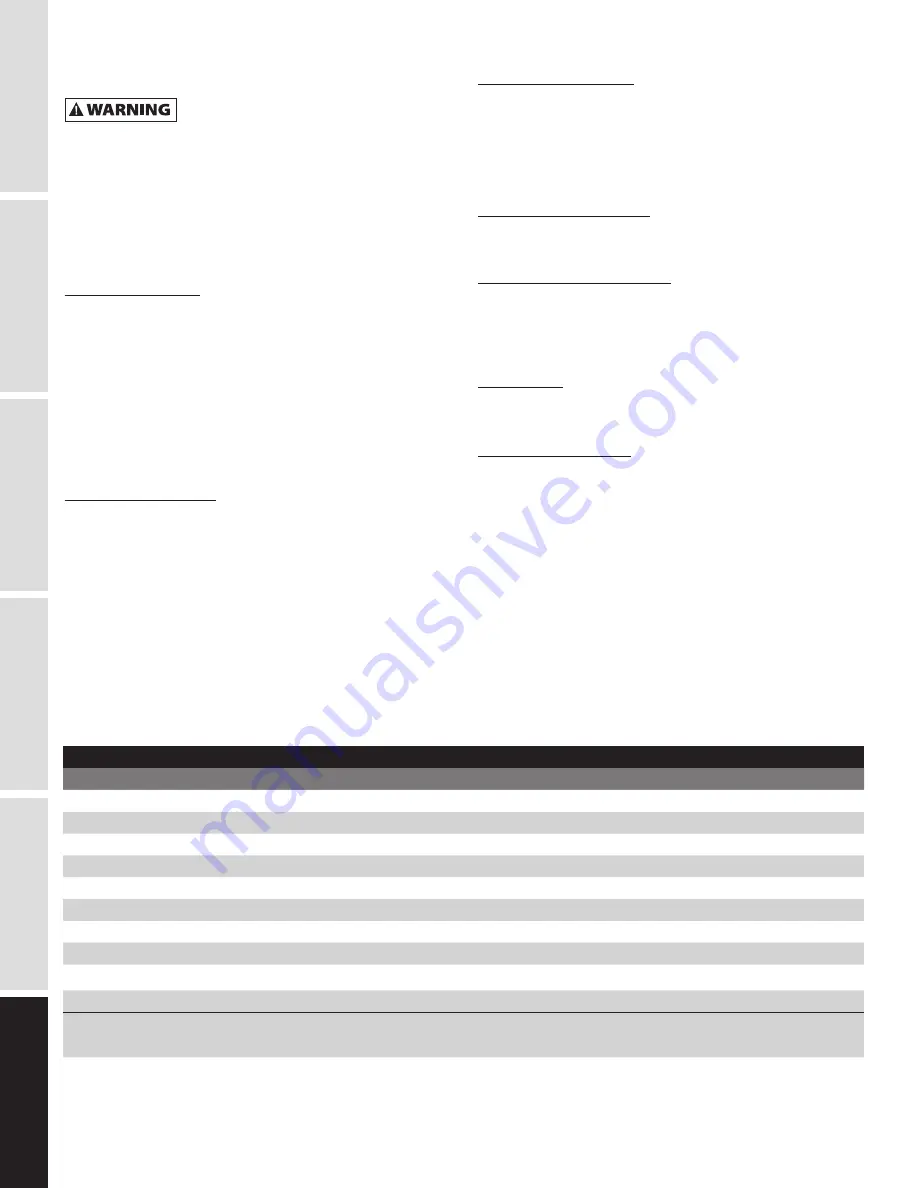
MAINTENANCE / REPAIR
TROUBLESHOOTING
OPERATION
ASSEMBLY / INSTALLATION
SAFETY / SPECIFICATIONS
GETTING STARTED
46
ROUTINE AND SPECIAL MAINTENANCE
Always disconnect the machine from its
power source before changing blades or
carrying out any maintenance procedure even in the case of
irregular machine operation.
Any special maintenance must be performed by certified
professionals. Do not remove parts for maintenance.
The maintenance jobs are listed below, divided into daily, weekly,
monthly and six-month intervals. If the following operations are
neglected, the result will be premature wear of the machine and
poor performance.
Daily maintenance
•
Give general cleaning to the machine to remove
accumulated shavings.
•
Clean the lubricating coolant drain hole to avoid excess fluid.
•
Top off the level of lubricating coolant.
•
Check blade for wear.
•
Rise of saw frame to top position and partial slackening of
the blade to avoid useless yield stress.
•
Check functionality of the shields and emergency stops.
Weekly maintenance
•
Thoroughly clean the machine to remove shavings,
especially from the coolant tank.
•
Removal of pump from its housing, cleaning of the suction
filter and suction zone.
•
Clean the filter of the pump suction head and the suction
area.
•
Use compressed air to clean the blade guides (guide
bearings and drain hole of the lubricating cooling).
•
Clean flywheel housings and blade sliding surfaces on
flywheels.
Monthly maintenance
•
Check the tightening of the drive wheel screws.
•
Check that the blade guide bearings on the heads are perfect
running condition.
•
Check the tightening of the screws of the motor, pump, and
accident protection guarding.
Six-month maintenance
•
Test the continuity of the equipment potential protection
circuit.
Oils for lubricating coolant
Considering the vast range of products on the market, the user
can choose the one most suited to their own requirements, using
as reference the type SHELL LUTEM OIL ECO. THE MINIMUM
PERCENTAGE OF OIL DILUTED IN WATER IS 8 - 10%.
Oil disposal
Please disposal of these products in an environmentally
conscious fashion.
Special maintenance
Special maintenance must be performed by certified
professionals. We advise contacting your nearest dealer and/
or importer. Other protective and safety equipment, devises (of
the reducer), the motor, the motor pump, and other electrical
components also require special maintenance.
ROUTINE AND SPECIAL MAINTENANCE CHART
Item
Part
Lubricant
Quantity
Routine
Remark
1
Bench vise slides
Machine oil
Suitable
Everyday
Oil after cleaning
2
Shuttle vise slides
Machine oil
Suitable
Everyday
Oil after cleaning
3
Lubricant fluid tank
Water-soluble cutting fluid
High level on gauge
Everyday
4
Worm gear
Grease
Suitable
Every month
5
Drive wheel oil nipple
Grease
Suitable
Two weeks
6
Idle wheel oil nipple
Grease
Suitable
Two weeks
7
Slide of slide seat
Machine oil
Suitable
Two weeks
8
Shuttle vise shorter jaw
Grease
Suitable
Two weeks
Oil after cleaning
9
Transmission gear box
Gear oil # 90
Middle level on gauge
Six months
Every year after the first
10
Hydraulic system tank
Hydraulic Oil AW-46
High level on gauge
Six months
Every year after the first
* Clean the chips from the flywheel housings and bench vises everyday for optimum performance.