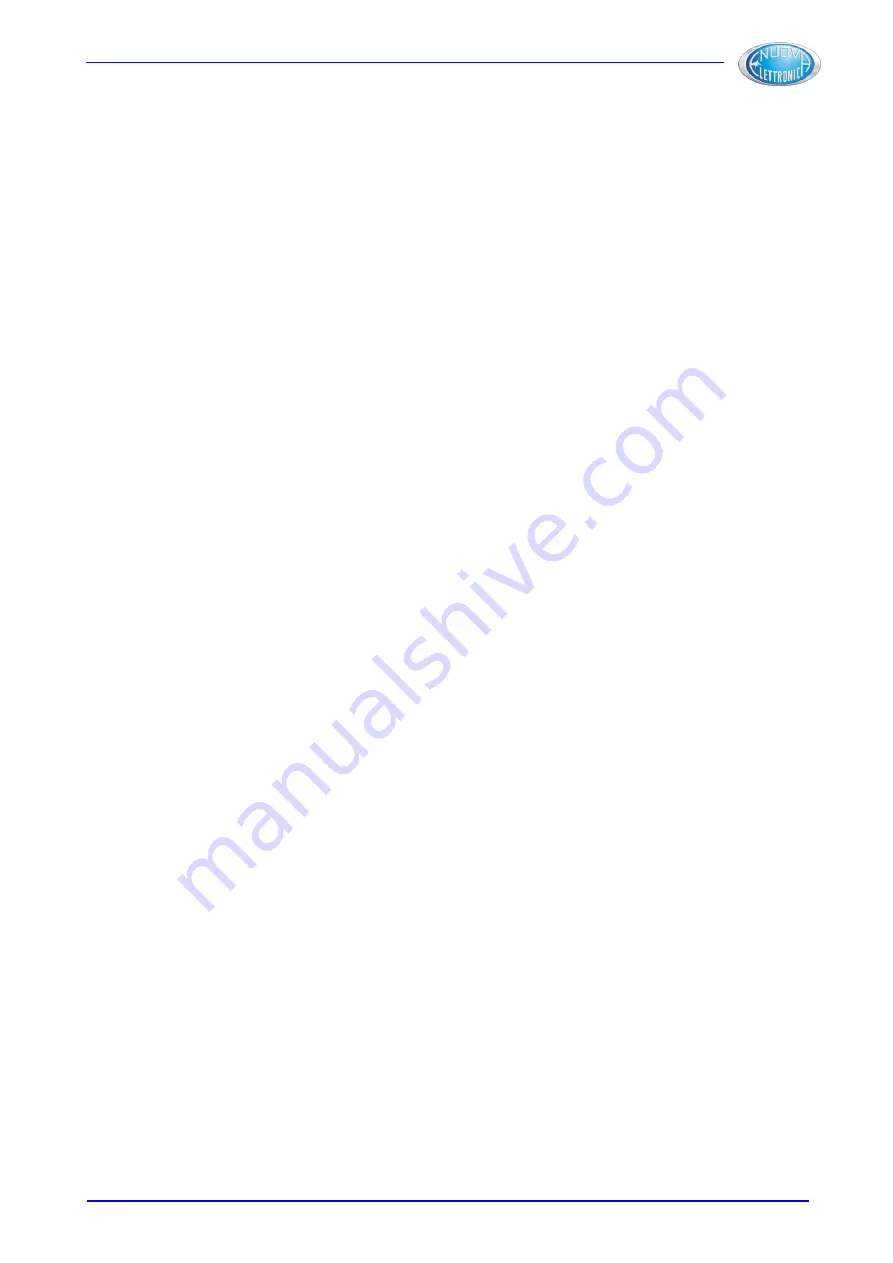
DSP
LASER
DSPLSR01EN
25
10.1.4. Check of overtravel or stop space
The overtravel of the press-brake, or stop space, must be at most 18 mm, depending on the
models in paragraph 9.
A greater value does not ensure the operator safety.
The rule design EN 12622:2014 specifies the requirements to adopt to check the overtravel
of the machine, in other words its stop space, in case of an emergency stop.
The DSP LASER device has been designed and manufactured in compliance with the
required requirements.
The control function must be activated each time the press-brake is switched on and,
however, after 30 hours of continue work.
The DSP LASER device can be equipped with a control circuit which, if interfaced with
proper position detectors installed on the press-brake (mechanical or electronic
overtravels), can execute this function of automatic monitoring of the overtravel in
compliance with what foreseen by the rule.
A cam with size equivalent to the maximum stop space (S.A.) of the machine must be
applied to the mobile table. A size greater than 1 mm is allowed, as tolerance, to make the
operation stable but not dangerous. Two limit-switches must be, instead, applied to the fixed
part at such a distance to ensure that the press-brake can reach the maximum downstroke
speed within this space. The cam must operate on the actuator of a limitswitch (PMSM),
whose N.A. contact determines the Maximum Top Dead Centre and, then, during the
downstroke, on the actuator of a second limitswitch (VSA), whose N.C. contact, opening,
determines the switching to state OFF of the OSSD outputs which, on their own, via the
actuation circuits of the machine, stop the movement of the upper tool checking its stop
space. The limit-switches can be both mechanic and inductive (electronic proximity
switches). The cam size must consider the actuation and release strokes of the limitswitch
VSA.
On the front side of the receiver, some LEDs are present signalling, during the check of the
stop space, the state of the signals necessary to achieve this control. Their state, once the
check has been made, points out the success or, in case of failure, which signal and, then,
action, has not properly occurred.
After each switch-on of the machine, then of the safety device, the check of the stop space
is required.
It is necessary to move the mobile table to PMSM and command the high-speed closing
keeping for the whole stroke, otherwise the check cannot be passed.
The check starts has soon as the limitswitch PMSM is triggered by the cam, which causes
its contact closes.
After this action, the high-speed closing of the machine must be executed.
If the procedure is not properly executed (for example the downstroke takes place at
reduced speed or, even at high speed, it is interrupted before reaching the limitswitch VSA,
or the cam reaching VSA and then causing the stop of the downstroke of the machine, but
the cam goes over VSA when the movement is ended, closing again its contact), the control
circuit of the device considers the check NOT passed and DSP LASER sets its output in
permanent OFF not allowing any high-speed downstroke.
Instead, if the cam, when the movement is ended, continues to engage the limitswitch VSA,
this means the machine has stopped within its typical stop space.
The stop circuit of the machine answers again with its initial project and test performances.
The check, in this case, is passed and the outputs of DSP LASER return to state ON
allowing the normal operation of the machine.
The machine can operate at most for 30 consecutive hours. Once elapsed this time, the
device sets its OSSD outputs to the permanent OFF state.
Only switching-off and, then, switching-on the machine the initial switch-on condition of DSP
LASER is restored, which obliges the operator to execute the check of the stop space.
Содержание DSP LASER
Страница 2: ......
Страница 4: ......
Страница 48: ...DSP LASER 44 DSPLSR01EN CONNECTION SCHEMES Fig 13 6 scheme of connection with AL1B...
Страница 49: ...DSP LASER DSPLSR01EN 45 Fig 13 7 scheme of connection with AL2B...
Страница 50: ...DSP LASER 46 DSPLSR01EN Fig 13 8 scheme of connection with ALdc...
Страница 51: ...DSP LASER DSPLSR01EN 47 Fig 13 9 scheme of connection without AL module...