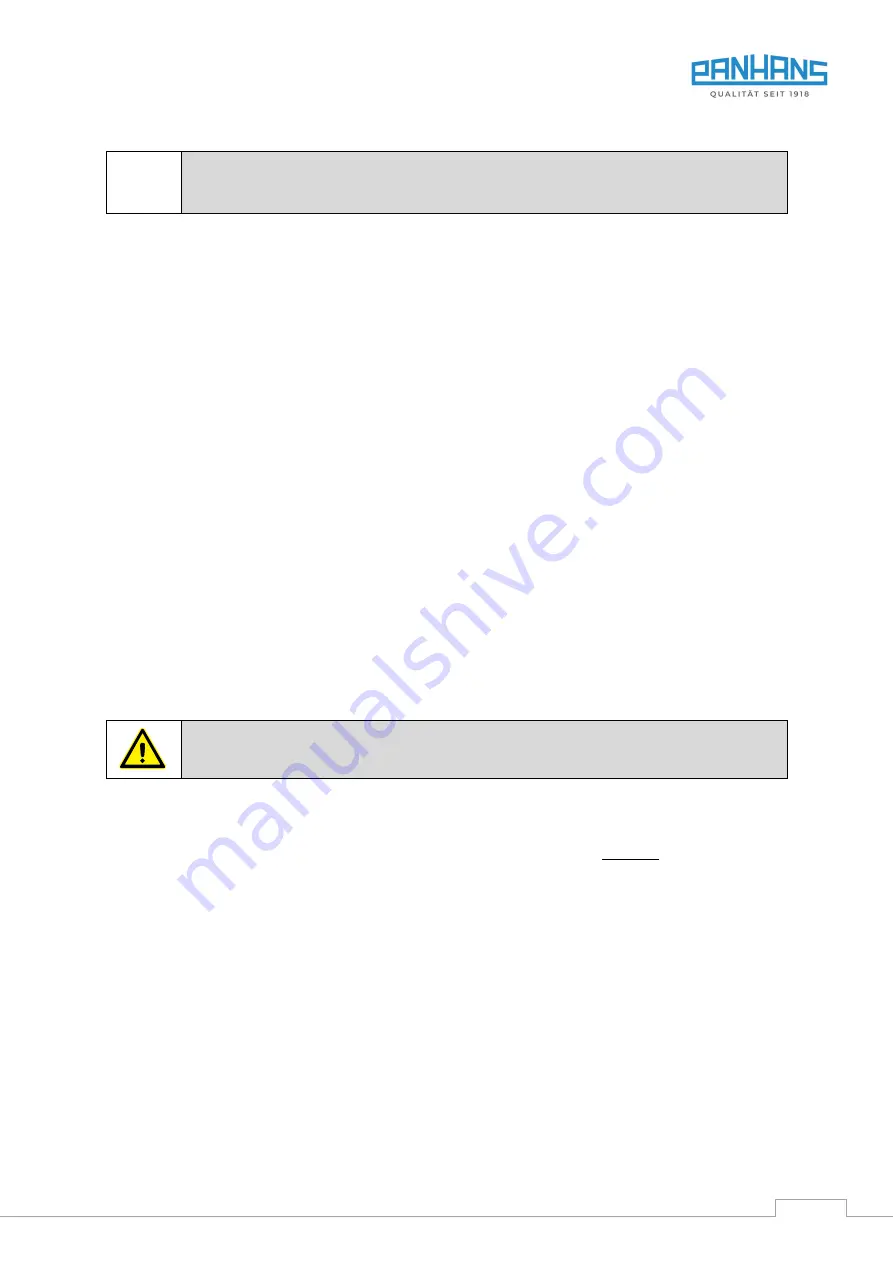
BA_PH_3V_EN_07-22.docx
48
17
Maintenance and Inspection
Before any maintenance and inspection work is carried out, chapter
5 "Safety" must
be read carefully and observed!
Operational malfunctions caused by insufficient or improper maintenance can result in very high repair costs and
long machine downtimes. Regular maintenance is therefore essential.
•
Clean the machine daily.
•
Check all sliding or rolling parts weekly for smooth running and lubricate with a thin-bodied oil if necessary.
•
Inspect electrical equipment/components weekly for externally visible damage and have them repaired by
a qualified electrician if necessary.
•
Immediately remove and replace damaged guards. Never work with damaged equipment!
•
Before starting work, check the extraction system for full function every day.
•
The extraction system must be checked for obvious defects before initial commissioning, daily and monthly
to ensure its effectiveness.
•
The air velocity to the extraction system must be checked before the initial commissioning and after signifi-
cant modifications.
•
The function of the gas springs should be checked occasionally. If it takes a lot of force to open the protec-
tive cover, the gas springs must be replaced.
•
Do not use the machine until these conditions are met.
Due to the different operating conditions, it is not possible to determine in advance how often a wear check,
inspection or maintenance is required. Inspection intervals are to be determined appropriately according to the
respective operating conditions.
17.1
Replace Ball Bearings
If the ball bearings become noisy or have play, they must be replaced. To do this, the corresponding bandsaw
wheel must be removed to make the old ball bearings accessible and replace them with new ones.
Switch off the machine during maintenance and repair work and secure it against being
switched on again unexpectedly! Lock the main switch with a padlock!
To remove or install the ball bearings, use a suitable device (e.g. puller / mounting tube) to avoid damaging the
bearings.
•
The type designation of the ball bearings for the 3-wheel bandsaw type 3V is
6305 2RS
.
Содержание 3V
Страница 2: ...BA_PH_3V_EN_07 22 docx 2 Space for notes...
Страница 4: ...BA_PH_3V_EN_07 22 docx 4 Space for notes...