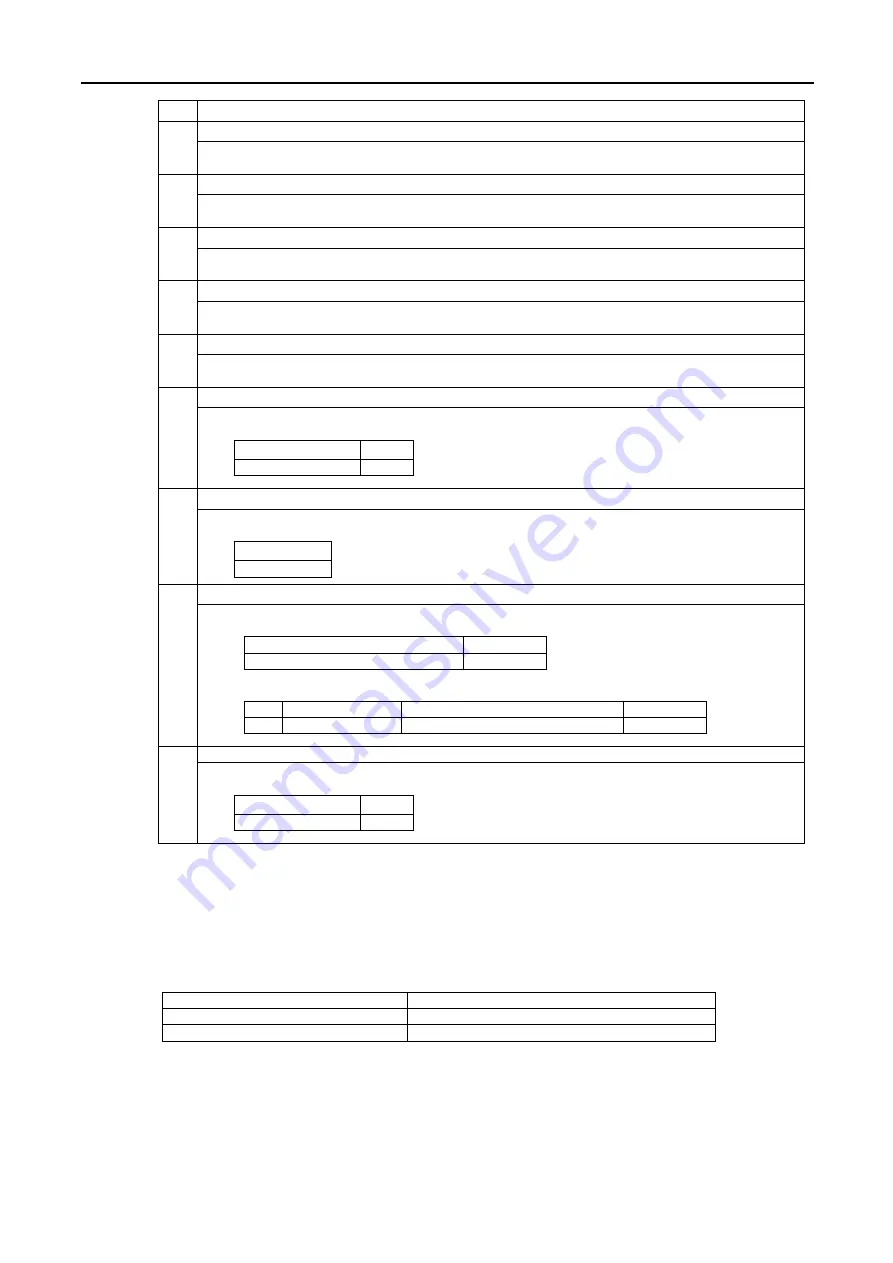
5.Operation
Analog monitor, digital monitor
5-22
ID
Contents
1F
Position Loop Integral Time Constant monitor [TPI MON]
■
Displays actual Position Loop Integral Time Constant value.
Value can be confirmed when changing the gain function.
20
Velocity Loop Proportional Gain monitor [KVP MON]
■
Displays actual Velocity Loop Proportional Gain.
Value can be confirmed when changing gain and at Auto-tuning function.
21
Velocity Loop Integral Time Constant monitor [TVI MON]
■
Displays actual Velocity Loop Integral Time Constant.
Value can be confirmed when changing gain and at Auto-tuning function.
22
Torque Command Filter monitor [TCFIL MON]
■
Displays actual Torque Command Filter.
Value can be confirmed when changing gain and at Auto-tuning function.
23
Model Control Gain monitor [MKP MON]
■
Displays actual Model Control Gain.
Value can be confirmed when changing gain and at Auto-tuning function.
24
Load Torque monitor (Estimate value) [MTLMON-EST]
■
Displays estimated value of load torque.
Display range
Unit
-499.9 to 499.9
%
25
Driver operation time [OPE-TIM]
■
Is counted during period control power is being turned on. The time is displayed value x 2 hours.
Unit
×2 hour
26
Acceleration monitor [ACCMON]
■
Indicates motor acceleration.
◆
Setup software displays values in decimal notation.
Display range
Unit
-2147483648 to 2147483647
rad/s
2
◆
Digital operator displays values in hexadecimal notation.
ID
Data range
Display range
Unit
26
Bit31 to Bit0
H.FFFF L.FFFF to H.0000 L.0000
rad/s
2
80
RESANG
■
Resolver sensor electric angle. [RESANG]
Reports Resolver sensor electric angle.
Data range
unit
0 to 65535
pulse
5.6
Analog monitor and digital monitor
All signals and internal status of the driver can be monitored. Analog monitor output 1 is also output
from
“
CN1-pin30
”
.
■
Selection of output signal
Select and change the output signal to be used from the parameters list below.
General parameters GroupA ID10
DMON: Digital Monitor Output Signal Selection
General parameters GroupA ID11
MON1: Analog Monitor Select Output 1
General parameters GroupA ID12
MON2: Analog Monitor Select Output 2
Содержание M-EGA-15A2301
Страница 149: ...No Text on This Page ...
Страница 237: ......