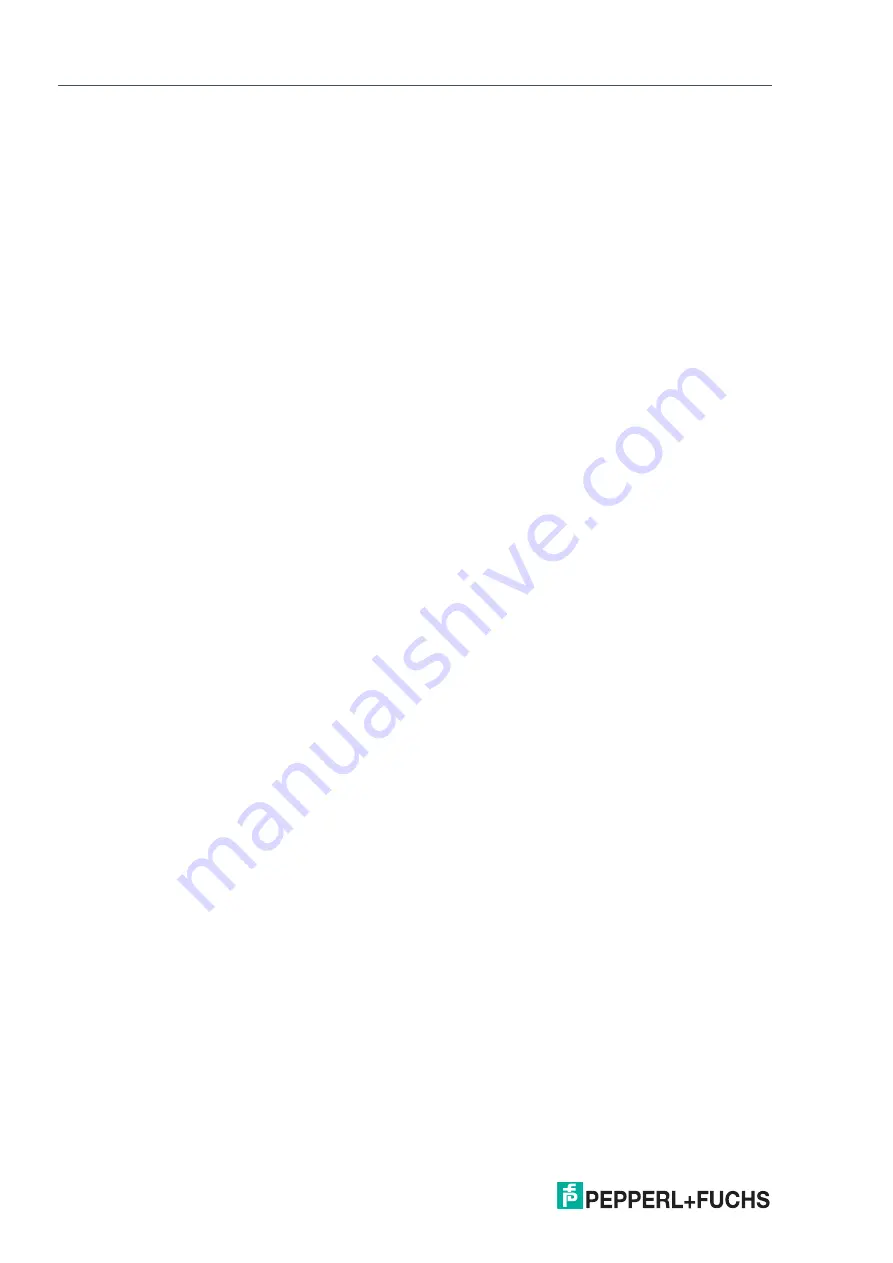
2
0
2
0
-0
6
8
Product Description
Parameter storage
•
The Parameter Storage function stores and monitors the parameters of the IO-Link device
and the IO-Link master.
•
This function makes it possible for you to easily replace the IO-Link device or the IO-Link
master.
This is possible from IO-Link specification V1.1 onward and only if the IO-Link device and
the IO-Link master support the function.
IO-Link device parameterization
•
The IO-Link devices can be parameterized in the PROFINET protocol using the Siemens
IO_LINK_DEVICE function block for STEP 7 and the TIA Portal.
Special Product Features
•
Rugged design:
Connectivity options for the module series include the widespread M12 connector with A
coding for I/O signals and D coding for the network. In addition, the connectors are color-
coded to prevent users from using the wrong ports. The output circuits are galvanically
isolated from the rest of the network and the sensor electronics. Controllers are therefore
reliably protected against noise.
•
Integrated web server:
Network parameters such as IP address, subnet mask, and gateway can be adjusted via
the integrated web server. The modules support the communication protocols BOOTP
and DHCP for automated assignment of network parameters via the corresponding serv-
ers.
You can read the parameters of the IO-Link device via the integrated web server and write
new parameters to the modules in single-write mode. Single-write mode does not activate
the automatic parameter storage mechanism.
•
Force Mode
In Force Mode, the module ports can be temporarily configured as digital inputs/outputs or
IO-Link ports. The configuration applies until the module is next switched off.
"Force Mode" allows the simulation of process data at the digital inputs/outputs without
the need to connect sensors and actuators. This means that you can test an application in
advance without a full physical application. It is possible to simulate input switching states
or to switch outputs even without a controller. This feature makes machine commissioning
simpler and quicker and can be used to test new production plants.
•
Integrated network switch:
The integrated two-port Ethernet switch of the modules allows you to set up a line topol-
ogy or a ring topology for the EtherNet/IP network or PROFINET network. The additional
DLR or MRP protocol allows you to design a highly available network infrastructure.
•
Redundancy function:
The module firmware supports the redundancy function DLR (Device Level Ring) or MRP
(Media Redundancy Protocol) for ring topologies. This means that if the connection is
interrupted, the modules switch immediately to an alternative ring segment and thus
ensure interruption-free operation. The supported DLR class is "beacon-based" in accor-
dance with the EtherNet/IP specification.
•
Fail-safe function:
The modules provide a fail-safe function. You can therefore choose the behavior of each
individual output channel in the event of an interruption or a loss of communication.