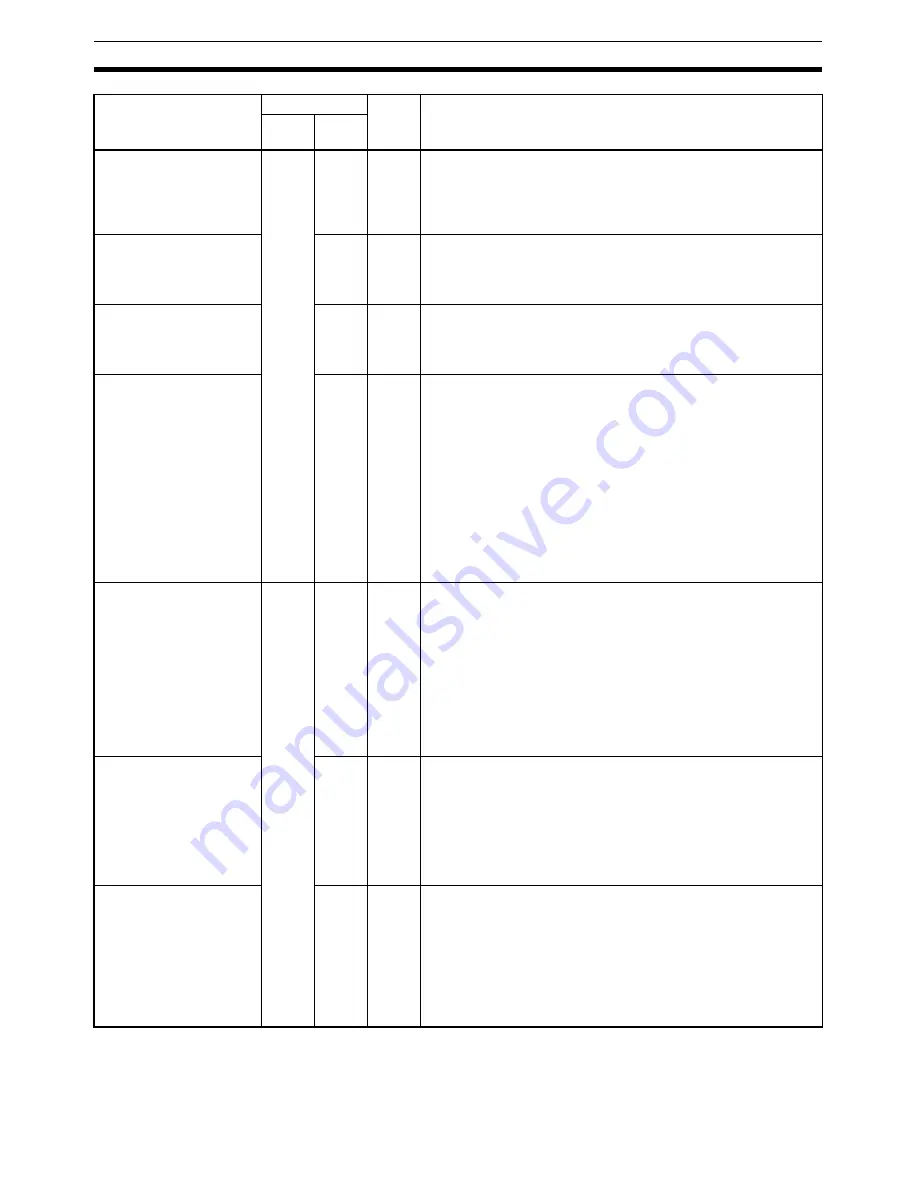
112
Error Codes
Section 15-2
Axis classification error
037Ah
-
0399h
3015h
3015h
Attempted to execute a command that cannot be executed as an
axis. (The command that requires an external signal (MOVEI, etc.)
was executed on the virtual axis, or the winding axis of
MOVETRAV is not set as an unlimited length axis, etc.)
Correct the applicable parameters or program.
No origin proximity signal
3016h
3016h
During an origin search in the limit reversal mode, there was no
deceleration limit switch in between over travel of both directions.
Provide the origin proximity limit switch, or check if the limit
switches themselves or wiring is normal.
Origin proximity and over
travel simultaneously ON
3017h
3017h
During an origin search, the deceleration limit switch and the over
travel in direction of the search were turned ON simultaneously.
Check if the origin proximity signal, or over travel signals for both
directions are wired correctly.
No origin signal
3018h
3018h
During an origin search, the over travel signal turned ON while
waiting for the origin signal (while waiting for the rise of phase-Z
after the fall (ON to OFF) of the origin proximity limit switch).
Check if the settings of the axis parameter [P4AA06: Origin deter-
mine signal] and the servo parameter [Pn511: Input signal select
5] are correct (if the applicable signal is enabled).
If the settings are correct, check the followings:
• Problem on Phase-Z of the encoder
• Breakage of encoder cable
• Too small distance between the origin proximity limit switch and
the limit switch
These causes are to be removed.
Excessive speed com-
mand
037Ah
-
0399h
3019h
3019h
The axis speed has exceeded maximum rapid feed rate during the
following command execution:
• MOVEL (Axes except for the one with the longest travel distance)
• MOVEC (Linear axis: if not specified with the tangential speed of
the circular interpolation portion.)
• MOVETRAV (Traverse axis)
• CAM
Check if the speed set in [P2AA01: Maximum rapid feed rate] is
correct. If it is not correct, set a higher speed. If it is correct, lower
the feed rate of the program or lower the speed using override.
Counter latch resource
violation
301Ah
301Ah
With DATUM, MOVEI, MOVELINK, CAMBOX, SYNC, and LATCH
commands, attempted to execute the functions simultaneously
that require the counter latch.
Check the axis specified for the Latch and correct the program so
that there are no redundant specifications (executing LATCH com-
mand on the axis already executing LATCH command, executing
LATCH command on the axis waiting for the synchronization start
conditions to be satisfied, or etc.).
Gear ratio range error
3040h
3040h
Relations between the No. of encoder pulses and command unit is
not normal. When the following expression is not satisfied, the
error will occur:
1/7FFFFFFFh
≤
B/A
≤
7FFFFFFFh
Note
B = No. of encoder pulses
×
P5AA05
A = P5AA04
×
P5AA06
B/A is integer calculation and the result is to be reduced.
Set the parameters so that the formula above is satisfied.
Name
Error log
Alarm
code
Cause and remedy
Error
code
Detail
code
Содержание CX-MOTION - 06-2008
Страница 1: ...CX Motion MCH Cat No W448 E1 04 OPERATION MANUAL...
Страница 2: ...CXONE AL C V3 CXONE AL D V3 CX Motion MCH Operation Manual Revised June 2008...
Страница 3: ...iv...
Страница 5: ...vi...
Страница 9: ...x TABLE OF CONTENTS...
Страница 15: ...xvi Note All new functions can be used in Motion Control Units with unit version 3 0 or later...
Страница 31: ...12 Connecting to a PLC Section 2 2...
Страница 47: ...28 Operations Listed by Purpose Section 3 2...
Страница 71: ...52 Exporting File Section 6 4...
Страница 91: ...72 Debugging the Program Section 9 3...
Страница 95: ...76 Data Traces Section 10 1...
Страница 99: ...80 Verifying Backup File with MC Unit Section 11 3...
Страница 106: ...87 SECTION 13 Printing This section describes the operations used to print project data 13 1 Printing 88...
Страница 109: ...90 Printing Section 13 1...
Страница 133: ...114 Error Codes Section 15 2...