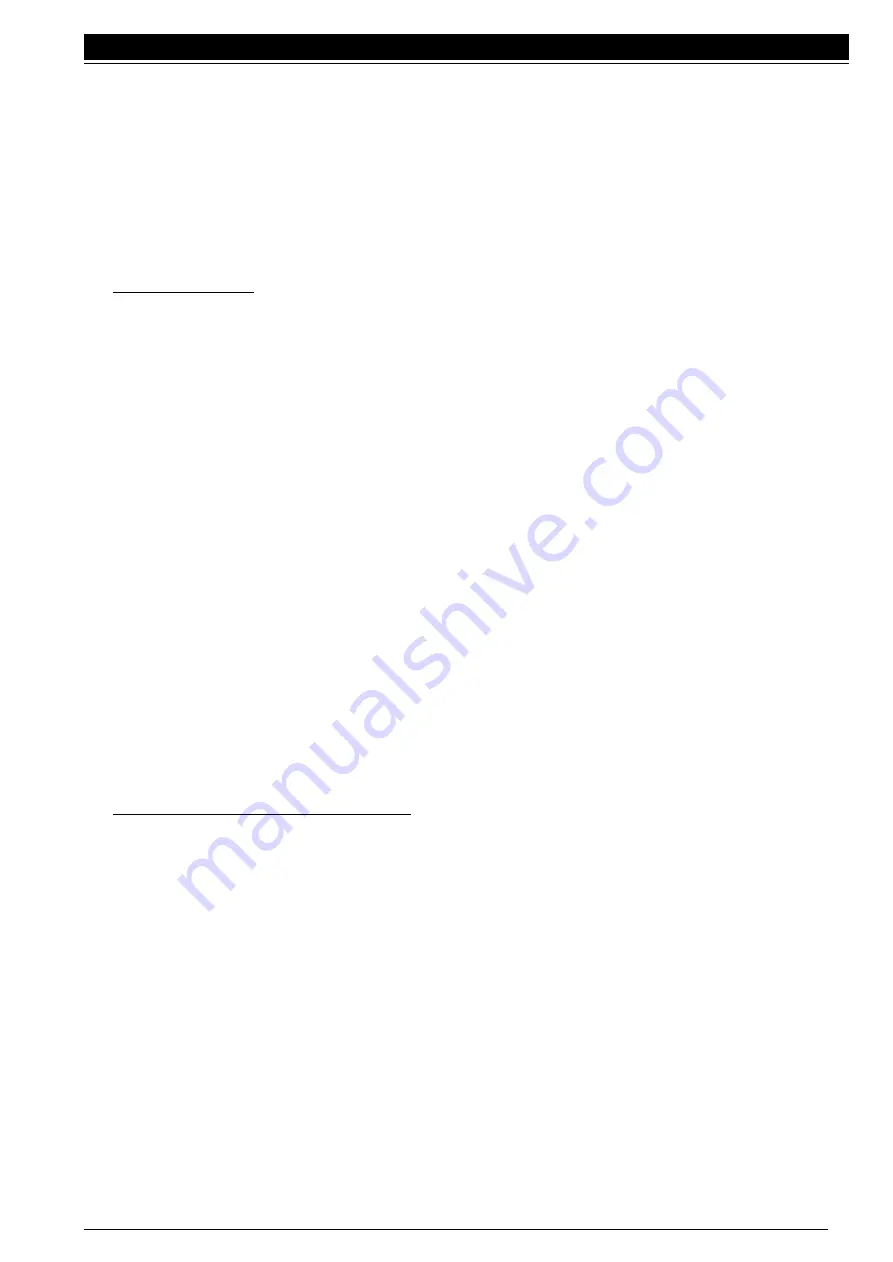
Usually the safety “Photocell” triggers only during the closing manoeuvre and “Photocell2” only during the opening manoeuvre.
If you wish to increase the level of safety it is possible to programme the system to check that the safety devices “PHOTOCELL”
and “PHOTOCELL2”are clear before movement can start.
