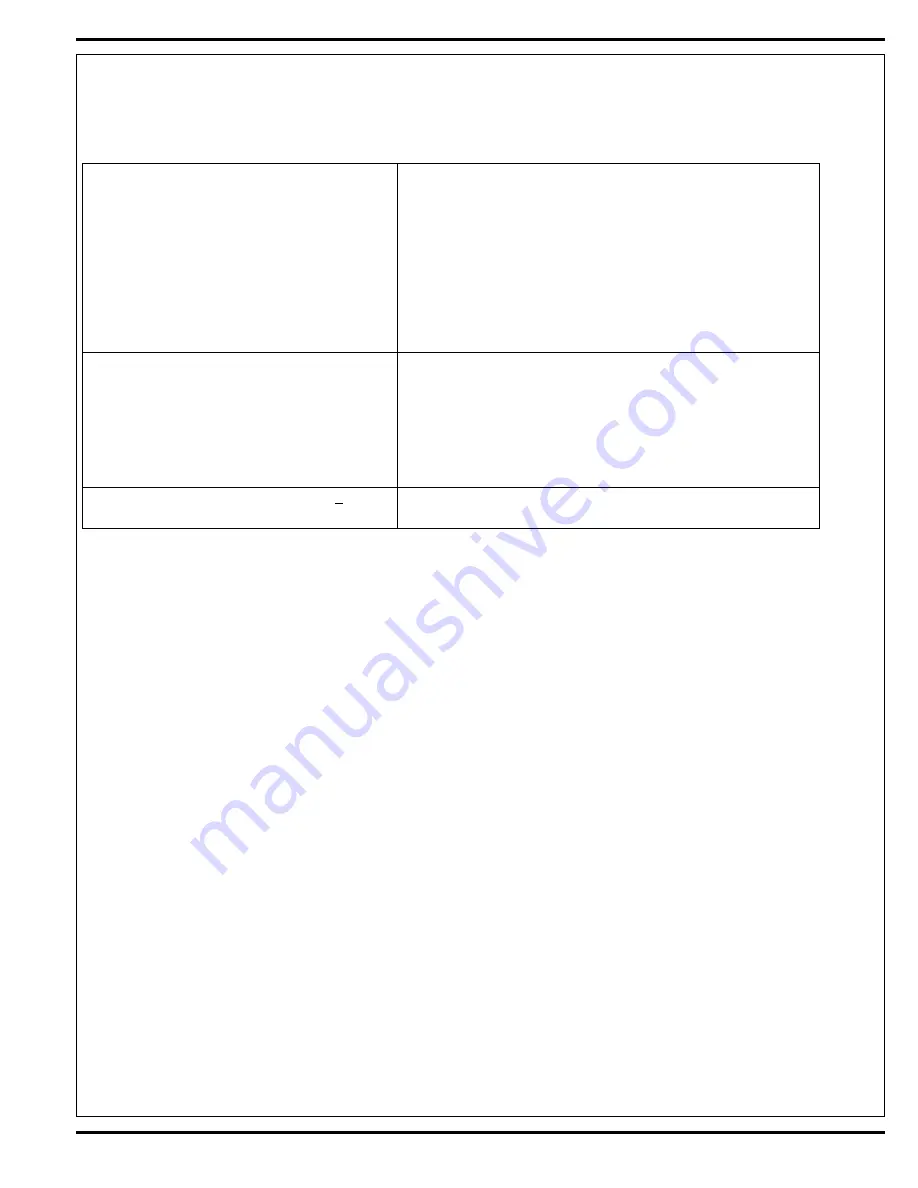
FORM NO. 56043126 - CR 1100, CR 1200 -
25
WHEEL DRIVE SYSTEM
WHEEL DRIVE TROUBLESHOOTING GUIDE
Problem Possible Cause
•
Wheel drive motor will not run in forward and
reverse
• Batteries need charging (low battery voltage, recharge batteries)
• Control Circuit,
(F2)
Circuit Breaker tripped (reset circuit breaker)
• Parking Brake
(OO)
set (release parking brake)
• Emergency Stop Switch
(KK)
tripped (plug in battery connector)
• Seat switch
(S9)
and Battery Interlock switch
(S13)
not closed. Repair or
Replace defective switch.
