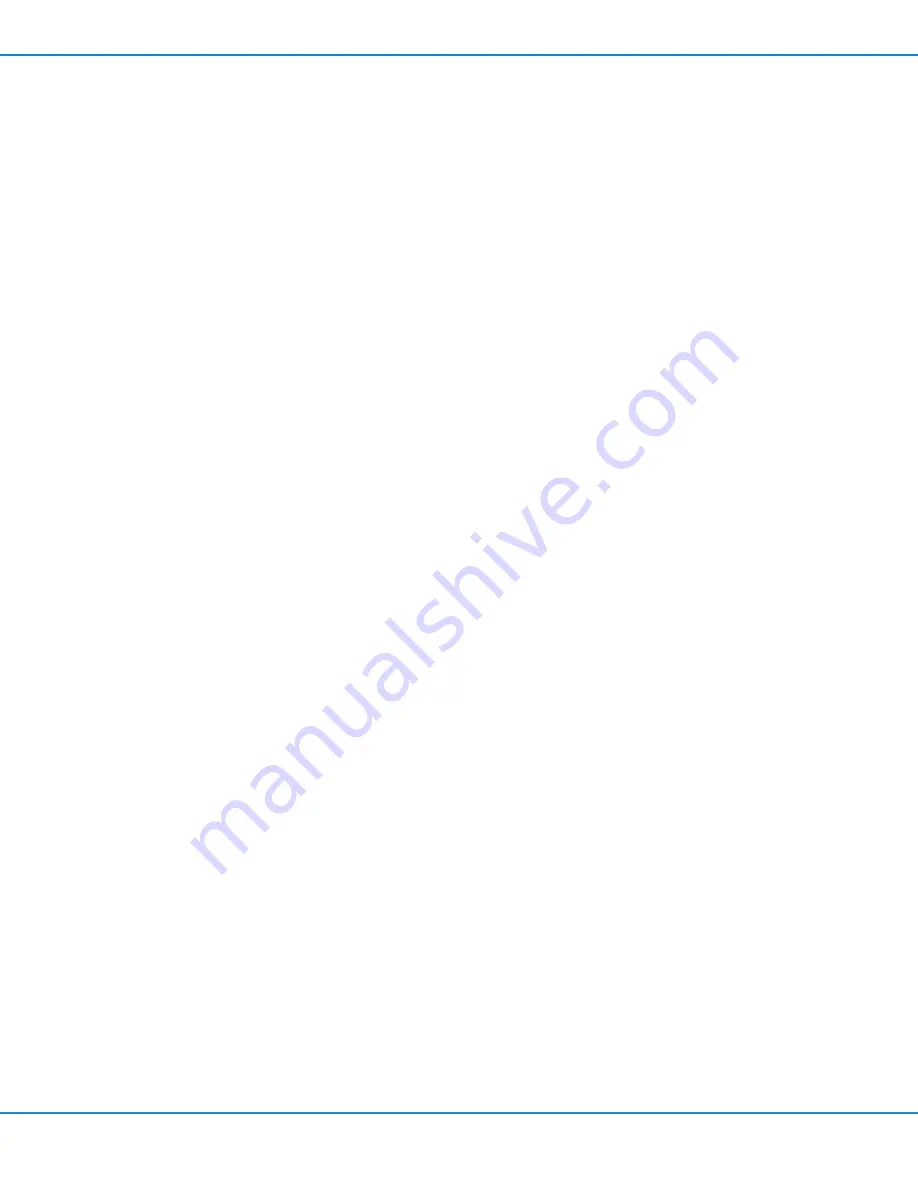
Data Communication via CAN Bus
In addition to being triggered manually or via binary input signals IN1 to IN10, dispensing sequences (output signals)
can also be controlled by CAN bus communication. The respective setting is located under the Process Data menu
option, Automatic Mode submenu.
The required bus interface is integrated into the PICO controller. Data transmission between the higher-ranking
control unit and a connected PICO controller occurs via a CAN bus according to the master-slave principle: the
primary control unit is the master, while the connected PICO controllers are the slaves.
Each slave (PICO controller) connected to the CAN bus receives its own address. The master (primary control unit)
uses the address to select the slave. The transmission rate used for transmission can be selected by the operator.
The address and the transmission rate must be set for each PICO controller under the System Data menu option.
Value ranges for addresses and transmission rates
(parameter selection, default settings, values after factory reset)
Parameter Value range
Default value and setting after factory reset
CAN address range
0 to 63 Address 63
Possible transmission rates
125 kBit/s
125 kBit/s
250 kBit/s
500 kBit/s
Communication
The standard CAN protocol format (11-bit identifier) as stipulated by the CAN specification 2.0 is used for
communication. The request sent by the master to the slave is responded to as quickly as possible with this
protocol. The time that it takes to receive a response is a factor of the current transmission rate and of the state of
the unit. A typical response time is under 2 ms.
PICO Controller 2+2-XCH-V2
19
www.nordsonefd.com [email protected]
+1-401-431-7000 Sales and service of Nordson EFD dispensing systems are available worldwide.