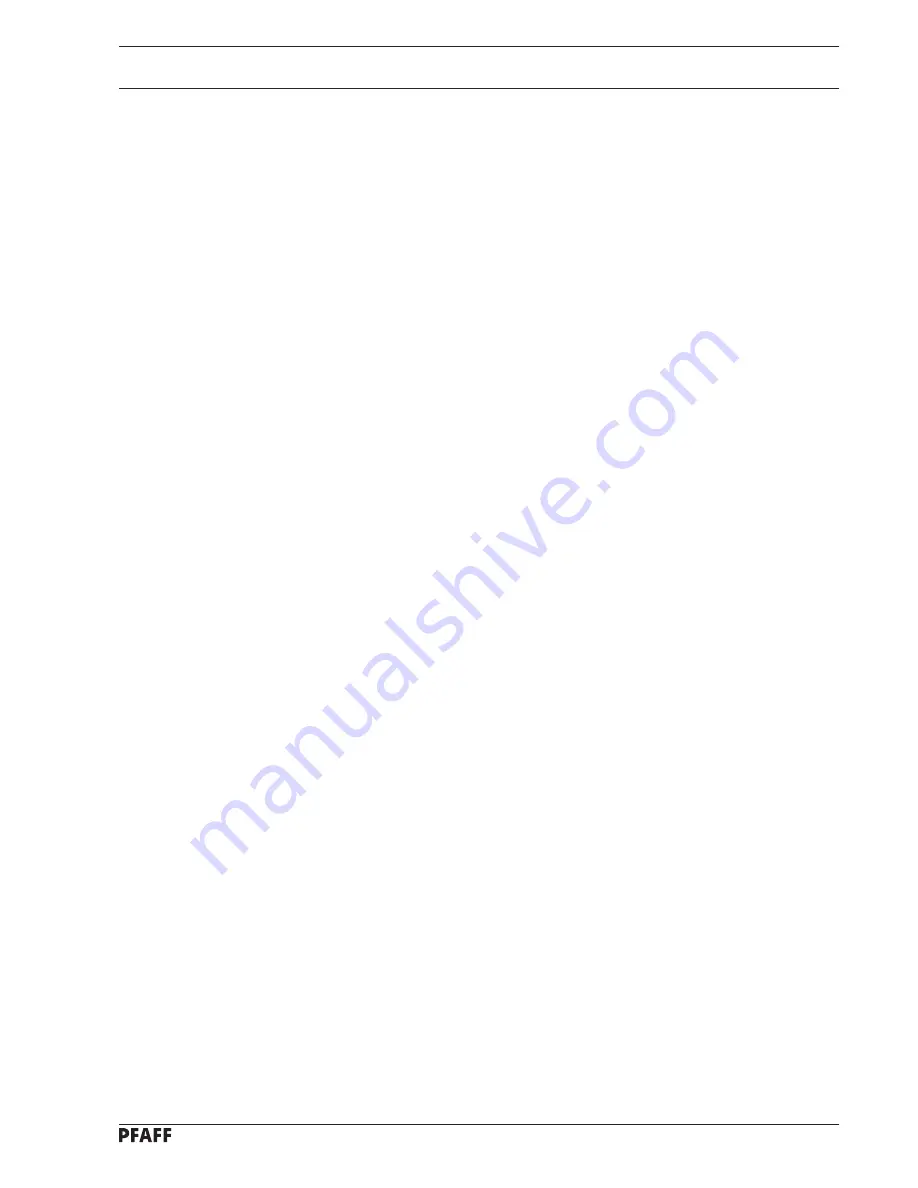
Transport, packaging and storage
5 - 1
5
Transport, packaging and storage
5
.01
Transport to the customer’s premises
Within Germany, machines are delivered without packaging.
Machines for export are packaged.
5
.02
Transport within the customer’s premises
The manufacturer bears no liability for transport within the customer’s premises or to the
location of use.
The machine may only be transported in an upright position.
5
.03
Disposal of the packaging
The packaging of these machines consists of paper, cardboard and VCE fiber.
The proper disposal of the packaging is the responsibility of the customer.
5
.04
Storage
The machine can be stored for up to 6 months if not in use. During this time it should be
protected from dust and moisture.
For longer storage the individual parts of the machine, especially the moving parts, should
be protected against corrosion, e.g. by a film of oil.
Содержание 3588-04/020
Страница 1: ...296 12 18 145 Betriebsanleitung engl 05 99 3588 04 020 Instruction Manual...
Страница 53: ......
Страница 54: ......
Страница 99: ...12 8 Care and maintenance...
Страница 174: ......
Страница 180: ...15 5 91 191 386 95 Part 1 Version 24 07 97 Circuit diagram Overview...
Страница 181: ...15 6 Circuit diagram Overview Version 14 02 97 91 191 386 95 Part 2...
Страница 182: ...15 7 91 191 386 95 Part 3 Version 24 07 97 Circuit diagram Overview...
Страница 183: ...15 8 Circuit diagram Overview Version 24 07 97 91 191 386 95 Part 4...
Страница 184: ...15 9 91 191 386 95 Part 5 Version 24 07 97 Circuit diagram Overview...
Страница 185: ...15 10 Mains supply 230 V Version 23 07 97 91 191 360 95...
Страница 186: ...15 11 91 191 367 95 Version 24 07 97 Terminals X1...
Страница 187: ...15 12 Circuit diagram A20 A21 Version 14 02 97 91 191 387 95...
Страница 188: ...15 13 91 191 388 95 Version 14 02 97 Circuit diagram A20 A22...
Страница 189: ...15 14 Circuit diagram A11 L1 Version 05 03 99...
Страница 190: ...15 15 Version 24 07 97 Circuit diagram A11 L2...
Страница 191: ...15 16 Circuit diagram A12 L3 Version 24 07 97...
Страница 192: ...15 17 Version 24 07 97 Circuit diagram A12 L4...
Страница 193: ...15 18 Circuit diagram A13 L5 Version 05 03 99...
Страница 194: ...15 19 Version 05 03 99 Circuit diagram A13 L6...
Страница 195: ......