• Defective Wheel Drive Motor (replace motor) *
• Defective or miss adjusted throttle pot.
(R1)
(replace or adjust throttle
pot) *
• Defective Main Contactor
(K5)
(replace main contactor) *
•
Wheel drive in one direction only, loss of either
forward and reverse
• Test the Fwd & Rev
(R1)
Throttle Pot.
Throttle’s wiring inputs at the
speed control for an open.
Forward 2.5-4.5V(pins 13 & 14)
Reverse .5-2.5V(pins 15 & 14)
Repair wiring or replace the throttle pot
(R1
).
• Controller can’t change electrical polarity to wheel motor replace the
(A3)
speed control. *
•
Speed Controller Fault Code Status Light
(E)
fl
ashes
a fault code.
•
Speed controller has sensed an operation error code fault.
(see the
Status LED Fault Codes (Table 1)
in the Electrical System)
* = See
Curtis Speed Control Troubleshooting
Section.
GENERAL FUNCTIONAL OVERVIEW
A 4 HP separately excited (
fi
eld & armature) 36V DC motor/gear/wheel unit (M15) is used to propel the machine. A Curtis model 1244 PMC solid
state speed controller (A3) regulates (outputs) the variable speed Fwd/Rev wheel drive motor functions. The controller unit is located in the left rear
electrical access panel. The (R1) throttle pot mounted to the operator foot pedal inputs to the (A3) controller. The (A3) Controller operator’s speci
fi
c
speed and direction demands.
DRIVE MOTOR SYSTEM CONTROLLER FUNCTION OVERVIEW
To make the A3 speed controller’s internal circuits operational (power it up) the main power Key Switch S11 must be closed. Next the seat switch
S9 and battery interlock S13 must be closed for the main contactor K5 to be energized. Depressing the foot pedal in either Fwd or Rev will move
the throttle pot R1 out of its neutral position and provide the needed directional and throttle inputs for controller outputs. Depressing the foot pedal
in either Fwd or Rev will move the 5K Ohm (R1) potentiometer shaft off its centered balanced (neutral) setting of approximately 2500 Ohms. With
this pot shaft movement the pot’s resistance value changes which generates a variable voltage signal (0-5 volts). These control board voltage input
signals are what energizes the Fwd & Rev internal directional relays, which selects the motor polarity and what also manages switches the battery
voltage On and Off (*PWM) that varies the motor speed.
MOTOR OPERATION
The motor has (4) terminal connections, (2) armature A1, A2 and (2)
fi
eld F1, F2. The separate motor armature circuit receives from the controller
a chopped on time off time *PWM voltage output that varies the motor speed. The separate
fi
eld circuit sees the current direction polarity change
that effects the rotation of the motor CW for FWD and CCW for REV.
DRIVE WHEEL SYSTEM SPEEDS
The speed controller is programmed for two maximum speed setting modes, M1-max and M2-max. The M1-max is the transport speed mode
and is set at 100% of the total system’s speed potential. The M2-max is the scrubbing speed mode and is set at 80% of the total system’s speed
potential.
Note:
Both of the speed settings (M1 & M2) can be changed (increased or decreased) from the original factory speci
fi
cations only by using the
hand held programmer PN 56409441. See in the electrical system section of this manual, instructions for using the programmer for speed setting
changes and troubleshooting diagnostics.
*PWM; pulse width modulation, also called “chopping” is a technique that switches the battery voltage ON and OFF to the motor very quickly, thereby
controlling the speed of the motor.
Содержание Cr 1100
Страница 72: ......