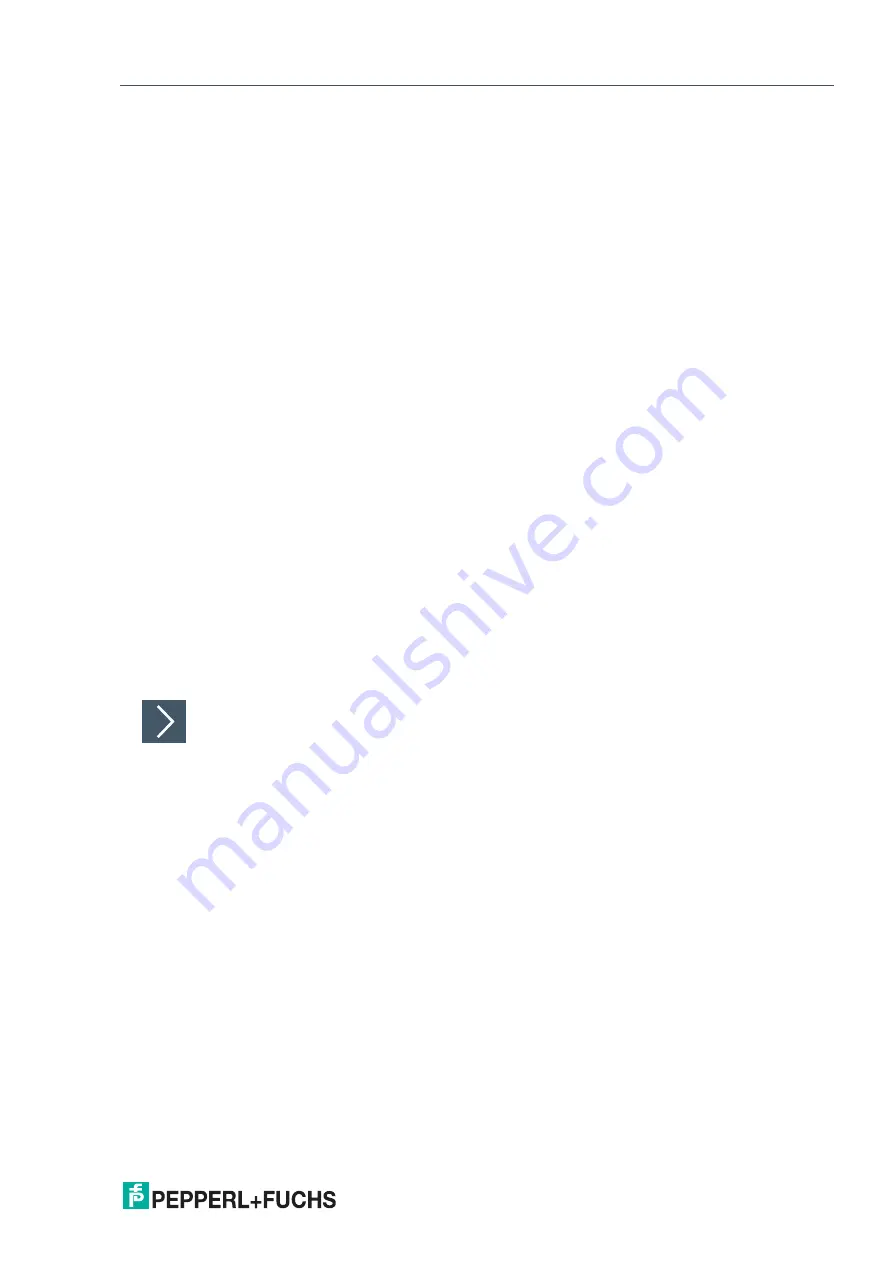
Commissioning for PROFINET
2
0
2
0
-0
6
33
•
1.6 ms, 3.2 ms, 4.8 ms, 8 ms, 20.8 ms, 40 ms, 80 ms, 120 ms
You can manually set the cycle time to the options provided. This option can be used for
IOL device modules that are connected via inductive couplers. Inductive couplers are
usually the bottleneck in the update cycle time between IOL master and IOL device. In this
case, refer to the datasheet of the inductive coupler.
Default: As fast as possible
Vendor ID
The "IO-Link Manual" port mode is required for the "Vendor ID" option.
The manufacturer identifier of the connected IOL device can be entered as a decimal value
[0 ... 65535] and is used for validating type compatibility depending on the "Validation and
Backup" settings.
Default: 0
Device ID
The "IO-Link Manual" port mode is required for the "Device ID" option.
The device ID of the connected IOL device can be entered as a decimal value [0 ... 65535] and
is used for validating type compatibility depending on the "Validation and Backup" settings.
Default: 0
5.2.6
Parameterization of the Status/Control Module
The status/control module in slot 1/subslot 1 is permanently preconfigured for each module. It
contains 2 bytes of input data and 2 bytes of output data for the digital IO data plus status and
control bits of the IO-Link master.
The bit assignments are described in the main chapter "Commissioning for PROFINET" in the
"Bit Assignment" chapter (See chapter 5.3).
Using the status/control module, it is also possible to carry out all of the global module-specific
parameterization that is not related to ports in the IO-Link COM mode.
1.
Select "Device View" (1) and the desired module (2) (in this example, slot 1 with an 8IOL
module).
2.
Then, in the "General" tab, select the "Module parameters" (3) area.