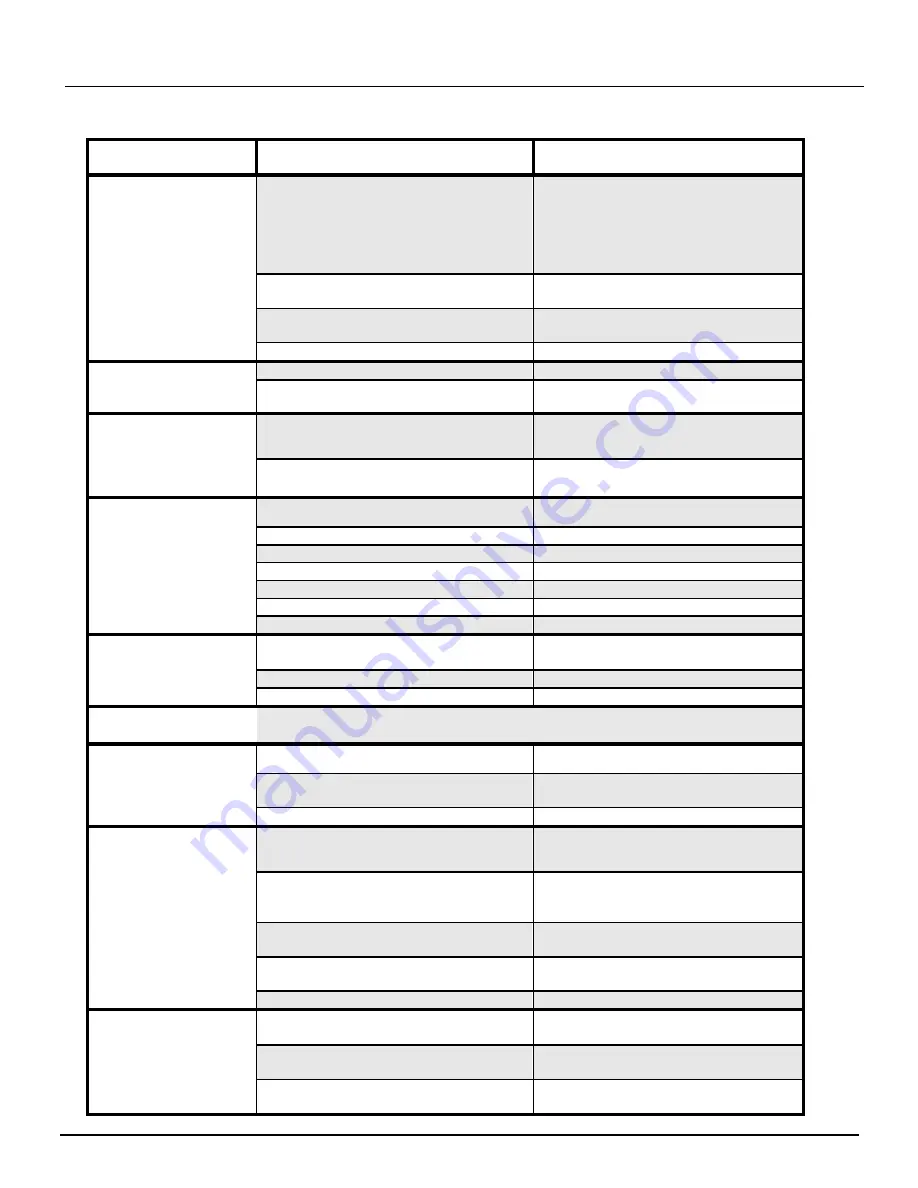
BC 60 "Trailblazer" Brushcutter
TROUBLESHOOTING
AUGUST/2012 (49458202/8203)
Section 4-7
PROBLEM
POSSIBLE CAUSE
SOLUTION
Machine will not
propel.
Main pump not developing pressure.
See Hydraulic Troubleshooting.
Brakes not releasing.
See next problem.
Propulsion relief setting too low.
Increase relief setting.
Defective motor or broken drive shaft.
Repair or replace motor or shaft.
Brakes will not
release
Air Pressure too low.
Adjust regulator setting
Brake cylinder bypassing air.
Inspect and replace cylinder
Brakes will not
apply.
Broken brake spring.
Inspect spring and replace if
necessary.
Brake shoes worn.
Inspect shoes and replace it
necessary.
Boom won't lift or
lower
Lockup engaged.
Disengage lock.
Obstruction at pinch points.
Remove obstruction
Pressure problem at lift cylinder.
Adjust main relief or replace cylinder
Carrier bushings not lubricated.
Grease bushings
Stuck control valve spool
Inspect and repair
Winch motor defective
Inspect, repair or replace.
Boom will not swing
Flow control valves improperly
adjusted
Inspect and adjust as necessary
Piston bypassing
Repair cylinder
Stuck control valve spool
Inspect or repair
Boom Breakaway
Operates too easily
Relief valve setting too low or stuck
open
Inspect and replace as necessary
Cutterhead won't
maintain RPM
Engine not at full RPM
Adjust throttle
System pressure problem
Adjust system pressure
Defective cutterhead motor
Repair or replace motor
Excessive Vibration
in Cutterhead
Unevenly distributed blades or missing
teeth
Replace blades.
Lack of lubrication in the blade shaft
housing
Fill with grease until grease exits other
side of cutterhead housing (blade
side)
Blade cartridge shaft bearing failure
Replace bearing
Defective cutterhead motor
Repair or replace motor
Cracked or damaged blade
Replace blade
Cutterheads will not
rotate
Motor defective
Inspect, repair or replace as
necessary
Relief valve faulty
Inspect, repair or replace as
necessary
Pump Defective
Inspect, repair or replace as
necessary
Содержание Trailblazer BC60
Страница 2: ......
Страница 48: ...BC 60 Trailblazer Brushcutter MAINTENANCE AUGUST 2012 49458202 8203 Section 3 3...
Страница 49: ...MAINTENANCE BC 60 Trailblazer Brushcutter Section 3 4 AUGUST 2012 49458202 8203...
Страница 64: ...BC 60 Trailblazer Brushcutter MAINTENANCE MARCH 2011 49458201 Section 3 21 TORQUE REQUIREMENTS...