Switch 10:
On
= Automatic realignment, if required, when power returns
When there is a power cut and the gate/door is without power, the gate/door position reading system loses the distance; in such
circumstances the “Realignment” procedure has been designed that will search for point “C” again. The realignment procedure
is normally carried out when power returns, when the first command pulse is received. With dip-switch n° 10 “ON” realignment
occurs as soon as power returns, without waiting from any command pulse
6.1) FUNCTIONING TESTS:
After the connections have been checked and verified (Chapter 2.4), and the travel limits programming phase has been carried
out (Chapter 3.2 or 4.3.1), it is possible to test actuator movement. We suggest you work in the “hold to run control” functioning
mode with all the functions deactivated (all switches OFF); in all cases, in the “hold to run control” mode, by releasing the
command key, the motor stops immediately. If you use the Step-by-Step input command the first movement (after turning on) will
be an opening manoeuvre. In this phase you will find it extremely easy to use the small keys “OP”, “CL” on the card. By means
of the command inputs, move the gate/door up to the point of opening “A” wanted. About 20 cm before the stop position, the
“slowing” phase must come into play so the gate/door reaches the stop position at a speed reduced by about 30%. Now carry
out a closing manoeuvre up to the point of closing “C” you want. Here too, the slowing down phase should start 20 cm before
the stopping point. Now test triggering of the safety devices: PHOTOCELL in the opening phase has no effect; in the closing
phase it will stop movement; PHOTOCELL2 has no effect in the closing phase; in the opening phase it will stop movement. The
devices connected to the STOP input act both in the opening and closing manoeuvres, stopping movement.
The recent European standards, prEN 12453: safety in using motorised doors - requirements and classifications; prEN 12445:
safety in using motorised doors - testing methods; (not yet approved but they will be in 1998), require the use of measurements
so as to limit the forces involved in moving automatic doors, equal to a maximum of 1400N as the force of impact and a maximum
residual static force of 150N that must be cancelled out within 5 seconds from impact. The
FRIZZ
(clutch) trimmer is on the card
and is used to establish the clutch’s intervention threshold.
As described in Chapter 1.4, the intelligent clutch system calculates to find the average movement speed so it can intervene with
greater precision. To evaluate the effect the adjustment has on the trimmer it is best to wait for movement to start and for the
gate/door to reach standard speed. Also ensure for safety reasons, that if the clutch intervenes three times in a row, movement
is stopped without any reversal.
If the automatic functioning mode is selected, at the end of the opening manoeuvre there is a “pause time” followed automatically
by a closing manoeuvre. Pause time, if not programmed, will be 30 seconds
The pause will also be activated in the semiautomatic movement phase when, in closing, the triggering of a safety device or the
intelligent clutch, causes a reversal in opening.
Only now, when all the adjustments have been made and with the electricity off, do we advise you to connect the radio receiver.
6.2) DESCRIPTION OF THE FUNCTIONING MODES:
In the “hold to run control” functioning mode the OPEN-TIMER input allows movement up to the opening point wanted; the PAR-
OPEN input allows movement up to the partial opening point; STEP-BY-STEP allows alternative opening and closing
manoeuvres; as soon as the command in input stops, movement stops. In the opening phase the gate/door will stop in the set
position or if PHOTOCELL2 is interrupted; in the closing phase movement will stop if the PHOTOCELL input is interrupted. An
action on STOP will cause movement to stop immediately both in opening and closing. Once movement has stopped the
command in input has to be stopped too before any new movements can be started
In any of the automatic functioning modes (semiautomatic-automatic and closes always) a command on the OPEN-TIMER input
will cause an opening manoeuvre; if the command persists after the gate has opened, movement remains “frozen” in an infinite
pause; only when the command stops will the gate/door be able to close. Command pulses on the PAR-OPEN input will cause
an opening manoeuvre only up to the partial opening point. A pulse on the STEP-BY-STEP causes alternative opening and
closing manoeuvres. A second pulse on the STEP-BY-STEP or on the same input that started the movement, will cause a Stop.
STOP will cause movement to stop immediately both in opening and closing.
If in a command input there is a continuous signal instead of a pulse, it will cause a “priority” state which means all the other
command inputs remain disabled (useful to connect a timer or Night-Day selector).
If the automatic functioning mode is being used, subsequent to an opening manoeuvre there will be a pause time followed by a
closing manoeuvre. If, during the pause the PHOTO triggers, the timer will be reset with a new time; if, on the other hand, a STOP
intervenes during the pause, the reclosing function is cancelled and there will be a STOP condition.
Triggering of the PHOTOCELL has no effect in an opening manoeuvre while PHOTOCELL2 causes reversal of direction. In a
closing manoeuvre triggering of the PHOTOCELL will reverse the direction followed by a new pause and then a closing
manoeuvre. If, at the beginning of an opening manoeuvre, the PHOTOCELL input is not clear, the request to open is cancelled.
Eng li sh
2 9