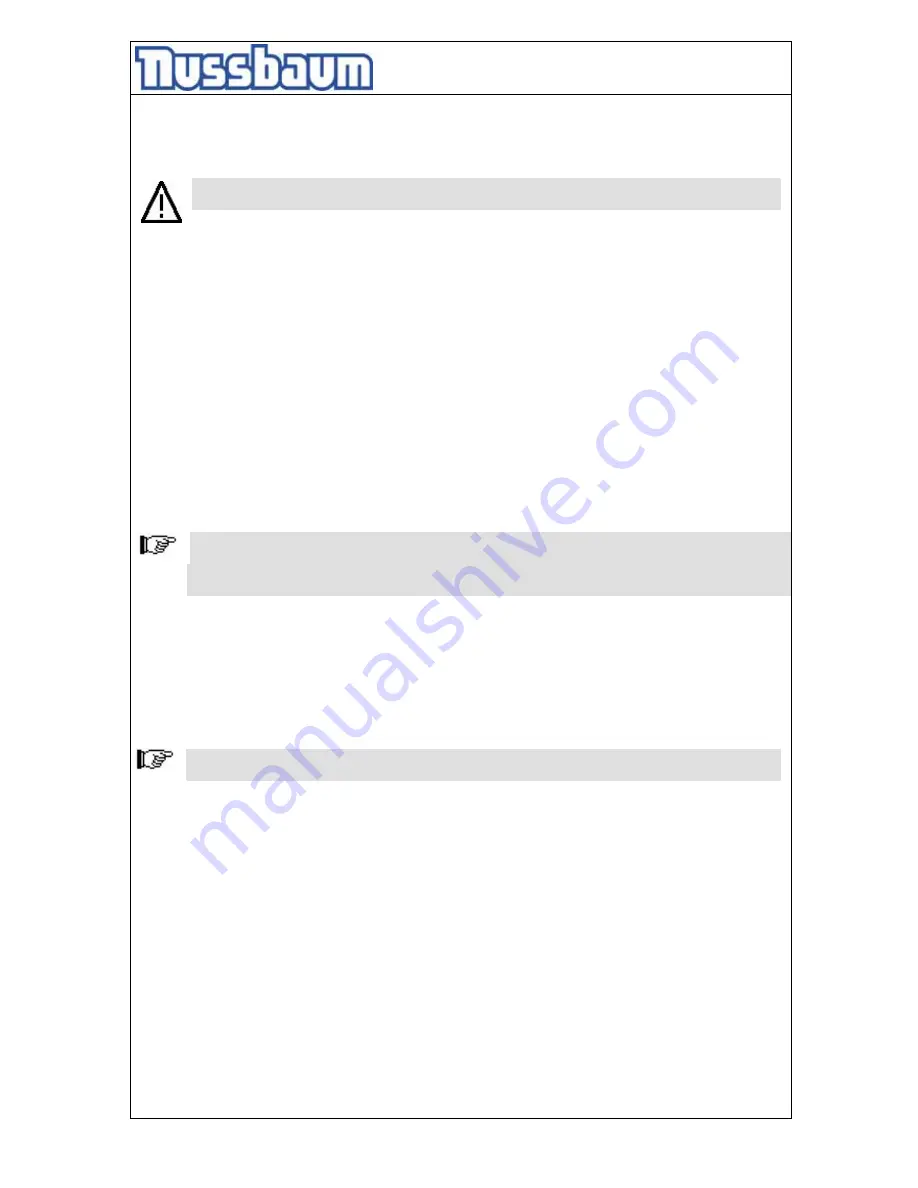
Operating instruction and documentation
HL 2.30 NT/ HL 2.40 NT
- 32 -
6.1 Emergency lowering
It is possible to lower the vehicle into the lowest position with a simply operation.
The emergency lowering must only carried out by persons which are instructed to
using the lift. Please refer to the regulation “Lowering the vehicle”.
Procedure – emergency lowering
• No persons in the danger area must be kept clear to the lift.
• Pull slowly the operating lever. The lowering procedure startet immediately. The lowering
speed is infinitely variable.
• Please observe the complete lowering procedure. In case of danger let off the lever.
• Lower the lift into the lowest position. Remove the arms and drive the vehicle out of the lift
• If necessary call your service partner.
• Use only the lift if it is in a perfect condition.
6.2 Lowering onto an obstacle
If the lifting carriage or a lifting arm is lowered onto an obstacle, the lift stops the lowering
movement. To remove the obstacle, push the operating lever to raise the lift.
7. Inspection and Maintenance
Before conducting maintenance work, preparations must be made to ensure that during
maintenance and repair work there is no risk to the safety of people working
on or around the lift and also that there is no risk of damage to equipment being used on
or around the lift.
To guarantee the utmost availability and to ensure that the lift remains functional, maintenance
work contracts are organised between our clients and their local retailers.
A service must be performed at regular intervals of 3 months through the operator in accordance
with following service manual. If the lift is in continuous operation or in a dirty environment, the
maintenance rate must be increased.
During daily operation the lift must be closely observed to ensure that it is functioning correctly. In
the case of malfunction or leakage the technical service must be informed.
German legal guidelines : BSV (Prescription of working tools) + BGR500 (Work with
working tools)
Содержание HL 2.30 NT
Страница 10: ...Operating instruction and documentation HL 2 30 NT HL 2 40 NT 10 2 5 Declaration of conformity ...
Страница 13: ...Operating instruction and documentation HL 2 30 NT HL 2 40 NT 13 3 3 Data sheet HL 2 30 NT ...
Страница 14: ...Operating instruction and documentation HL 2 30 NT HL 2 40 NT 14 ...
Страница 15: ...Operating instruction and documentation HL 2 30 NT HL 2 40 NT 15 ...
Страница 16: ...Operating instruction and documentation HL 2 30 NT HL 2 40 NT 16 3 4 Data sheet HL 2 40 NT ...
Страница 17: ...Operating instruction and documentation HL 2 30 NT HL 2 40 NT 17 ...
Страница 18: ...Operating instruction and documentation HL 2 30 NT HL 2 40 NT 18 3 5 Foundation plan ...
Страница 19: ...Operating instruction and documentation HL 2 30 NT HL 2 40 NT 19 ...
Страница 22: ...Operating instruction and documentation HL 2 30 NT HL 2 40 NT 22 3 7 Electrical diagram ...
Страница 23: ...Operating instruction and documentation HL 2 30 NT HL 2 40 NT 23 ...
Страница 24: ...Operating instruction and documentation HL 2 30 NT HL 2 40 NT 24 ...
Страница 25: ...Operating instruction and documentation HL 2 30 NT HL 2 40 NT 25 ...
Страница 26: ...Operating instruction and documentation HL 2 30 NT HL 2 40 NT 26 ...