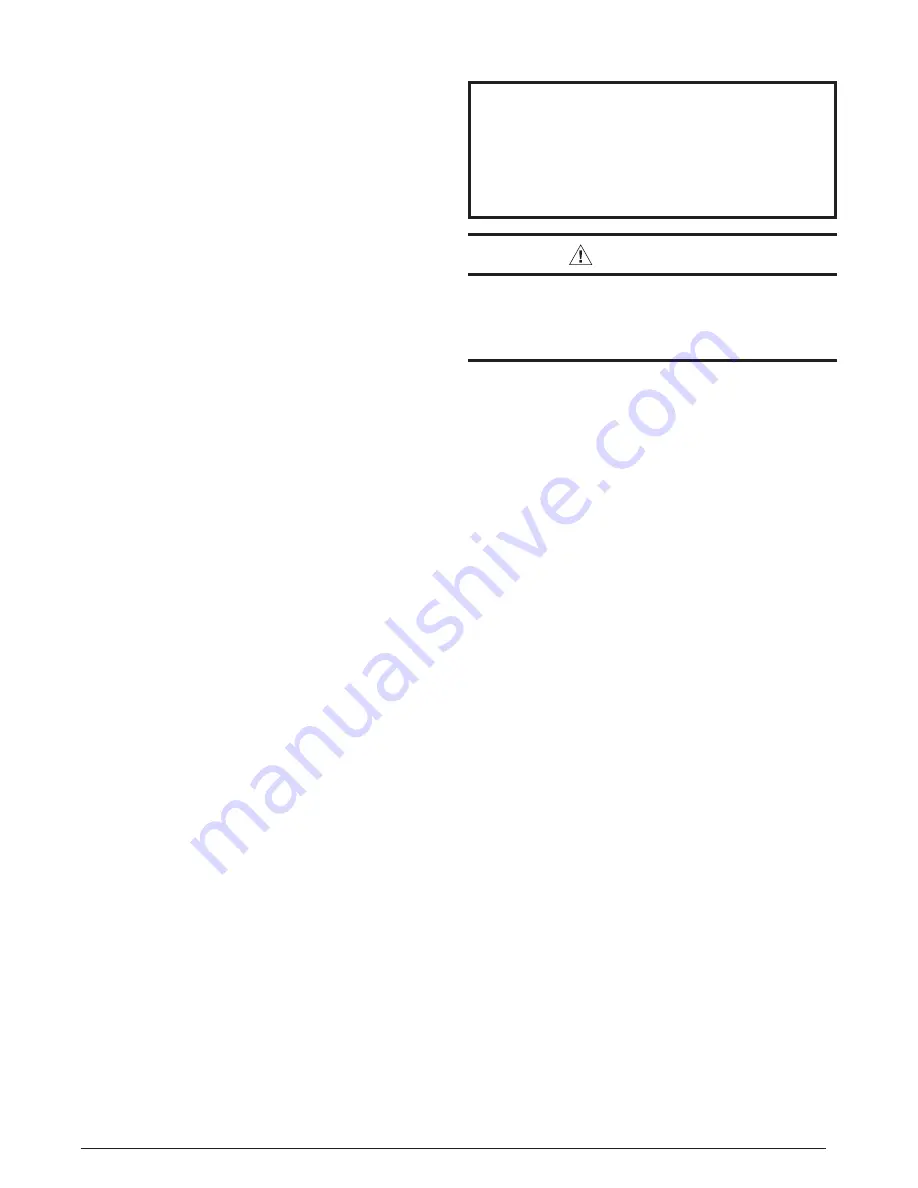
23
START-UP & ADJUSTMENTS
Pre-Start Check List
√
Verify the polarity of the connections are correct, the
line voltage power leads are securely connected and
the furnace is properly grounded.
√
Verify the thermostat wires (
R
,
W
,
Y
, &
G
) are securely
connected to the correct leads on the terminal strip of
the circuit board.
