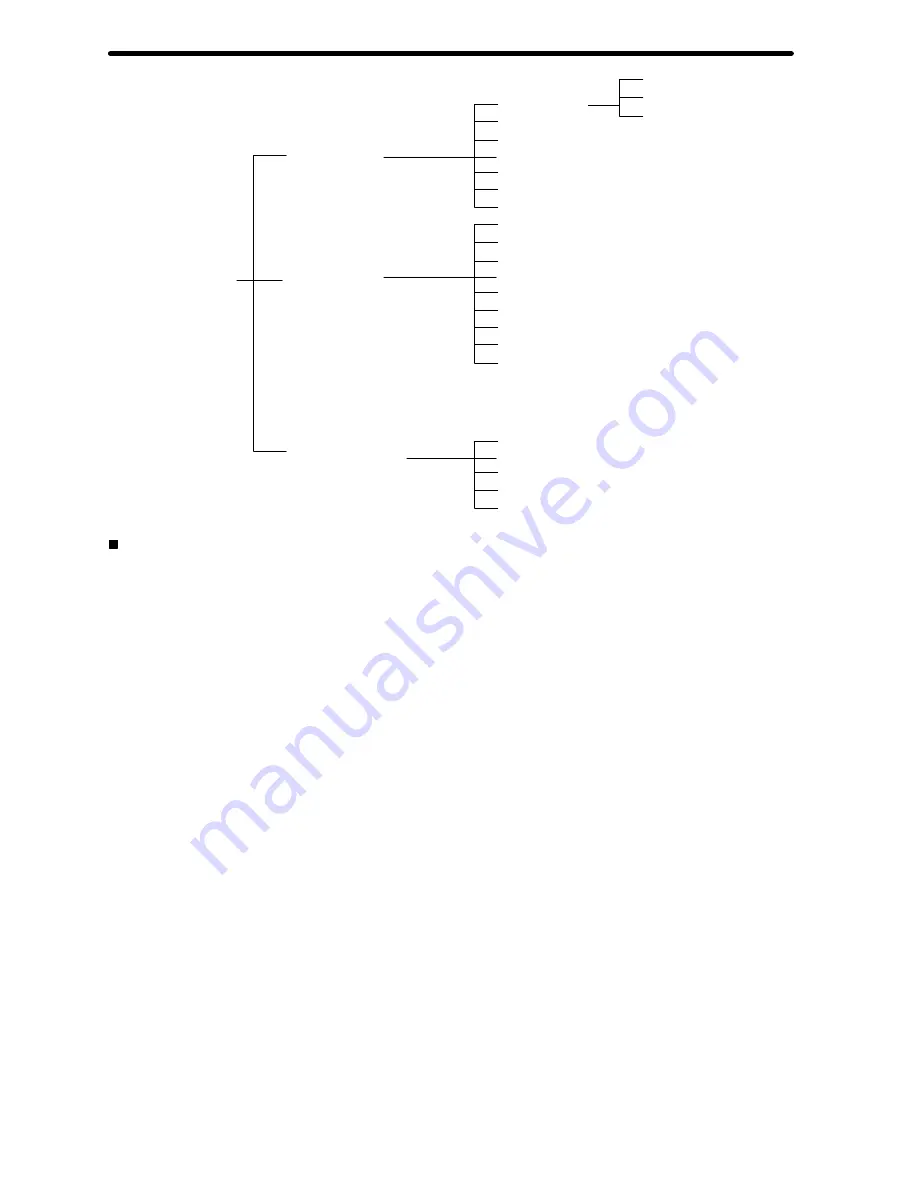
Motion Control Units
Product Specifications
2
MC Unit functions
Automatic Mode
(Executes G-language programs
in the MC Unit.)
Manual Mode
(Executes manual commands
from the CPU Unit or Teaching
Box.)
Common to Automatic
and Manual Modes
Position control
Speed control
Origin search
Interrupt feeding
Traversing
Arithmetic operations, etc.
Deceleration stop
Origin search (manual)
Standard origin return
Jogging
Error counter reset
Forced origin
Absolute origin setting
Servo lock/Servo unlock
Teaching
Zones
Backlash correction
Override
Present position preset
Electronic gear
Dwell timer
Stop Mode
Pass Mode
In-position
Check OFF Mode
Features
Multitasking G Language
The MC Unit is provided with a multitasking G language, which is the
optimum language for motion control. The G language makes it sim-
ple to create programs for multiaxis control, without placing a bur-
den on the CPU Unit’s ladder diagram program.
Simple and Fast Traverse Operations
Commands for 2-axis traverse operations enable simple and fast
traverse operations.
Fast Pick-and-place Operations
After a positioning command has been output, the in-position check
OFF function allows the next positioning operation to be started
without waiting for the first positioning operation to be completed.
This makes it possible to perform high-speed pick-and-place opera-
tions.
Supports Absolute Encoders
The MC Unit is compatible with absolute encoders as a standard
feature, eliminating the need to perform an origin search. Incremen-
tal encoders can be used as well.
High-speed Response to Start Commands from CPU Unit
The response time from when a start command is received from the
CPU Unit until the command voltage is output from the MC Unit is 8
ms for two axes and 13 ms for four axes (MC421 only). This is 1.5
times faster than the previous models.
Note:
Two-axis MC Unit
This function applies to the X axis when a 2-axis, 1-task
configuration is used.
Four-axis MC Unit
This function applies to the X axis when a 4-axis, 1-task
configuration is used.
500-kp/s Encoder Response Frequency
The maximum feedback encoder response frequency is 500 kp/s,
so the MC Unit can be used with high-speed and high-precision ser-
vomotors. This is double the response frequency of the earlier mod-
els.
CPU Unit Interrupts
A CPU Unit external interrupt task can be started by outputting a D
code (interrupt code) for the CPU Unit when positioning is com-
pleted or when passing through a particular position. This feature is
ideal for high-speed synchronization between the MC Unit and CPU
Unit.
Other Functions
•
Unlimited Feeding
This function executes unlimited feeding for the specified axis.
Use of this function allows the user to control unlimitedly fed
axes, such as those for turntables or one-way conveyors. The
present value can be increased or decreased within the
specified range.
•
Synchronous Electronic Gear
Input pulses for a synchronous encoder can be accelerated or
decelerated for each axis at any timing. The acceleration or
deceleration rate is specified by a numerator/denominator ratio.
To provide simple synchronous control, this function can also be
enabled or disabled for each axis at any timing.
•
Error Counter Reset
After a deceleration command has been completed, the error
counter reset function forcibly sets the error counter to 0 to stop
the axis operation completely. This function is best suited for
machine press control in molding and other processes.
•
Multiturn Circular Interpolation
The multiturn circular interpolation function has been added to
the existing circular and helical circular interpolation functions.
This function can be used for applications such as winding
machine operations.
•
Override (Real Time Speed Change)
The speed can be changed during PTP, linear interpolation, or
circular interpolation operations in which the axis stops during
the positioning operation. (This function is invalid in pass mode
or in-position check OFF mode.)
•
Pass Operations
The acceleration and deceleration times can be changed during
pass operations. It is possible to specify whether to pass the
operation using the previous acceleration time or pass the
operation using the deceleration time during pass operations. It
is also possible to pass the operation at a constant acceleration
rate during single-axis pass operation.