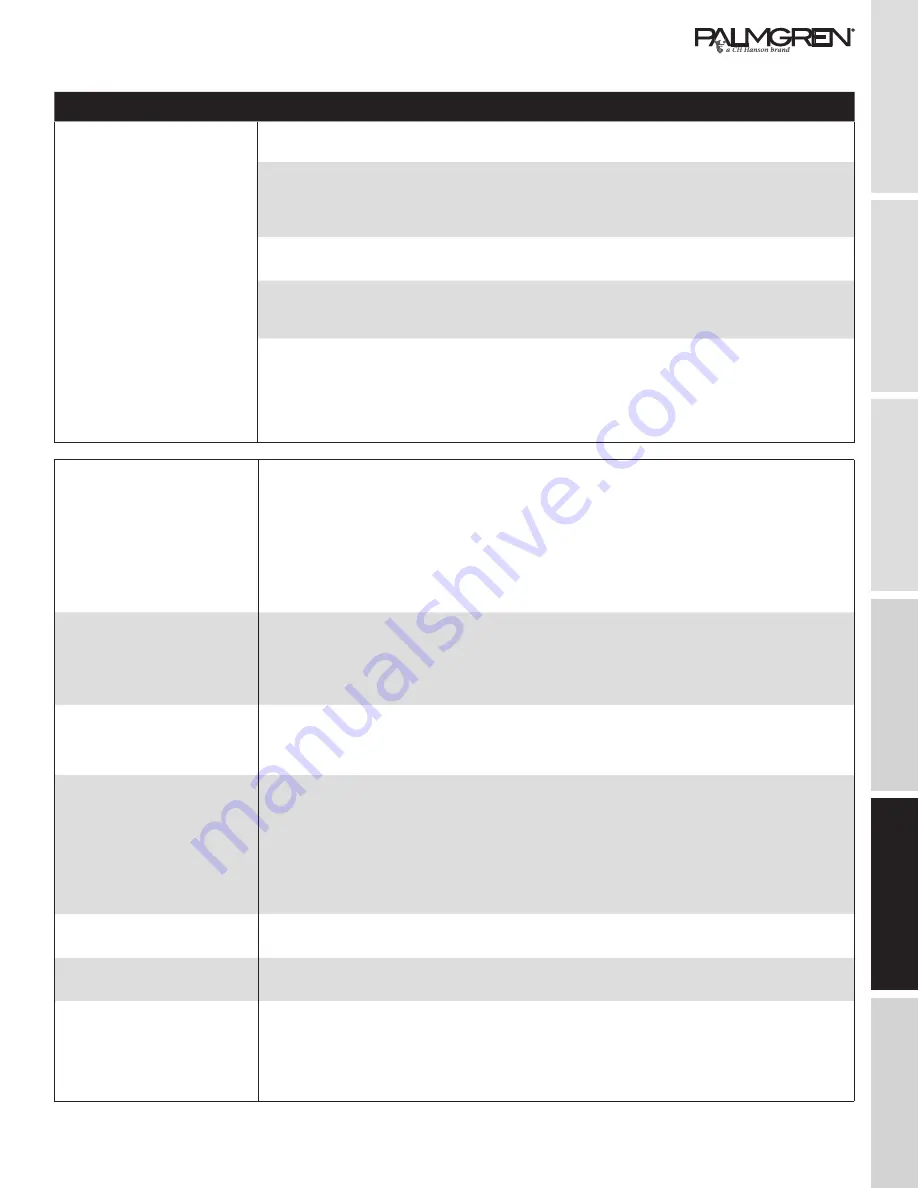
23
GETTING STARTED
SAFETY / SPECIFICATIONS
ASSEMBLY / INSTALLATION
OPERATION
TROUBLESHOOTING
MAINTENANCE / REPAIR
Motor will not start; fuses or
circuit breakers blow
1. Short circuit in line cord or plug
2. Short circuit in motor or loose
connection
3. Incorrect fuses or circuit breakers in
power line
4. Motor overloaded
1. Inspect line cord or plug for damaged insulation
and shorted wires. Replace damaged wires and/or
components.
2. Inspect all lead terminals on motor for loose or worn
insulation on wires. Tighten any loose connections.
Replace or repair motor.
3. Install correct fuses or circuit breakers
4. Reduce load on motor
Motor fails to develop full
power (power output of
motor decreases rapidly) with
decreased voltage at motor
terminals
1. Power Line overloaded
2. Undersized wires or cords too long
3. General overloading at power
company’s facilities
1. Reduce the load on the power line
2. Increase the wire sizes or reduce the length of cords
3. Request a voltage check from the power company
Motor overheats
1. Motor overloaded
1. Reduce load on motor
2. Air circulation around motor is
restricted
2. Clean motor to provide normal air circulation around
motor
Motor stalls (resulting in blown
fuses or tripped circuit breakers)
1. Short circuit in motor; connections
loose; or shorted terminals; or worn
insulation on lead wires
2. Low voltage line conditions
3. Incorrect fuses or circuit breakers in
power line
4. Motor overloaded
1. Inspect all lead terminals on motor for loose or worn
insulation on wires. Tighten any loose connections.
Replace or repair motor.
2. Correct low voltage line conditions
3. Install correct fuses or circuit breakers
4. Reduce load on motor
Frequent opening of fuses or
circuit breakers
1. Motor overloaded
2. Incorrect fuses or circuit breakers
1. Reduce load on motor
2. Install correct fuses or circuit breakers
Motor problems in general
Various causes
To troubleshoot and service the motor consult a
qualified technician
Motor running too hot
1. Blade tension too high
2. Blade too coarse for work (especially
when cutting pipes)
3. Blade too fine for work (heavier, soft
materials)
1. Reduce tension on the blade
2. Change the type of blade to better match the
material being cut.
3. Change the type of blade to better match the
material being cut.
TROUBLESHOOTING GUIDE
Symptom
Possible Cause(s)
Corrective Action
Blade cuts crooked
Cut advancing too fast
Decrease the speed of the cut advance, exerting less
cutting pressure. Adjust the braking device.
Worn out blade
Move the blade close to material being cut so that
only the blade section used in the cut is free, This will
prevent deflections that would excessively stress the
blade. Replace the blade.
Wrong tooth pitch
Replace blade choosing the proper tooth pitch to
better match the material being cut.
Broken teeth
The lack of teeth can cause deflection during the
cut; check the blade for broken teeth and replace it if
necessary.
Insufficient lubricating coolant or wrong
emulsion
Check level of coolant in the tank. Check to ensure the
coolant is flowing freely. Check the lubricant viscosity.
In cold situations the coolant may need to be heated
with the optional heater.
Check and user proper lubricant.