√
Verify the gas line service pressure does not exceed
10.0 inches of W.C., and is not less than 4.5 inches W.C.
for natural gas. For LP gas the line service pressure
must not exceed 14 in. W.C., and must not be less than
11.0 in. W.C.
√
Verify the roll-out and vent switches are closed. If
necessary, press the red button to reset a switch.
DO
NOT install a jumper wire across a switch to defeat
its function.
If a switch reopens on startup, DO NOT
reset the switch without identifying and correcting the
fault condition.
√
Verify the blower door is in place, closing the door
switch in the line voltage circuit.
√
Verify the gas line has been purged and all connections
are leak free.
Start-up Procedures
Do not perform these steps until all of the checks in the
previous steps have been completed:
1. Set the thermostat to the lowest setting.
2. Turn off all electrical power to the furnace.
3. Follow the Operating Instructions on the label attached
to the furnace.
4. Set the thermostat above room temperature and verify
the Operating Sequence (page 25).
5. After 5 minutes of operation, set the thermostat below
room temperature and verify steps 9 - 10 of the Operating
Sequence.
Verifying & Adjusting Input Rate
The input rate must be verified for each installation to
prevent over-firing of the furnace.
NOTE:
The input rate
must not exceed the rate shown on the furnace rating plate.
At altitudes above 2,000 feet, it must not exceed that on
the rating plate less 4% for each 1,000 feet. To determine
the exact input rate, perform the following procedures:
1. Shut off all other gas fired appliances.
2. Start the furnace and run it for at least 3 minutes.
3. Measure the time (in seconds) required for the gas
meter to complete one revolution.
4. Convert the time per revolution to cubic feet of gas per
hour using Table 7 (page 30).
5. Multiply the gas flow rate in cubic ft per hr by the heating
value of the gas in Btu per cubic ft to obtain the input
rate in Btuh. See example.
6. The manifold pressure must be set to the appropriate
value for each installation by a qualified installer, service
agency or the gas supplier.
WARNING:
Do not attempt to drill the gas orifices. Use only
factory supplied orifices. Improperly drilled
orifices may cause fire, explosion, carbon
monoxide poisoning, personal injury or death.
a.) Obtain the manifold pressure setting required for
this installation by referring to Table 11 for Propane
or Table 12 (page 31) for Natural Gas.
b.) Remove the regulator capscrew from the INLET
side of the regulator. See Figure 30, page 30 - gas
valve picture in LP section.
c.) Slowly turn the adjustment screw inside the regulator
to obtain the appropriate manifold pressure.
NOTE: Turning the screw clockwise increases the
pressure and turning the screw counter-clockwise
decreases the pressure. To prevent backing the
screw all the way out from the valve, turn the screw
slowly.
d.) Replace and tighten the regulator capscrew over
the adjustment screw.
Verifying & Adjusting Temperature Rise
After installation of the furnace, confirm the temperature
rise of the furnace is within the limits specified on the rating
plate. Any temperature rise outside the specified limits
could result in premature failure of the heat exchanger.
For typical duct systems, the temperature rise will fall
within the limits specified on the rating plate with the
blower speed at the factory recommended setting. If the
measured temperature rise is outside the specified limits,
it may be necessary to change the speed of the blower.
NOTE:
Lowering the blower speed will increase the
temperature rise and a higher blower speed will decrease
the temperature rise.
The furnace is equipped with a multi-speed motor. Heating
and cooling speed selection is made by moving the switch
on the integrated control located in the furnace.
1. Place thermometers in the return and supply air stream
as close to the furnace as possible.
IMPORTANT: The
thermometer on the supply air side must be shielded
from direct radiation from the heat exchanger to
avoid false readings.
2. Consult Table 5 (page 24) and the rating plate for
the proper circulating air flow and temperature rise.
Example
:
• Time for 1 revolution of a gas meter with a 1 cubic
ft dial = 40 seconds.
• From Table 7 read 90 cubic ft gas per hr.
• Local heating value of the gas (obtained from gas
supplier) = 1,040 Btu per cubic ft.
• Input rate = 1,040 x 90 = 93,600 Btuh.