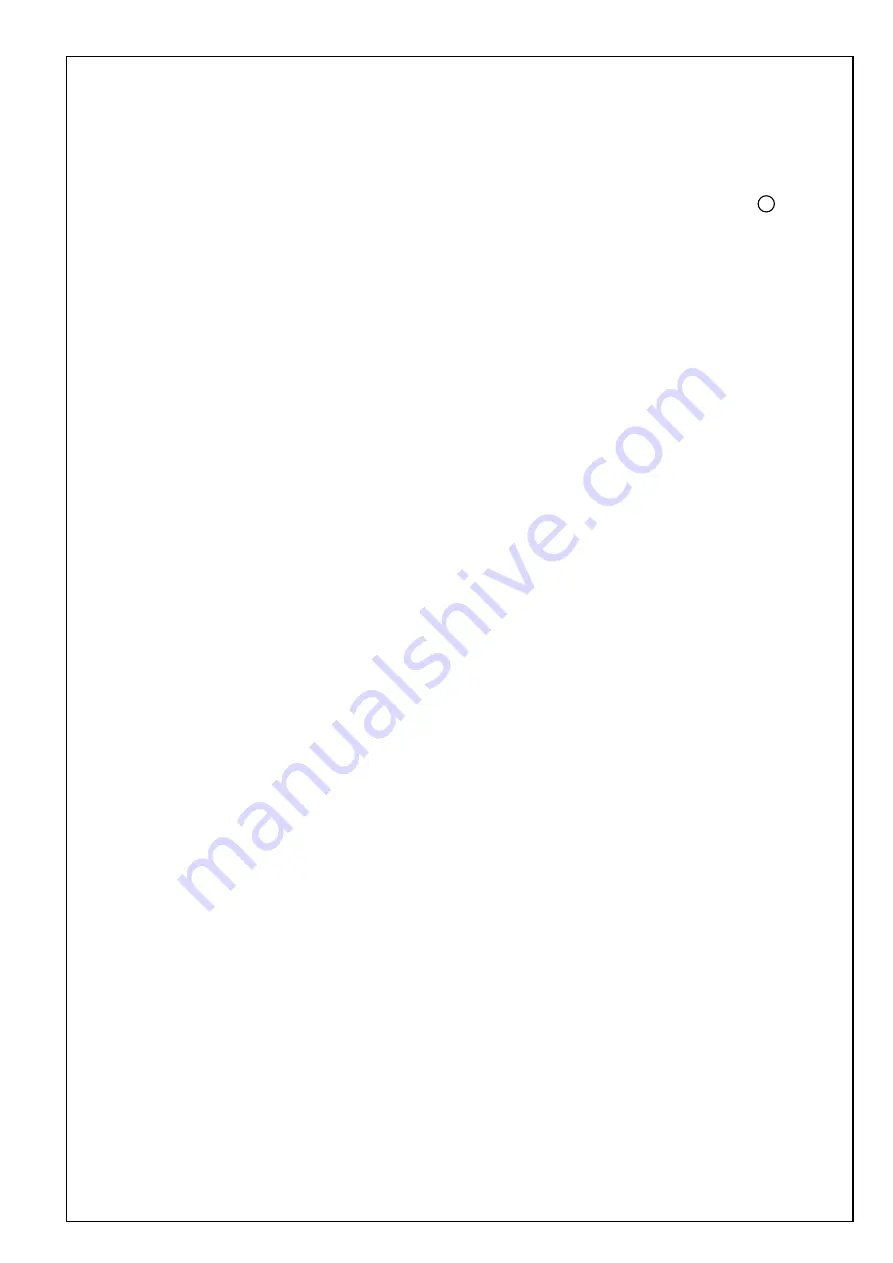
No. SX-DSV03015 - 55 -
Motor Business Unit, Panasonic Corporation
9-5 Compliance with UL standard
Certified by the UL508C (file No. E164620) standard by observing the installation conditions 1, 2 below.
[1] Installation environment
Use the servo driver under the environment of pollution level 2 or 1 defined in IEC60664-1.
(Example: Installed in the IP54 control panel.)
Make sure to connect a circuit breaker or fuse compliant with UL certification (marked with LISTED, )
between the power supply and the noise filter.
For information about rated current of the circuit breaker/ fuse, refer to "9-4 List of peripheral devices
applicable to servo driver".
For wiring, use the
copper conductor cable of the temperature rating 75deg.Celsius or more.
The terminal block can
be damaged if the screw tightening torque exceeds the maximum value.
(
See the page for explanation of terminal blocks.)
[2] Short Circuit Current Ratings (SCCR)
This servo driver compiles with the power of the following conditions.
- The power supply voltage is less than the maximum input voltage of the product.
- Symmetrical short current of the power supply is less than 5000A.
[3] Protection of branch circuit
Protection of branch circuit, please follow the NEC(National Electrical Code) and Standard regional.
[4]
Overload protection, overheat protection
The
overload protection function of the servo driver works when the effective current will be 115 % or more of
the rated current based on the time property. Check that the effective current of the servo driver does not exceed
the rated current. Set up the maximum instantaneous allowable current at the Pr0. 13 (first torque limit) and
Pr5.22 (
second torque limit).
There is no overheat protection in the servo motor. If you need to conform to the NEC, please implement the
overheating protection measures.
UL