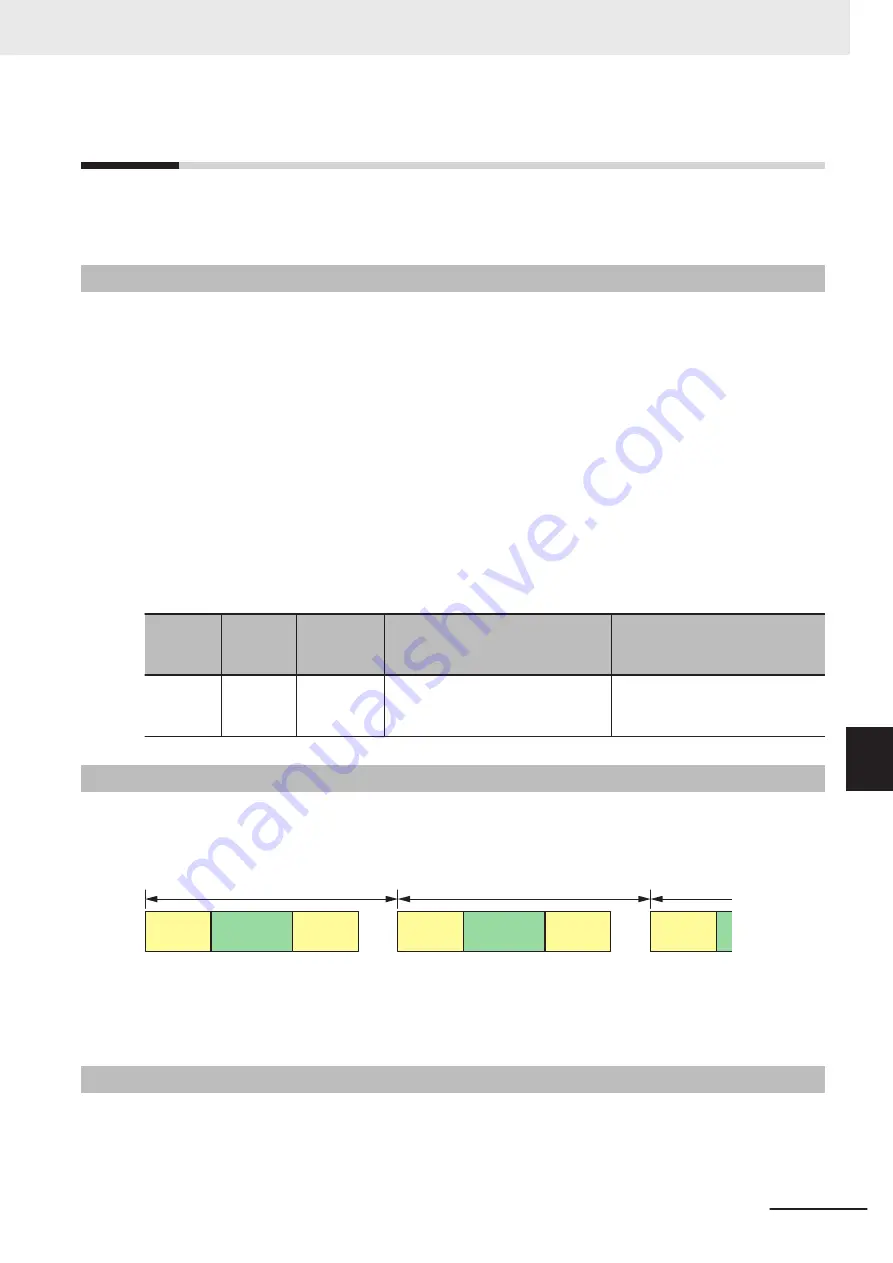
8-2
Safety Task
This section describes the safety task of the Safety CPU Unit.
The safety task period of the Safety CPU Unit affects the safety reaction times.
8-2-1
Safety Task
The safety task is used to assign an execution condition to a series of processes, such as for data
exchange with the Safety I/O Units and safety program execution.
The Safety CPU Unit executes one safety task.
The safety task is executed on a fixed period.
More than one program
*1
can be assigned to a safety task. The programs that are assigned are exe-
cuted in the order that they are assigned. Execution of all of the programs assigned to the task is
called "program execution".
*1. There is no limit to the number of programs.
Data exchange between a Safety CPU Unit and safety slaves, including Safety I/O Units and safety
I/O terminals, or between Safety CPU Units is called "communications receive processing" and
"communications send processing".
Type of
task
Number
of tasks
Task exe-
cution pri-
ority
Execution conditions
Main processing contents
Safety
task
1
None
The safety task is executed once
every safety task period during op-
eration in RUN or DEBUG mode.
Communications receive proc-
essing, program execution, and
communications send processing
8-2-2
Operation of Safety Task
The following operation is performed for the safety task.
Input data processing for I/O refreshing, user program execution, and output data processing for I/O
refreshing are performed repetitively, i.e., each safety task period.
Communications
receive
processing
Program
execution
Communications
send
processing
Safety task period (fixed)
Communications
receive
processing
Program
execution
Communications
receive
processing
Communications
send
processing
Safety task period (fixed)
The safety task period is the time interval at which the safety task is executed. The upper limit of the
safety task period setting is 100 ms. A building error will occur for any safety program that requires a
safety task period that is longer than 100 ms. If that occurs, change the safety program.
8-2-3
Minimum Safety Task Period
This section describes how to find the minimum safety task period.
8 Calculating Safety Reaction Times
8 - 5
NX-series Safety Control Unit User's Manual (Z930)
8-2 Safety T
ask
8
8-2-1
Safety T
ask
Содержание NX-SIH400
Страница 4: ...Introduction 2 NX series Safety Control Unit User s Manual Z930 ...
Страница 46: ...Revision History 44 NX series Safety Control Unit User s Manual Z930 ...
Страница 108: ...2 Specifications 2 42 NX series Safety Control Unit User s Manual Z930 ...
Страница 132: ...3 Installation and Wiring 3 24 NX series Safety Control Unit User s Manual Z930 ...
Страница 148: ...4 Safety Control Unit Operation 4 16 NX series Safety Control Unit User s Manual Z930 ...
Страница 216: ...5 System Configuration and Setup 5 44 NX series Safety Control Unit User s Manual Z930 ...
Страница 306: ...6 Programming 6 90 NX series Safety Control Unit User s Manual Z930 ...
Страница 378: ...7 Checking Operation and Actual Operation 7 72 NX series Safety Control Unit User s Manual Z930 ...
Страница 390: ...8 Calculating Safety Reaction Times 8 12 NX series Safety Control Unit User s Manual Z930 ...
Страница 412: ...11 Safety Data Logging 11 10 NX series Safety Control Unit User s Manual Z930 ...
Страница 504: ...12 Troubleshooting 12 92 NX series Safety Control Unit User s Manual Z930 ...
Страница 550: ...l Safety I O Terminal Settings l I O Map Settings Appendices A 38 NX series Safety Control Unit User s Manual Z930 ...
Страница 554: ...l I O Map Settings Appendices A 42 NX series Safety Control Unit User s Manual Z930 ...
Страница 558: ...l Safety I O Terminal Settings l I O Map Settings Appendices A 46 NX series Safety Control Unit User s Manual Z930 ...
Страница 564: ...l Safety I O Terminal Settings l I O Map Settings Appendices A 52 NX series Safety Control Unit User s Manual Z930 ...
Страница 623: ...I Index I 1 NX series Safety Control Unit User s Manual Z930 I ...
Страница 625: ......